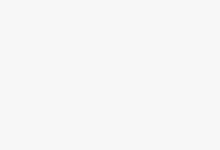
RFID technology successfully improves the efficiency of military uniform orders
[ad_1]
Warmkraft, a military uniform supplier in Mississippi, applied radio frequency identification technology to the shipment of item-level clothing, saving 50% of freight labor costs, reducing the error rate from 5% to 0.2%, ensuring the accuracy of orders, and installing the system. The completion time of the later order was two weeks earlier than the previous one. The system is provided by SimplyRFID Technology Corporation. The use of EPC Gen 2 tags in the supply of military uniforms has reduced the packing error rate by 96%, and at the same time reduced the labor in the shipping process.
Since November 2009, Warmkraft began to provide labeled clothing for the United States Air Force (USAF). Currently, the two suppliers of the company in Mississippi have implemented the labeling system required by the U.S. military department. The labelled clothing is not only supplied to the Air Force, but also And it has expanded to the US Marine Corps (US Marine Corps). The U.S. Air Force’s item-level RFID deployment is designed to help the U.S. Defense Logistics Agency monitor the reception and distribution of uniforms at the recruit training center at Lackland Air Force Base. Ron Lack, general manager of Warmkraft, said: In the next year, the company plans to provide labeled uniforms for the US Army.
As a supplier, Warmkraft buys military uniforms from clothing manufacturers, which need to be repelled, waterproofed, and wrinkled before being shipped to the military logistics procurement office. After random checks, they are finally sent to soldiers. Before installing the RFID system, these processes need to be carried out manually. Once the purchasing department finds an error, this batch of orders will be returned and checked one by one. The work efficiency is very low. As an intermediate supplier, it is important to ensure the accuracy of orders.
Avery Dennison AD-223 inlay
Warmkraft hopes that the RFID system can be fully utilized. In order to increase the tag reading speed at Stonewall’s second-largest supply center, the company outsourced software installation to SimplyRFID. However, the first Taylorsville system installed by the company mainly includes three parts: RFID tags, readers and web-based software systems. The shortcomings of this system are mainly manifested in: first, the accuracy of label reading is not high, how to ensure the accuracy of the reading of the goods labels moving on the conveyor belt is a big problem; second, the web-based server has an impact on the Internet network. The connection is highly dependent. Once the network is disconnected, the entire system will not work.
The Knox software developed by SimplyRFID is used to manage local data without a network connection. In addition, this programmable software can be used to detect whether the garment is labelled. Through the two label information readings with different times, it is detected whether the goods are moving with the conveyor belt.
RFID channel reader above the conveyor belt
The AD-223 RFID tag of Avery Dennison is used in the system. The company uses Zebra Technology’s R110Xi label printer to print ultra-high frequency (UHF) passive labels. The Knox software stores the ID numbers of all tags and the stock keeping unit (SKU) of the tagged clothing. The clothing is boxed and put on the conveyor belt. When passing through the read-write channel, the tag ID is read to determine whether the ID corresponds to the inventory unit stored in the database. If there is a mismatch, the Zebra 105SL printer will automatically print a “unqualified” sign on the outside of the box to remind the staff to replace it in time to ensure the accuracy of the order.
The carton reaches the pallet via the conveyor belt, and the reader around the pallet only reads the label code on the carton (as for the single-product label of the clothing in the box, it is no longer read).
The lower left corner is the reader at the tray
Similarly, the logistics department will read the label information during the inspection process when the order is received, and then pay after the order is confirmed.
Warmkraft staff will also use Integrated Systems Limited (CSL) handheld readers to read pallet and carton labels.
The deployment of this system has brought huge benefits to the entire supply system. However, the cost of a label is about 15 cents, which is still not a small challenge for widespread adoption. Under normal circumstances, the company buys 1.5 million tags per year, and this number will increase significantly, and the total cost will continue to rise. If the military does not enforce the use of RFID, the company may not continue to use item-level tags.
[ad_2]