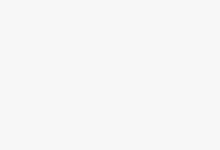
Liverpool: Seamless connection from barcode technology to RFID technology
[ad_1]
The application of the GS1 system enables Liverpool to share information with global suppliers, and achieve a seamless connection from barcode technology to RFID technology.
Liverpool is a giant in the Mexican retail industry, with total sales exceeding US$5.2 billion in 2012. Its storage and transportation center (DC) in Turtitlan, Mexico is responsible for the company’s supply chain operations.
Beginning in 2002, Liverpool began to rapidly expand its stores, with 5 to 7 stores opening every year. In order to adapt to this growth trend and prepare for future development, Liverpool needs to re-engineer the operation process of its storage and transportation center. The original purpose of its transformation is to optimize the company’s warehousing process through an automated warehouse storage system and improve operational efficiency. On the basis of achieving this goal, the company is also committed to transforming its inventory management and optimizing its receiving and distribution processes. The reasonable application of this technology will bring maximum benefits.
Optimize the supply chain with RFID technology
In 2002, Liverpool started its supply chain optimization project with the aim of achieving the following goals:
• Improve the visualization of products in the supply chain;
• Reduce box or pallet level distribution errors, especially reduce the error information related to the product in the package or the shipping destination;
• Improve inventory accuracy rate;
•Reduce the loss and backlog of products in plastic packaging or containers;
•Improve inventory speed;
•Reduce cost waste caused by delivery errors.
When looking for the right technology to achieve the above goals, Liverpool considered radio frequency identification technology (hereinafter referred to as “RFID”) as the first choice. After preliminary evaluation, when the project started, the company decided to adopt RFID technology based on the GS1 EPC (Electronic Product Code) standard, and adopted a step-by-step implementation strategy, starting from the pilot, and gradually improving and achieving success through continuous accumulation and learning.
In the initial assessment, Liverpool Company evaluated the EPC on the standard plastic box packaging RFID tagsConduct a feasibility test. This kind of packaging box will be widely used in storage and transportation centers and transportation processes as a logistics unit. The result of the test is the standardized transformation of plastic packaging boxes, so that assets can be reused in the supply chain, and the added value of supply chain operations has been increased.
From trial to coverage of all products
The pilot project aims to verify the use of EPC RFID technology in the following links through the accuracy test of reading 100 plastic packaging box labels:
• Receiving: receiving products sent by suppliers;
• Integration: according to specific order requirements, verify the products in the box;
• Delivery: The products are shipped to various stores.
Liverpool believes it is necessary to develop a code for the label on the plastic box packaging. At the same time, the company should evaluate and compare the effects of implementing standardized coding and custom coding.
The biggest benefit of the GS1 EPC standard chosen by Liverpool is that it is widely used for data exchange in the supply chain, whether in Mexico or other parts of the world. As a global standard, GS1 EPC provides Liverpool with the foundation and potential to obtain economic benefits and meets the company’s strategic requirements for sustainable development.
For project management, three technology companies were invited to participate in the establishment of a proof of concept (hereinafter referred to as POC). One of the companies is responsible for the installation of EPC RFID reading points for the three links of receiving, integrating, and shipping the Turtitlan storage and transportation center.
Liverpool learned from the POC of the project that it needs to establish an EPC RFID channel so that the correct reading rate of the plastic packaging box labels in the incoming and outgoing links can reach 99.9%.
At the end of the pilot project in 2007, Liverpool decided to expand the use of EPC RFID technology in the storage and transportation center to include three entrances in the receiving area, three reading points in the integration area, and all exits in the shipping area. EPC RFID tags are currently used on plastic packaging boxes for all products.
In addition, a new receiving model “SEMI” was also used for the first time on cartons with product labels. Unlike the plastic box receiving method called “PLANO”, the label attached to the carton is a single-use EPC RFID tag.
EPC RFID technology application has achieved remarkable results
In 2008, Liverpool began testing EPC RFID single-product-level tags of different manufacturers and product categories. In just four years, the use of this technology has expanded from the company’s 4 storage areas to 70; from the initial 2 suppliers to 150; from only 2 stores to 96 stores. At present, the main item-level labelled products are textiles, clothing and bedding.
Through EPC RFID item-level labeling, a series of valuable information is generated from the receiving point of the goods to the delivery, which enables Liverpool to better arrange the goods and ensure that the goods are delivered to the correct location.
Currently, 96 Liverpool stores have benefited from the implementation of EPC RFID technology, especially in the management of warehousing cycle inventory. In addition, 263 EPC RFID mobile readers are deployed in its stores. In this way, as long as EPC RFID tags are used on products, solutions such as smart shelves or smart settlement can be adopted to enhance consumers’ shopping experience. Currently, Liverpool is promoting this project to other product categories, such as furniture and kitchenware.
[ad_2]