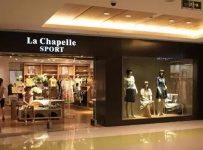
RFID technology has been used in all channels of La Chapelle’s brands
[ad_1]
La Chapelle Group uses RFID to open up the omni-channel data chain, improve the efficiency of each link, and realize product sharing with accurate data, and multi-node data collection provides the basis for big data analysis. Cinda IOT once again successfully cooperated with apparel brands to launch RFID technology in the apparel industry to promote the upgrading and application of the industry. This cooperation promotes the cross-border integration of the retail industry and the Internet of Things, and further creates a harmonious ecosystem in the “chip” era.
In 2016, La Chapelle Group established a plan to introduce RIFD technology for all its brands, including labeling of garment factories, logistics center collection and delivery, fast store receipt, inventory and intelligent management.
Since the spring of 2017, Laxia has fully introduced RFID washing and labeling, and processing and labeling in the garment factory. This link standardizes the production process of the garment factory through the RFID washing label, and uses the RFID flat panel inspection equipment to carry out the packing inspection of the garments, which strengthens the quality inspection process before shipment, and reduces the situation of over-packing, under-packing and wrong packing. . In the logistics center, the product information can be quickly read through the channel machine to improve the efficiency of receiving goods, to prevent the occurrence of stringing, lack of goods, etc., to achieve 100% data inspection, to avoid some errors caused by traditional random inspections that cannot be discovered in time, and it is not easy to hold accountability afterwards The problem. Before the goods are shipped out of the warehouse, they are verified by the delivery review tablet, which ensures the accuracy of delivery and greatly improves the delivery efficiency.
After the goods arrive in the store, the store clerk uses the professional reading and writing device SWING-U to conveniently receive the goods. Realize the inventory of goods without opening the box, and realize real-time docking with the back-end system through a customized mobile APP, update data and receive information. After receiving the goods, the store product information is uploaded to the company server, and the store data update is completed. In the inventory link, according to the inventory plan provided by the company, the inventory is carried out in a targeted manner, and timely and accurate data are provided for the company to carry out related business. The use of smart fitting rooms improves the user experience of customers, and at the same time facilitates back-end customer flow statistics, which is a powerful tool for building marketing big data. The application can also realize real-time docking with the background system, update data and receive information in time. In this regard, the clerk said that the application of new technology has reduced their work intensity, improved work efficiency, and saved more time and energy to better serve customers and increase sales.
[ad_2]