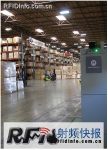
Megatrux uses Motorola’s RFID solution to improve service levels and reduce costs
[ad_1]
Megatrux of the United States is one of the top 100 logistics companies in the world. It mainly provides one-step supply chain services for many retailers. With a warehouse area of 3 million square feet, the company provides first-class third-party logistics freight management services at home and abroad. The service areas include land, sea and air. Megatrux provides retailers with a one-step supply chain service that can help them transport goods from overseas manufacturers to domestic warehouses, and then to store shelves. Megatrux is headquartered in Rancho Cucamonga, California, USA. The company has 9 major freight management service departments and 8 warehouses in China. Its main customers include Wal-Mart, JC penny and Bed Bath and Beyond.
Challenges faced by the company: improve customer service levels, increase revenue, etc.
Megatrux has been trying its best to use various technologies to maintain its highly competitive position in the third-party logistics industry. They know well: In the logistics industry, the customer is God. The current rapid increase in fuel costs has made meager corporate profits worse. For this reason, the company is also actively seeking new ways to improve production processes in order to reduce labor costs while improving customer service. In addition, because many customers are also Wal-Mart suppliers, Megatrux has also realized the importance of RFID technology in the transportation of goods. The company is also actively researching RFID solutions.
Solution: Apply RFID technology to manage warehouses
Megatrux believes that the application of RFID technology in warehouses can meet a variety of business needs. By automating traditional manual operations, the efficiency and accuracy of daily warehouse cleaning can be improved. The real-time data provided by RFID technology enables Megatrux and their customers to track the status of shipments in real time. In addition, Megatrux also provides new RFID services to customers.
Megatrux chose to test Motorola’s RFID solution in the busiest warehouse (the warehouse occupies 175,000 square feet and ships 1 million boxes of goods to Wal-Mart every year). KC Pelle, Executive Vice President of Megatrux, said, “When we choose RFID suppliers, we also consider choosing the best. Obviously, Motorola is the leader in data collection. Moreover, we have been using Motorola and Ship2Save from the very beginning. Technology and industry experience.”
The system adopted by Megatrux includes: installation of Motorola XR440 fixed readers and AN400 high-performance RFID antennas at the import and export of 5 warehouses; installation of 2 RFID Gen2 EPC terminal barcode printers for on-site printing of RFID labels; one Motorola MC9090-G RFID handheld reader that can read RFID tags anytime and anywhere; integrate simple equipment into existing business systems-forming Ship2Save operation management system (S2S-OMS) middleware application.
The result of the application is to realize the pipeline operation of the entire warehouse operation process:
Inbound application of RFID technology
Now, before the goods are put into storage, the staff will print the RFID barcode on the spot, and then paste it on the packing box and pallet of the goods. After that, these boxes and pallets will pass through the warehouse door, and the installed XR440 fixed reader and AN400 high-performance RFID antenna will read the original information on the tag and transmit the data to the S2S-OMS middleware through the network cable connection. . Then, the S2S-OMS middleware will act as an intermediary, interpreting, filtering and even formatting the data, and finally transmits it to Megatrux’s warehouse management system (WMS).
Application of RFID technology out of the warehouse
When the goods are out of the warehouse, the installed readers and antennas will read the RFID information on the pallet tags and send the information to the WMS through the S2S-OMS middleware. After the information is accepted, the documents and advance shipping notice will be issued automatically. If the driver makes a mistake while pushing the pallet onto the truck, an alarm will sound and it will be displayed on the monitor at the warehouse door.
Warehouse mobile application RFID technology
Motorola MC9090-G RFID handheld reader can further utilize the information on the goods label. After increasing mobile performance, Megatrux is now able to extend RFID technology to other inventory management. For example, fast scanning of labeled shelves and packaging boxes has been able to achieve rapid positioning of specific freight or packaging. In addition, mobility can also make the packaging box and the pallet label match, so as to ensure that each pallet contains the designated packaging box.
Application of RFID technology during transportation
Integrating the RFID solution with the company’s GPS system can increase the real-time transparency of truck freight on the way. Now Megatrux can notify customers to prepare for the arrival of goods when the truck is 100 miles away from the destination.
Benefits: better service, fewer errors, less manpower and faster return on investment
The application of RFID solutions has brought great benefits, as follows:
1. Faster processing power improves service quality. Some manual steps have also been removed from warehouse management. For example, the entry and exit of goods in and out of the warehouse no longer requires the personal involvement of staff. Now, RFID readers can automatically acquire and transmit the required real-time data. As a result, the staff will process more orders a day, which increases the number of shipments and customer satisfaction, and at the same time reduces labor costs.
2. 100% accuracy also eliminates errors during transportation: By using RFID, Megatrux can now be sure that specific customers receive specific goods within a specific time, eliminating customer dissatisfaction or high costs caused by transportation errors.
3. Improve customer service to bring stronger competitiveness to the company: Megatrux can provide customers with real-time freight tracking services through the application of RFID solutions. In this way, the company gains a competitive advantage for itself by providing new value-added RFID services to Wal-Mart and other suppliers, and at the same time increases revenues-these benefits serve as dividends that offset the cost of implementing RFID solutions.
4. Quick return: RFID technology has brought so many benefits to the company, and I believe that a full return on investment will be obtained in just 14 to 16 months.
KC Pelle, Executive Vice President of Megatrux, said, “The RFID solution we use is not only a major advantage, but also keeps our company at the forefront of the third-party logistics industry. We can provide customers with personalized real-time and transparent information websites. . Customers can log in to obtain real-time and complete tracking, transportation and logistics process all-round data. This flexible system solution can simplify data processing to meet the different needs of specific customers. The automation of our business processes can make Inventory managers deal with more freight orders, thereby reducing the labor input in disguise. By applying RFID technology, we can confidently guarantee that when our customers ship goods through Megatrux, they will definitely be there. Receive the designated goods at the designated time and at the designated place.”
Next step: rapid promotion of RFID technology
With this successful experience, Megatrux has planned to extend this application system to other warehouses in the United States within 18 months. In addition, the company decided to promote RFID technology to international operations. Currently, Megatrux is installing Motorola RD5000 mobile RFID readers on forklifts, and promoting other material handling equipment to the entire warehouse management process to expand the benefits of RFID technology.
Pelle said, “We tested RFID technology in the busiest warehouses. The Motorola/ShipSave solution has become the basis of a complete warehouse mobile RFID solution. I believe this solution will eventually be extended from warehouse door access management applications to All aspects of inventory management, from receiving and picking to transportation and inventory counting.”
[ad_2]