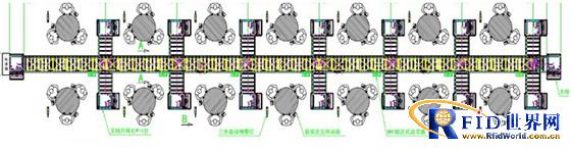
RFID automatic sorting project of a toy company
[ad_1]
1. Project background
A toy company is the world’s largest toy seller, and its series of products sell well all over the world. In order to reduce material distribution errors on the production line and improve the efficiency of material distribution on the production line, the company decided to build an automatic material delivery system (Torsoparts-Vision delivery System).
2. System description
By installing a data interaction terminal and a numerical control alarm light for each production workbench, employees can make a lack of material call through the data interaction terminal, and at the same time, the RFID alarm light will light up and send out a lack of material alarm buzzer.
An industrial PC is deployed at each replenishment station. The lack of material call requests will be automatically queued and displayed on the display screen in chronological order; the replenisher fills the material with theRFIDThe labeled material bowl is then placed on the replenishment level conveyor belt, and the industrial control system (PLC) is driven and controlled by the system. The system directly transports the material bowl to the target shortage station. At this time, the material receiver The handheld device receives the material arrival prompt (vibration), and the material receiver can carry out the material collection according to the displayed information to the designated location.
3. Construction purpose
The system is mainly used for the automatic distribution of production line materials, with main business functions such as lack of material call and automatic material transmission;
The system is transmitted to the working location through the production line, which reduces manpower on the one hand, and on the other hand, the system eliminates the problem of material distribution errors through the comparison and analysis of the identification of the material label and the information of the system issued;
The system uses automatic segmentation control of the production line control system (PLC). When the material arrives, the production line is automatically opened, and the production line is automatically closed when it leaves. In this way, the purpose of energy saving and cost reduction is achieved;
Through the application of the system, the comprehensive analysis of people, machines, materials and methods in the production process is realized, the accuracy and real-time of data are improved, the accurate performance evaluation of employees is realized and the production decision data is provided for managers to use.
4. System Architecture
This system is a distributed system, and its network deployment structure is as follows:
System advantages:
The system realizes the perfect combination of RFID technology and PLC control system through network connection, realizes the networked control of the entire system, improves the scalability and ease of use of the system, and provides sufficient conditions for remote control, viewing, and maintenance of the system operation ;
Through the construction of this system, the cost of material distribution in the customer’s factory is reduced, the error of material distribution is eliminated, and the accuracy and real-time of production data collection are improved at the same time.
[ad_2]