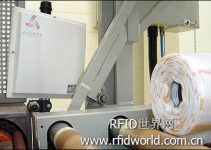
Italian textile manufacturers use RFID to track the production process of work-in-progress
[ad_1]
Griva, a textile manufacturer near Turin, Italy, uses RFID to solve the inefficiency of the WIP tracking system. According to Alien’s vice president of marketing, Ronny Haraldsvik, Griva has achieved a return on investment within nine months of adopting the RFID system.
Alien ALR-8800 reader mounted on the conveyor belt
In Griva’s 1,000-square-meter automated factory, Griva produces approximately 300,000 rolls of textiles every year. According to Stephen Crocker, Alien’s European market channel management director, the raw materials are woven into textiles and then cut and rolled into a roll on durable paper or plastic reels. In 15 separate dyeing and coating processes, the machine automatically unwinds the woven roll for processing, and then rewinds, and the entire processing process is fully automated. Each volume is identified one by one in each process. The system uses Alien’s RFID hardware and Simet’s middleware. Simet is an Italian RFID system integrator and middleware provider.
Before adopting the RFID system, Griva posted a bar code on each reel to be processed; bar code scanners were installed on the conveyor belt. When the conveyor belt transfers the web from one process to the next, the scanner reads the barcodes one by one. This generates raw product processing records so that Griva can track the production process. However, in the high temperature and harsh industrial manufacturing environment, the bar code sometimes appears blurred, resulting in failure to read. In this case, the staff has to manually read and record the ID number of the web.
Even if the barcode can be kept intact during the manufacturing process, when the roll enters the final processing stage-the machine wraps the roll with plastic film, the difficulty of reading the barcode is further increased. Because the barcode reading requires a clear line of sight, the plastic film tends to stretch the barcode, making it difficult to read. In fact, Crocker claims that the original system can only read 70% of stretch-wrapped webs.
Now the staff puts a label with passive EPC Gen 2 Alien Squiggle inlay on the reel. When each roll of textile completes a processing flow, an Alien ALR-8800 reader reads the EPC number of the label. Simet’s RFID middleware filters repeated readings and transmits the ID number of the tag to Griva’s production tracking system.
Griva puts a label on the reel with EPC Gen 2 Alien Squiggle inlay
Griva could have used high-frequency tags and reader tracking systems instead of UHF EPC tags now, Crocker said, because the application does not require distance reading. However, manufacturers hope that their partners will also adopt EPC in the future so that the company can track textile rolls in the supply chain.
The increased reliability of the identification system reduces labor costs. Enable Griva to track the production process of the production line at the fastest speed. This gives Griva a 30% return on investment.
[ad_2]