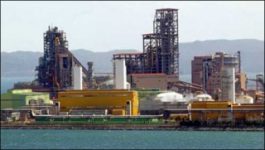
Posco steel manufacturer uses RFID technology to improve plant safety
[ad_1]
South Korean steel manufacturer Posco Steel introduced RTLS (Real Time Location System) to reduce accidents, improve the safety of employees and visitors, and reduce energy consumption.
Posco is the world’s fourth largest steel manufacturer, and its finex process manufacturing plant in Pohang, South Korea has more than 500 employees. The machinery and equipment in the factory and the iron melting process have created a dangerous working environment.
To ensure the safety of employees and visitors, Posco has introduced a system called u-safety management system, which uses ultra-wideband RFID tags and readers to keep track of the status of each area in the factory. All personnel entering the factory are required to wear safety helmets embedded with active RFID tags. Managers can always know the safety of all personnel and confirm whether they enter the accident area, such as fire or gas leakage.
Posco Steel said that the purpose of introducing this technology is not to monitor the actions of employees, but to ensure the safety of everyone. The system can grasp whether the personnel in the factory and the truck enter the dangerous area. Posco Steel Co., Ltd. cooperated with South Korea’s IBM. The two parties conducted tests on real-time positioning systems and software to determine the reading distance and reading rate of tags and readers.
Because the factory is made of metal materials, which shortens the reading distance of the reader, it is necessary to add several readers; and there is a furnace in the factory, so the readers and tags must be resistant to high temperatures. Finally, it was decided to install the reader at the entrance of each staircase.
IBM said that the introduced solution contains two important systems-a real-time positioning system based on RFID technology and LAS (location awareness services).
Posco Steel uses Ubisense’s real-time positioning system solution with 7000 series RFID tags. The tag can transmit 6 to 8 gigahertz signals per second. The reader receives the signal, confirms the location where the tag signal is sent, and then uses the LAN (local area network) to send the message to the LAS middleware.
The WebSphere Sensor Events system developed by IBM can recognize the number code issued by the label. After determining the location of the tag, the complex event processing system (complex event processing) will then confirm whether an accident has occurred in the area to sound the alarm. At the same time, the location of the label in the factory can be grasped at any time by using the network.
If an employee wants to enter an area and needs to carry a gas detector, LAS will automatically detect the employee. After employees enter the area, they then use the complex event-processing system (complex event-processing) to sense the tags on the gas detectors. If the LAS detects that the position of the gas detector deviates from the employee, the system will sound an alarm bell.
The system was completed in February 2008, and the pilot test was completed in March 2009, and then it was put into use.
Posco Steel said that the system can indeed improve plant safety and save energy consumption. Using Ubisense’s tags and readers, you can also grasp the attendance rate of employees.
As the system achieves the expected results at Posco’s plant, Posco plans to also introduce the system in other plants. The function of controlling the brightness of the light in the factory is hoped to be introduced to all Posco Steel’s factories. Posco Steel plans to install additional functions for product and factory equipment management.
[ad_2]