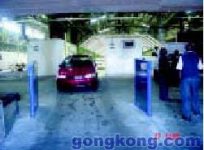
Application of HS800 series of EMS active readers on Ford engine production line
[ad_1]
Ford Motor Company’s Essex engine plant is located in Windsor, Ontario, Canada. The factory produces 11 different car engines with a wide range of types, such as manual and automatic gears, 3.8 liters and 4.2 liters, 00 and 01 models, South American and North American standards.
In order to strictly control the production quality of Ford’s Essex engine plant with an annual output of approximately 700,000 engines, Ford needs an automated data acquisition system to ensure product tracking and quality.
Mr. Michael Loch, a technical sales representative of Trade Electric (integrator of Ford’s Essex automation system), said: “Ford needs a tracking and identification system that can be used to store manufacturing information, such as whether the piston is installed in the correct position or whether the nut is tightened with the right torque. “Michael Loch added: “The system must be able to withstand harsh environments. The tracking mechanism must be able to withstand the same environmental conditions as engine machined parts, usually through a hot cleaning fluid spray, and then at a high temperature of 140 degrees Fahrenheit. Dry it down and spray it with oil at the end. Just as important, the system must be able to interface with Allen-Bradley’s PLC5.”

Dave Mathias, head of the Ford Essex electrical group, pointed out: “The HS208R readable and writable code carrier of EMS left us a deep impression. This code carrier has the fastest reading and writing speed and sufficient storage space, and it is packaged In a sturdy industrial-grade housing. The facts have proved that this kind of code carrier is extremely reliable, they usually need to be exposed to hot water, grease, soap, noise, and vibration resistance.
Tim Eisler, the sales manager of EMS, described the application of the identification system at the beginning of the manufacturing process as follows: “After the engine has completed the piston drilling station process, the code carrier bracket is directly installed on the engine slide, and the carrier The communication between the code bodies is the HS500A read-write antenna of EMS. At the beginning of the manufacturing process, the HS500A antenna writes the serial number and model data into the code carrier.”
Trade Electric’s Michael Loch further explained: “When the engine is transported to the assembly line, where multiple lines cross (such as cam lines and piston lines), the data in the engine’s code carrier is transferred to the code installed on the engine tray. Body.

An antenna reads data from the engine code carrier, and transmits the data to PLC 5 through the HS880B controller of EMS. HS880B is directly connected with AB’s PLC 5 through AB’s 1771DB interface module. The same data is sent to the code carrier on the engine tray via another antenna.
In the process of about 2000 processes, manufacturing process data indicating “pass or fail” will be written into the code carrier. Whenever a process is completed, the antenna is about to write the manufacturing data into the code carrier. When the engine tray approaches the next workstation, the antenna reads the code carrier and confirms that the engine has successfully completed the previous process. If the information read on the label is “failure”, the engine will continue to walk through the production line, but it will not be processed at the subsequent workstations until the repair port (repair point). Ford’s Essex engine plant uses an RFID system to streamline the engine repair process. If an engine fails the final test, engineers can determine where the problem is without disassembling the engine. The cause of the failure can be determined by analyzing the manufacturing data in the RFID code carrier.

Dave Mathias pointed out when reviewing the development process of the identification system, “Several years ago Ford used barcodes to track the production process of engines, but barcode labels cannot be used in harsh environments, and you cannot write data on barcodes. In contrast, Yes, you can record a lot of information on an RFID. In fact, we only use half of the storage space of the HS208R tag, which provides us with a lot of room for expansion.”
Jim Kott, spokesperson for data collection at AB Rockwell Automation, also agrees: “AB and its Encompass Partner-EMS, together promise users to provide automation solutions based on RFID technology.”
[ad_2]