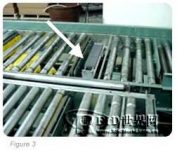
Johnson Controls company car seat cover production RFID application case
[ad_1]
It is pleasing to observe that a mass of ordinary foam becomes a car seat in the engineer’s perfect work. Manufacturing a car seat that makes users feel comfortable is as complicated as manufacturing a high-performance car, and requires multiple processes to complete before being transported to the end user for assembly.
Johnson Controls of Livermore, California, supplies car seats to the car manufacturer NUMMI (New United Motor Manufacturers Incorporated). NUMMI is a joint factory established by Toyota and General Motors. Johnson Controls of Livermore provides a wide range of car and truck seat models.
NUMMI adopts the JIT (Just-In-Time Production) system pioneered by Toyota Japan to produce a variety of models of cars. The JIT production system eliminates its own parts inventory, and requires all its suppliers to supply parts in a timely and accurate manner according to their own production needs. part. The implementation of the JIT production system can reduce inventory and eliminate overdue storage of parts, which requires suppliers to respond to orders and deliver timely and accurately.
In order to meet NUMMI’s supply requirements, Johnson Controls transports 12 truck seats to NUMMI’s workshop every day, and each batch of goods is required to be directly and accurately delivered to the required production line.
As a supplier of NUMMI, Johnson Controls faces many problems in meeting its JIT requirements. But the most important thing is to respond to the manufacturer’s orders accurately and in a timely manner. NUMMI’s orders are transmitted to the supplier via the network every hour. The order information is in the form of product serial numbers, describing which car seats should be shipped to the factory. Of course, the most important thing is to respond to the order requirements accurately and promptly in the process of processing these orders.
Johnson Controls has two car seat cover production lines: one is a truck seat cover production line, and the other is a car seat cover production line. Both the car seat covers produced on that line are transported to the warehouse through the conveyor belt, and are finally mixed together for storage and packaging. If the order of NUMMI is: car seat cover, truck seat cover, car seat cover, but if Johnson Controls’ order of delivery is: car seat cover, truck seat cover, truck seat cover. When this batch of car seat covers not sent in the order of order arrives at NUMMI’s factory, the production line will be stopped. Any untimely response to orders and errors will result in huge economic losses, so Johnson Controls urgently needs a set of technical solutions to ensure the accurate execution of orders.
Fred Zaske, an engineer at Johnson Controls, explained: “Our previous recognition system only used a handwritten notepad to record the production, inventory, and transportation information of car seat covers. There are huge human errors in manual entry. In order to reduce this human error. So we decided to re-install a new identification system. This identification system must greatly ensure our timely and accurate execution of NUMMI orders.”
Our earliest choice is the barcode recognition system, but the barcode is easily soiled and damaged, which can lead to misreading or unreading. This will cause the production line to stop, and the relatively simple RFID system of the EMS company can avoid all of this and ensure the accuracy of production and operation.
When we decided to use the EMS RFID system, EMS engineers recommended to use HMS series products at the beginning of the project. The RFID system composed of HMS products was first implemented on the truck seat cover production line and warehouse/transportation department, and the HMS code carrier was installed in The bottom of the truck seat cover pallet. First, the truck seat cover production parameters are written into the code carrier, and then in the subsequent process, the HMS827-04 reader reads the code carrier information of each pallet and transmits it to the PLC, and then displays the seat cover production information on the touch screen and operates The worker starts production according to the type of seat cover reflected in the production information, and after completing all the actions to be performed on this station, it enters the next station. The reader writes the production information of all stations into the code carrier. At the last station of the production line, the production operation system checks whether the production information stored in the code carrier is consistent with the information described in the order. If it is consistent, the car seat cover is Send to storage/transportation area.
The Johnson Controls warehouse is also equipped with HMS827-04 readers. Once the car seat cover is checked and qualified at the last station, it is sent to the warehouse through the automatic conveyor system, and is automatically arranged according to the NUMMI order serial number and loaded directly onto the delivery truck. .
An HMS827-04 reader/writer is also installed between the end of the automatic conveyor belt and the delivery truck. When the operator loads the car seat cover into the delivery truck, the HMS827-04 reader is used as the last checkpoint to check whether the model of the seat cover to be loaded on the truck matches the model required by NUMMI’s order.
Successful application of RFID system
Johnson Controls successfully applied the RFID system to replace the manual entry system in the truck seat cover production line and warehouse, and achieved huge production and economic effects. Because of this, Johnson Controls is actively expanding the RFID system to the car seat cover production line and warehouse.
Johnson Controls’ car seat cover production line identification system uses EMS company’s RS read-only series readers and ES series code carriers. The choice of RS read-only series readers and ES series code carriers is based on the following two reasons. One: The car seat cover production line has many processes and the transmission rate is very high. The writing function of the reader is not easy to complete, so the RS read-only series reader is used. Second: ES650 G007 code carrier can be programmed by customers. Johnson Controls uses 1-32 digits of ES code carrier to identify an order number.
The manufacturing process of car seat covers seems to be a fascinating process. The top of the workshop is full of car foam seats that rotate continuously. When it reaches a station, the reader reads the information of the code carrier to see if it is processed at this station. If it needs to be processed, fill some foam such as car seat pillows. , Seat belts, airbags, etc. Each station on the car seat cover production line has a reader to read the code carrier attached to the bottom of the pallet to see if it should be processed at this station.
Johnson Controls can produce multiple models of car seat covers on the same production line. When a seat cover arrives at a station through the conveyor chain, the reader reads the code carrier information. If the serial number of the code carrier of the pre-arranged production program (one serial number corresponds to a seat cover model) indicates that there is no need to do any processing at this station, the production operation system automatically transfers the car seat cover to the next station through the transfer roller , Only the serial number of the code carrier indicates that the seat cover that needs to be processed at this station stops. At each station, the operator obtains the processing information through a touch screen connected to the PLC, and then selects the correct component for processing. With the assistance of workers, the automatic production line completes the production of car seat covers.
The Johnson Controls production and operation system uses RFID to ensure safe and efficient production. When the pallet with the code carrier passes through all the stations, the seat cover can only be processed after the operator checks the seat cover model and selects the correct components. . The Zaske engineer’s evaluation of the safety of the RFID system is “The application of the RFID system ensures that the operator can only process the seat cover by selecting the correct components, which greatly reduces the occurrence of production errors.”
In the next step, the car seat cover is covered with fabric and sewn, and then sent to the monitoring station. After all the manufacturing processes, the car seat cover will pass a series of inspections to ensure that the product is free of defects. After the later maneuvering and strict inspections at multiple inspection stations, some models of seat covers such as airbags will pass other special inspections. Before using the RFID system, a testing station can only detect one type of seat cover, but after applying the EMS company’s RFID system, a testing station can detect multiple types of seat covers, which greatly improves the utilization rate of Johnson Controls’ testing stations. .
After passing the inspection of the car seat cover, wrap it in a plastic paper bag and place the seat cover from a small metal pallet to a larger plastic pallet, and then the pallet is sent to NUMMI’s automobile production line.
EMS company’s HMS series readers and code carriers are also used in the warehousing/transportation department for product tracking. The seat cover is placed on the bottom of the plastic pallet attached with the HMS125 code carrier, and the seat cover passes through the conveyor roller after it is off the line. When read and written by HMS827-04 reader.
Johnson Controls added a function to its RFID system, connecting the car seat cover RFID system with the warehouse management system. When a car seat cover is offline (using the RS read-only series RFID system), the production operation system directly sends the product information to the warehouse management system.
When the car seat cover is placed on the plastic pallet attached with the HMS125 code carrier, the reader will write the seat cover model and production information in the process when it passes through the conveyor roller installed with the HMS827-04 reader Code body. After that, the seat cover has a code carrier as its own “identity tag”, and then the final assembly information is also written into the code carrier when the HMS827-04 reader installed in the storage/transportation line is used. Before Johnson Controls used the RFID system, the products were shipped to the warehouse through conveyor rollers after they were off the assembly line and required an operator to do record statistics. Now the implementation of the RFID system saves the cost of building warehouse inspection stations, which effectively reduces The cost of production and operation of the enterprise.
Technical specifications
Johnson Controls’s car seat cover production line selects EMS company’s RS series read-only code carrier, RS427-03 reader, and ES650 G007 code carrier installed at the bottom of the metal tray. In the early stage of the implementation of the RFID project, a thorny problem was encountered, because the plastic pallet had to be rotated 90 degrees on the production line, so that the reading distance became longer and the reader could not read the code carrier. The on-site engineer came up with a brilliant solution to install 4 code carriers on each plastic pallet. This ensures that no matter how the tray rotates, there is a code carrier that can pass through the reader.
Johnson Controls’ car seat cover production line is equipped with 2 EMS CM52 interface modules to connect 16 HMS and RS readers with the control operation host (Johnson Controls’ production and operation system uses Rockwell and AB’s PLC5S), cars and trucks Each seat cover production line has a CM52 interface module to connect 8 readers.
save time
Zaske explained, “The implementation of the RFID system by Johnson Controls has greatly saved the production time of seat covers and made the production organization more flexible; a variety of seat covers can be produced on the truck and car seat cover production line; in the final storage/transportation link of the production line There is no need to sort the seat covers according to the model requirements of the order; some seat covers that require special processing procedures do not have to be mixed with other ordinary seat covers; if processing is not required in a station, the RFID system will pass The PLC controls the conveyor roller to continue moving to the next station.”
Johnson Controls uses EMS’s 125KHz RS series with high read and write rates and 13.56MHz HMS series RFID products with high storage capacity. Through the organic integration of RFID technology and production operation system, Johnson Controls has established an effective and complete supply chain control system, which greatly improves the accuracy of production and greatly improves production efficiency.
Applied EMS products:
HMS827-05
HMS125
RS427-03
ES650 G007
CM52
EMS company is committed to providing complete RFID solutions for the world’s leading manufacturing companies. Over the past 17 years, we have successfully implemented RFID systems in the supply chain of many industries with a broad RFID product line and excellent solutions. Our Fastrack and HMS The series of readers and code carriers are currently providing high-quality and reliable services to Fortune 500 companies all over the world. If you want to know more about RFID or are interested in the cases you have read, please contact us.
It is pleasing to observe that a mass of ordinary foam becomes a car seat in the engineer’s perfect work. Manufacturing a car seat that makes users feel comfortable is as complicated as manufacturing a high-performance car, and requires multiple processes to complete before being transported to the end user for assembly.
Johnson Controls of Livermore, California, supplies car seats to the car manufacturer NUMMI (New United Motor Manufacturers Incorporated). NUMMI is a joint factory established by Toyota and General Motors. Johnson Controls of Livermore provides a wide range of car and truck seat models.
NUMMI adopts the JIT (Just-In-Time Production) system pioneered by Toyota Japan to produce a variety of models of cars. The JIT production system eliminates its own parts inventory, and requires all its suppliers to supply parts in a timely and accurate manner according to their own production needs. part. The implementation of the JIT production system can reduce inventory and eliminate overdue storage of parts, which requires suppliers to respond to orders and deliver timely and accurately.
In order to meet NUMMI’s supply requirements, Johnson Controls transports 12 truck seats to NUMMI’s workshop every day, and each batch of goods is required to be directly and accurately delivered to the required production line.
As a supplier of NUMMI, Johnson Controls faces many problems in meeting its JIT requirements. But the most important thing is to respond to the manufacturer’s orders accurately and in a timely manner. NUMMI’s orders are transmitted to the supplier via the network every hour. The order information is in the form of product serial numbers, describing which car seats should be shipped to the factory. Of course, the most important thing is to respond to the order requirements accurately and promptly in the process of processing these orders.
Johnson Controls has two car seat cover production lines: one is a truck seat cover production line, and the other is a car seat cover production line. Both the car seat covers produced on that line are transported to the warehouse through the conveyor belt, and are finally mixed together for storage and packaging. If the order of NUMMI is: car seat cover, truck seat cover, car seat cover, but if Johnson Controls’ order of delivery is: car seat cover, truck seat cover, truck seat cover. When this batch of car seat covers not sent in the order of order arrives at NUMMI’s factory, the production line will be stopped. Any untimely response to orders and errors will result in huge economic losses, so Johnson Controls urgently needs a set of technical solutions to ensure the accurate execution of orders.
Fred Zaske, an engineer at Johnson Controls, explained: “Our previous recognition system only used a handwritten notepad to record the production, inventory, and transportation information of car seat covers. There are huge human errors in manual entry. In order to reduce this human error. So we decided to re-install a new identification system. This identification system must greatly ensure our timely and accurate execution of NUMMI orders.”
Our earliest choice is the barcode recognition system, but the barcode is easily soiled and damaged, which can lead to misreading or unreading. This will cause the production line to stop, and the relatively simple RFID system of the EMS company can avoid all of this and ensure the accuracy of production and operation.
When we decided to use the EMS RFID system, EMS engineers recommended to use HMS series products at the beginning of the project. The RFID system composed of HMS products was first implemented on the truck seat cover production line and warehouse/transportation department, and the HMS code carrier was installed in The bottom of the truck seat cover pallet. First, the truck seat cover production parameters are written into the code carrier, and then in the subsequent process, the HMS827-04 reader reads the code carrier information of each pallet and transmits it to the PLC, and then displays the seat cover production information on the touch screen and operates The worker starts production according to the type of seat cover reflected in the production information, and after completing all the actions to be performed on this station, it enters the next station. The reader writes the production information of all stations into the code carrier. At the last station of the production line, the production operation system checks whether the production information stored in the code carrier is consistent with the information described in the order. If it is consistent, the car seat cover is Send to storage/transportation area.
The Johnson Controls warehouse is also equipped with HMS827-04 readers. Once the car seat cover is checked and qualified at the last station, it is sent to the warehouse through the automatic conveyor system, and is automatically arranged according to the NUMMI order serial number and loaded directly onto the delivery truck. .
An HMS827-04 reader/writer is also installed between the end of the automatic conveyor belt and the delivery truck. When the operator loads the car seat cover into the delivery truck, the HMS827-04 reader is used as the last checkpoint to check whether the model of the seat cover to be loaded on the truck matches the model required by NUMMI’s order.
Successful application of RFID system
Johnson Controls successfully applied the RFID system to replace the manual entry system in the truck seat cover production line and warehouse, and achieved huge production and economic effects. Because of this, Johnson Controls is actively expanding the RFID system to the car seat cover production line and warehouse.
Johnson Controls’ car seat cover production line identification system uses EMS company’s RS read-only series readers and ES series code carriers. The choice of RS read-only series readers and ES series code carriers is based on the following two reasons. One: The car seat cover production line has many processes and the transmission rate is very high. The writing function of the reader is not easy to complete, so the RS read-only series reader is used. Second: ES650 G007 code carrier can be programmed by customers. Johnson Controls uses 1-32 digits of ES code carrier to identify an order number.
The manufacturing process of car seat covers seems to be a fascinating process. The top of the workshop is full of car foam seats that rotate continuously. When it reaches a station, the reader reads the information of the code carrier to see if it is processed at this station. If it needs to be processed, fill some foam such as car seat pillows. , Seat belts, airbags, etc. Each station on the car seat cover production line has a reader to read the code carrier attached to the bottom of the pallet to see if it should be processed at this station.
Johnson Controls can produce multiple models of car seat covers on the same production line. When a seat cover arrives at a station through the conveyor chain, the reader reads the code carrier information. If the serial number of the code carrier of the pre-arranged production program (a serial number corresponds to a seat cover model) indicates that there is no need to do any processing at this station, the production operation system automatically transfers the car seat cover to the next station through the transfer roller , Only the serial number of the code carrier indicates that the seat cover that needs to be processed at this station stops. At each station, the operator obtains the processing information through a touch screen connected to the PLC, and then selects the correct component for processing. With the assistance of workers, the automatic production line completes the production of car seat covers.
The Johnson Controls production and operation system uses RFID to ensure safe and efficient production. When the pallet with the code carrier passes through all the stations, the seat cover can only be processed after the operator checks the seat cover model and selects the correct components. . The Zaske engineer’s evaluation of the safety of the RFID system is “The application of the RFID system ensures that the operator can only process the seat cover by selecting the correct components, which greatly reduces the occurrence of production errors.”
In the next step, the car seat cover is covered with fabric and sewn, and then sent to the monitoring station. After all the manufacturing processes, the car seat cover will pass a series of inspections to ensure that the product is free of defects. After the later maneuvering and strict inspections at multiple inspection stations, some models of seat covers such as airbags will pass other special inspections. Before using the RFID system, a testing station can only detect one type of seat cover, but after applying the EMS company’s RFID system, a testing station can detect multiple types of seat covers, which greatly improves the utilization rate of Johnson Controls’ testing stations. .
After passing the inspection of the car seat cover, wrap it in a plastic paper bag and place the seat cover from a small metal pallet to a larger plastic pallet, and then the pallet is sent to NUMMI’s automobile production line.
EMS company’s HMS series readers and code carriers are also used in the warehousing/transportation department for product tracking. The seat cover is placed on the bottom of the plastic pallet attached with the HMS125 code carrier, and the seat cover passes through the conveyor roller after it is off the line. When read and written by HMS827-04 reader.
Johnson Controls added a function to its RFID system, connecting the car seat cover RFID system with the warehouse management system. When a car seat cover is offline (using the RS read-only series RFID system), the production operation system directly sends the product information to the warehouse management system.
When the car seat cover is placed on the plastic pallet attached with the HMS125 code carrier, the reader will write the seat cover model and production information in the process when it passes through the conveyor roller installed with the HMS827-04 reader Code body. After that, the seat cover has a code carrier as its own “identity tag”, and then the final assembly information is also written into the code carrier when the HMS827-04 reader installed in the storage/transportation line is used. Before Johnson Controls used the RFID system, the products were shipped to the warehouse through conveyor rollers after they were off the assembly line and required an operator to do record statistics. Now the implementation of the RFID system saves the cost of building warehouse inspection stations, which effectively reduces The cost of production and operation of the enterprise.
Technical specifications
Johnson Controls’s car seat cover production line selects EMS company’s RS series read-only code carrier, RS427-03 reader, and ES650 G007 code carrier installed at the bottom of the metal tray. In the early stage of the implementation of the RFID project, a thorny problem was encountered, because the plastic pallet had to be rotated 90 degrees on the production line, so that the reading distance became longer and the reader could not read the code carrier. The on-site engineer came up with a brilliant solution to install 4 code carriers on each plastic pallet. This ensures that no matter how the tray rotates, there is a code carrier that can pass through the reader.
Johnson Controls’ car seat cover production line is equipped with 2 EMS CM52 interface modules to connect 16 HMS and RS readers with the control operation host (Johnson Controls’ production and operation system uses Rockwell and AB’s PLC5S), cars and trucks Each seat cover production line has a CM52 interface module to connect 8 readers.
save time
Zaske explained, “The implementation of the RFID system by Johnson Controls has greatly saved the production time of seat covers and made the production organization more flexible; a variety of seat covers can be produced on the truck and car seat cover production line; in the final storage/transportation link of the production line There is no need to sort the seat covers according to the model requirements of the order; some seat covers that require special processing procedures do not have to be mixed with other ordinary seat covers; if processing is not required in a station, the RFID system will pass The PLC controls the conveyor roller to continue moving to the next station.”
Johnson Controls uses EMS’s 125KHz RS series with high read and write rates and 13.56MHz HMS series RFID products with high storage capacity. Through the organic integration of RFID technology and production operation system, Johnson Controls has established an effective and complete supply chain control system, which greatly improves the accuracy of production and greatly improves production efficiency.
Applied EMS products:
HMS827-05
HMS125
RS427-03
ES650 G007
CM52
EMS company is committed to providing complete RFID solutions for the world’s leading manufacturing companies. Over the past 17 years, we have successfully implemented RFID systems in the supply chain of many industries with a broad RFID product line and excellent solutions. Our Fastrack and HMS The series of readers and code carriers are currently providing high-quality and reliable services to Fortune 500 companies all over the world. If you want to know more about RFID or are interested in the cases you have read, please contact us.
[ad_2]