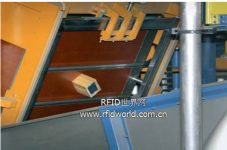
Introduction of SIEMENS RFID application cases in the tobacco industry
[ad_1]
one.Preface
With the continuous improvement of the level of automation in cigarette production, tobacco industry companies have continuously improved production efficiency through the use of new equipment and technological transformation, ensuring product quality, and establishing a modern logistics management system for tobacco companies to play a very important role.
The logistics of the tobacco industry can be divided into the internal logistics of the manufacturer’s production process, that is, the industrial logistics and the commercial logistics of the finished tobacco sales link. As an advanced automatic identification technology, RFID has been widely used in the field of tobacco logistics, which can greatly improve the efficiency of logistics management and operation, and reduce logistics costs.
SIEMENS RFID system as an industrial grade product has a wide range of applications in the tobacco industry. For example, it is applied to the automated recipe library of tobacco leaf, the shredded tobacco library, the auxiliary material library, the finished product library, and the spare parts library to realize the digital automatic storage of raw and auxiliary materials and the automatic production of cigarette logistics automation system.
According to the technological process of cigarette production, RFID can be applied to automatic leaf storage, automatic premixing of tobacco, and automatic unpacking of tobacco leaves and automatic recycling of packaging materials in the process of cigarette making. RFID can be used for automatic supply of shredded tobacco, automatic storage of filter tips, automatic transportation and data collection of cigarettes and finished cigarette boxes, automatic palletizing and unstacking of finished cigarettes, and so on.
At present, in order to meet the needs of the national tobacco industry’s “No. 1 Project” and realize the information tracking management of the whole process of production and distribution of finished cigarettes, more and more tobacco manufacturers are adopting automatic sorting of finished cigarettes with RFID technology as the core. The delivery system organically integrates the production links of cigarettes with the commercial links, which not only improves the production efficiency of the enterprise, but also improves the logistics efficiency and information system management of the finished cigarette distribution and sales links.
The following introduces some typical cases of SIEMENS RFID application in the tobacco industry.
two. Introduction to Typical Cases of SIEMENS RFID Tobacco Industry Application
Case 1: SIEMENS Moby E realizes the automated management of the tobacco recipe library
one.Overview
In a tobacco factory’s cut tobacco warehouse, the pre-prepared tobacco cuts with different formulas are automatically stored in a cut tobacco box, and the SIEMENS Moby E radio frequency identification system is used to confirm the box number and cigarette brand. By automatically checking the cut tobacco in the tobacco box Identification, to realize the flexible production of the shredded tobacco batching process.
two.client needs
The factory produces many different brands of cigarettes, derived from different shredded tobacco recipes. In order to solve the contradiction between large-volume silk production and small-batch, multi-brand package production, according to the requirements of package production, precise process control such as the use of tobacco shreds, the recovery and storage of residual materials, and the rejection of unqualified products are realized. A box-type tobacco storage scheme is adopted. Because shredded tobacco of different ingredients cannot be distinguished manually from the appearance, RFID is used to identify the brand of tobacco in the shredded tobacco box, which can effectively avoid the mixed tobacco branding and wrong branding caused by the wrong feeding point of the cigarette box. Quality accident.
three.solution
There are about 1,200 shredded tobacco bins in the shredded tobacco library, each shredded tobacco bin stores about 180Kg of shredded tobacco. RFID is used to reliably identify batch production information in the entire process from the ingredients of various tobacco leaf materials to the delivery to the cigarette equipment.
The shredded tobacco warehouse is divided into three process sections: warehousing, warehousing and box turning. The main process of the inbound section is boxing of shredded tobacco, and the outbound section mainly realizes the sampling and exiting and returning of the cigarette boxes; the box turning section mainly completes the procedures such as box turning and dumping and brand checking.
(Picture 1)
As shown in Figure 1, a Moby E E611 data carrier is installed at the bottom of each tobacco box.
In the mixing section of the silk production line, cigarette boxes with different tobacco grades are transported to different tobacco feeding points. After completing the packing cloth process, the system writes the weight, batch, brand, and cigarette box number of the shredded tobacco into the RFID data carrier on the cigarette box through the RFID reader to complete the storage process.
When shredded tobacco is out of the warehouse, check the tobacco grade before turning over the box. When the cigarette box is transported to the RFID reading and writing station in front of the box turning machine, the control system reads the tobacco grade stored in the RFID and compares it with the commissioning grade issued by the dispatching system. When the tobacco grade and box number are consistent with the system requirements, Carry out the operation of turning boxes and dumping materials to complete the outgoing process.
Four.Customer benefits
1. Through reliable identification of the cigarette box, a fully automated production process of mixed-line production of shredded tobacco of various brands of cigarettes and warehouse management on the same silk-making line is realized.
2. To ensure the correctness of the shredded tobacco supply, to avoid quality accidents such as mixed tobacco branding and wrong branding caused by the wrong feeding point of the cigarette box, and the remaining raw materials can continue to be recycled, stored and reused.
3. Realize the real-time monitoring and synchronization update of logistics and information flow through synchronization with MES and ERP systems.
Case 2: SIEMENS MOBY D in a cigarette factory
Application in the Management Information System of the Standing Warehouse of the Mouth Stick Production Workshop
In the warehouse management information system of the filter rod production workshop of a cigarette factory, Kunming Shipyard adopts the MOBY identification system of SIEMENS Company to track and manage the production and quality of the mouth rods in the fully automated process of storage and delivery. , Improve the production efficiency and the accuracy of information management, and realize the effective control of product quality.
one.Project Overview
The PLC part of this system adopts the SIEMENS SIMATIC S7-400 series, and the field bus part adopts the Siemens distributed I/O equipment ET200M that supports the PROFIBUS protocol. At the storage end of the mouth rod production, the mouth rods are processed and formed, loaded into plastic pallets, and transported to the vertical warehouse for storage. At the end of the mouth bar transfer and delivery, the pallet is taken out of the vertical warehouse and transported to the mouth bar transmitter to realize the process of the mouth bar leaving the warehouse. The whole process has realized the whole-process tracking management of the mouth stick production information.
two. MOBY application examples
In this project, MOBY D is mainly used in the identification of the inbound and outbound of the mouth stick in the pallet. By installing SLG D12S read/write equipment on the inbound device and the outbound device, install MDS paper smart labels (mobile data storage) on the side of the pallet. At the inbound end, when the pallet passes through the read/write device, The production and quality information of the mouth stick is written into the electronic label on the corresponding pallet. At the outbound end, when the pallet passes through the read/write device, the electronic label information on the pallet is read out and combined with the data in the database. The information is compared, and if the information matches, it indicates that the goods out of the warehouse are correct.
The MOBY system effectively links the production and quality information in the production process of the mouth stick production, warehousing, storage, and delivery, and realizes the automatic and non-contact reading of the information, and realizes the production warehousing and adjustment of the mouth stick. The automated control and management of the goods out of the warehouse process ensures the completeness and correctness of the production information and quality information in the entire process.
Case 3: SIEMENS Moby E realizes the automatic storage management of cut tobacco warehouse
one.Overview
In a tobacco factory’s cut tobacco warehouse, the pre-prepared cut tobacco with different formulas is automatically stored in a tobacco box, and SIEMENS’s Moby E radio frequency identification system is used for packing cloth, warehousing storage, cigarette box exporting, and turning over. The confirmation of the box number and the tobacco brand and weight in the links of box feeding and surplus material recycling has realized the automated production of the storage management of the tobacco production process. Figure 4 shows the layout of the entire shredded tobacco library.
two.client needs
Due to the use of the tobacco box storage scheme, the tobacco of different ingredients cannot be distinguished manually from the appearance. Therefore, RFID is used to automatically identify the tobacco brand and other information in the tobacco box, which can effectively prevent the tobacco box from being sent to the wrong feeding point The quality accidents caused by shredded tobacco mixing, wrong branding, etc., cooperate with the use of automated logistics equipment to ensure the consistency of the shredded tobacco in and out of the warehouse with the production scheduling, and complete the automated operation of the tobacco production and storage and the automated management of production information.
three.solution
The reader is installed at the lower part of the conveyor, as shown in Figure 5, to complete the writing and reading of information on the tobacco box. An electronic tag is installed at the bottom of each cigarette box to store information such as the variety, grade, weight, time of entry and exit, and box number of the tobacco leaves.
In the feeding link, the upper management system assigns a certain storage lane in the storage area to discharge the tobacco box to the outbound shuttle car according to the principle of first in, first out. A Moby E electronic tag reader is installed on the outbound shuttle. Check the electronic tag information on the box to confirm whether it is consistent with the scheduled information. If the information is consistent, it will be shipped out normally; if the information does not match the scheduled information, it will be returned After the original storage channel, the shredded tobacco consistent with the predetermined information is output again.
[ad_2]