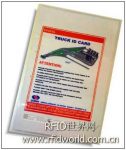
Cimko Cement Plant uses RFID to speed up truck loading
[ad_1]
γγA cement factory in northern Turkey uses an RFID system to speed up the weighing and loading process of hundreds of trucks per day.
The daily operations of the Cimko Cement Narli plant are very busy. Cimko, a joint venture between Turkey’s Sanko Holding and Italy’s Cementerie Aldo Barbetti, opened this fully automated new factory in early 2008.
However, the company’s management quickly discovered that the loading process was a major bottleneck in the plant’s operations. When the truck enters the factory, the driver must get out of the truck to register, receive the paper loading documents, then weigh, and then load the goods into the cement warehouse-a process that is quite time consuming, according to Erdal Tokat, Cimko IT project manager.
Therefore, Cimko decided to adopt a passive RFID system to manage the flow of trucks in and out of the factory. The company hired Meyer RFID, a Turkish RFID manufacturer and a member of the Siemens Solution Provider project, to implement a system that used 24 Siemens RF600 readers and 48 antennas.
Cimko truck ID card with Alien Technology EPC Gen 2 RFID tag
“It is not easy to adopt passive RFID in this environment because the project is huge,” said Onur Bayindir, general manager of Meyer RFID, referring to the large area of ββthe Narli factory. Although active RFID tags are usually more suitable for large areas, the price of active tags is $25 each, which is too expensive for the Narli factory, which handles hundreds of trucks at a time.
Now, truck drivers entering the factory will receive a truck ID card containing Alien Technology UHF Gen 2 EPC RFID tags, operating at 866MHz. The price of the ID card is less than $1.4 each, according to Bayindir. Now, the Narli factory has a total of 500 cards to cope with peak demand.
When the system recognizes the truck, the LED instructs the driver to drive into the correct loading platform
With this new system, the driver does not need to leave the cab to register. Moreover, the company’s Microsoft SAL database will automatically generate a record to store customer information, including the type and quality of cement purchased.
When the truck approaches the factory, the gate opens, the vehicle enters the factory, and arrives on a set of scales; at this time, a Siemens RF600 reader is activated and starts searching for tags. After the tag is recognized, the truck is automatically weighed, and its empty weight is displayed on an LED that the driver can see. When a truck was successfully weighed, the driver received a green light and drove into the cement loading warehouse.
When the truck is identified and weighed, a series of large LED panels instructs the vehicle to go to the correct feeding station to load packed or unpacked cement. The Siemens RFID reader at the feeding station reads the truck’s tag to determine whether the vehicle is authorized to enter. If the verification is passed, the system removes the roadblock and allows the truck to enter.
If the loading dock RFID reader recognizes that the approaching truck is authorized to load cement, the gate opens automatically
After the loading is complete, the exiting truck passes through another set of scales. The vehicle is identified by the RFID tag again to ensure the correct quantity of cement loaded. The empty weight of the truck is compared with the weight after loading. If the quantity is correct, the system lights up green, allowing the truck to leave the factory.
When the truck is filled with cement, it returns to the weighing platform, and the RFID reader is automatically activated to identify the tag
“Now, the throughput of the factory has increased by 15%-20%,” Tokat said. “The factory operates at full capacity 24 hours a day, seven days a week.” In particular, he said that the weighing process is nearly 10 times faster than before.
According to Tokat, the implementation of this system took only three months, and the company began to install it on January 10, 2009. A total of 10 Cimko employees and 5 Meyer RFID employees were employed.
The cost of this project is US$414,000, which does not include the labor cost of Cimko’s IT department, who wrote most of the software for the weighing system and RFID system.
So far, Tokat said that he and his colleagues are very satisfied with the project. Although he declined to disclose the return on investment, he said that the system has greatly improved the efficiency of the factory.
[ad_2]