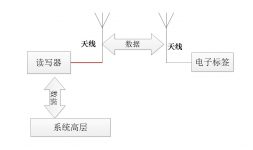
Applied to RFID automotive stamping shop material rack management solution
[ad_1]
Stamping is the leading process in automobile production. As a pioneer in the production of complete vehicles, the stamping workshop is responsible for the storage of raw material coils and sheets; the uncoiling and shearing of coils, etc. The most important of which is the stamping production of various large, medium and small stamping parts. The operation of the entire process of stamping parts from off-line to warehouse-in to warehouse-out is directly related to the production efficiency of the entire stamping workshop.

With the rapid development of the automobile industry, various automobile manufacturers have only pursued the optimal end result from the beginning, and now require that each link in the manufacture of automobiles be optimized. The serious problem is how to control the details of the production process and how to record as much information as possible in the production process.
A large amount of production data needs to be summarized and analyzed. The statistical work of these data requires a lot of manpower and most of the statistical data also has the problem of information lag. The problems found in the production process cannot be solved in time, and manual statistics are required. The project is single, and it is difficult to find the correlation between multiple issues. In addition, because the available logistics area of the factory area is becoming less and less, and the corresponding problems caused by logistics constraints are increasing, the existing logistics methods must be changed and informationization must be introduced to adapt to the logistics requirements under the fast-paced production mode.

Due to the lack of effective information collection methods in the traditional management mode, the material flow information cannot be accurately collected and shared in real time. The obtained data also needs to be manually entered into the system by manual operation. There is a certain delay in the information, and it is often necessary after an error occurs. It takes a lot of time to find out the cause and re-check. A small stamping part may cause the sluggishness of the entire material supply chain system, which greatly reduces the efficiency of vehicle manufacturing.
The temperature and humidity of the production link in the stamping workshop are close to room temperature. The main production equipment is punch presses, including stamping abrasive tools, and the main conveying equipment is pallets and trolleys. The pallet is used to load the plates before punching, and the trolley is used to load the parts after punching. At the beginning of the stamping process, the supplier usually transports the plates to be supplied to the stamping workshop. After passing the quality inspection, the stamping workshop will carry out warehousing operations. The plates after storage can proceed to the next step. The forklift workers will transport the entire pallet to the feed inlet of the press as required. Then, the designated parts are punched out in the press and transferred to the offline position through the conveyor belt. After the off-line position is inspected by the workers, the parts are sorted and placed on the trolley according to the specified quantity. After the qualified parts are full, they will be transported by forklift workers to the warehouse for storage. The unqualified parts trolley will also be transported to the repair area for repair. Finally, the stamping department forklift personnel will pick and place the parts trolley on the welding tractor according to the task list, and then the tractor will enter through the welding shop door, representing the completion of the parts out of the warehouse. The tractor can usually check 1 to 4 parts trolley at a time.
Through UHF RFID technology, the information management of stamping parts in each circulation link is realized, so that each node can grasp the real-time inventory and flow information of the required parts, improve the logistics operation efficiency between warehouses, and make the original cumbersome and complex information statistics. The work becomes simple and transparent, and it is of great significance to help the stamping shop realize the intelligence, information and automation of key material management.
The auto factories of the modern automobile industry have the characteristics of large-scale production, small batches of models, rapid changes in varieties, and co-production of multiple models. These trends have led to a wide variety of stamping parts and different structures. However, the editable attributes of the RFID electronic tag can well associate the information of the RFID tag with the information of the rack. After the off-line station fills the rack with stamping parts, it starts the turntable to rotate to the operable end of the forklift, and the forklift picks up the rack loaded with the stamped parts and exits for warehousing operations. In the process of exiting, the RFID electronic tag will enter the readable area of the offline station collection point. The UHF RFID reader will collect the RFID electronic tag information on the shelf and transmit the information to the back-end system. The binding of this batch of stamping parts and chip information is completed, which completes the establishment of basic data.

Line end installation renderings
When depositing money, scan the QR code on the outer packaging of the incoming material and the corresponding RFID electronic tag on the pallet through the RFID handheld terminal, read the corresponding information of the material (material number, package number, quantity, processing manufacturer, etc.), and use this information Bind with this pallet RFID electronic tag in the inventory management system. After the binding work is completed, the material will be waiting for storage. After the raw materials have undergone quality inspection and are bound to the pallet through the RFID handset, they will be picked up by a forklift and sent to the material warehouse. The installation of Honglu RFID reading and writing equipment at the entrance of the material warehouse will be able to record material warehousing information in real time, thereby helping to effectively manage inventory.
The forklift performs the storage operation of the racks. When passing the warehouse gate, the reading system composed of UHF RFID reader and RFID antenna will read the electronic tag information of all the racks on the forklift and pass the external display system , Including the large screen and LED lights to display the quantity of storage in real time, which can be checked by the forklift operator. At the same time, the storage data will be uploaded to the back-end system through the network, and the back-end system will obtain the bound stamping information according to the electronic label information and complete the corresponding Part storage process, and real-time update of inventory information.

Inbound door installation renderings
The next step of stamping is welding. All stamped parts in stock will flow to the welding workshop. Therefore, an UHF RFID reader is installed on the welding logistics door, and the RFID electronics will be read by the Honlu RFID reader when the parts are out of the warehouse. Label, complete the acquisition of the label information of the material rack entering the welding workshop, the system can complete the out of the corresponding stamping parts, and update the inventory information in real time.

Outbound door installation renderings
Under the premise of flexible production requirements in the stamping workshop, facing different models and different stamping parts, the material racks used for circulation are different. The RFID logistics tracking system of the stamping workshop solves the wide variety of material racks and structures in the stamping workshop. Different problems have achieved the management goals of standardization of shelf label installation, standardization of collection equipment deployment, and standardization of operating procedures. The seamless connection of RFID technology has been achieved without changing the original operating procedures.
The material rack management of the automobile stamping workshop using RFID technology makes full use of the technical advantages of RFID, establishes the marking of the circulating material rack, and identifies the specific stamping parts through the circulating material rack, and utilizes the deployment of the RFID reading system of each circulation node. Realize the real-time control and tracking of the stamping parts supply logistics process, and the entire process is automated without human intervention, which greatly improves the management efficiency and reduces the error rate.
Different from traditional applications, the transformation of RFID technology in the stamping shop first faces the more stringent environmental requirements of the industrial site, including temperature and humidity, electromagnetic interference, vibration, dust, etc., these seemingly inconspicuous external factors. Often it will have an unpredictable impact on the reliability and stability of the product, thereby affecting the use of the entire system.
Shenzhen Honglu Technology Co., Ltd. is a leading RFID hardware and solution integrator in the field of Internet of Things. It has been focusing on technical research in the field of RFID for many years. It has an independent R&D center and product development center, and has obtained a number of invention patents and international certifications. . So far, the company has made achievements in industry 4.0, asset management, warehousing logistics, smart transportation, smart weighing, tobacco logistics, production line management, smart grid, Internet of Vehicles, retail management and other fields, and has accumulated a wealth of product applications and projects Management experience. As the first batch of high-tech enterprises in the RFID field, Honglu has built end-to-end solutions from product development to front-end applications, providing integrators, corporate customers and consumers with competitive RFID solutions, products and services, and Committed to building a better IoT ecosystem.
[ad_2]