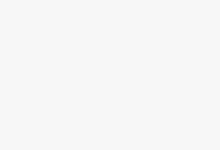
RFID clothing hanging system makes process management more efficient
[ad_1]
The garment production hanging system is a high-tech automation equipment in the garment industry’s “quick response production technology”. The RFID clothing hanging system can improve the working environment of employees and the production environment of the workshop, solve the problem of efficiency differences between different employees, and improve efficiency.
Hang the whole piece of clothing on the hanger, enter the process section in advance, when the production staff completes a process, just tap the control button, the hanging system will automatically transfer the hanger to the next process station, which greatly reduces Non-production time for handling, lashing, folding, etc.
In the hanging system, information identification and collection is a very important link in the system. It can feed back the completed quantity of each production station in the system analysis link. According to the quantified data at each station, the next one is selected based on the best The destination of the process improves the efficiency of the entire hanging system production line. The transmission technology used in the hanging system mainly includes three types of identification methods: RFID, barcode identification, and chip identification. However, due to the chip’s easy to fall off, the bar code is easy to wear and other reasons, the current hanging system favors the use of rfid identification technology to realize information collection and identification.
The combination of RFID and clothing hanging system will greatly improve efficiency. The RFID reader can read the information in multiple RFID tags at the same time, the recognition is very sensitive, and it has an anti-re-reading design, and a tag can only be read once. Compared with one-to-one barcode reading, it is much more efficient. At the same time, it has a high level of protection and can withstand a 1.5-meter drop. In addition, the RFID reader can also realize data communication with PC, PLC, and single-chip microcomputer through RS485/RS232 interface. Through the realization of RFID identification management on the garment hanging production line, timely and accurate data collection has helped the hanging system balance the efficiency differences of different employees and improve production efficiency; at the same time, more efficient employee management has been realized, such as based on feedback The data is used to understand employee output and repair data, find abnormal employee efficiency, and follow up and solve it in time.
Garment production is a labor-intensive industry. From the beginning of raw material fabrics to cutting, proofing, sewing, and ironing, each position requires a lot of workers to work. It is a streamlined operation. Especially in the sewing department, each sewing machine or other equipment has a worker to complete a process, such as the front body, back body, sleeves, etc. How to control and improve the production process, improve production efficiency and product quality, and solve the problem of labor The problems faced by garment manufacturers. Eastman clothing hanging system solves the above-mentioned problems well.
The basic principle of the clothing hanging system The basic concept of the clothing hanging system is to hang the whole piece of clothing on the hanger, and automatically send it to the operator of the next process according to the pre-input process section, which greatly reduces Non-production time for handling, lashing, folding, etc. When the production staff completes a process, they only need to lightly press the control button, and the hanging system will automatically transfer the hanger to the next process station. Eastman clothing hanging system is independently developed from hardware to software. Through the non-contact RFID radio frequency advanced technology scanning system and information system with strong anti-interference ability, it provides timely salary reports, cost difference analysis, quality analysis, and actual per station. Production status, detailed salary information for each employee, conditions and analysis of potential production capacity.
1. Greatly improve the working environment of employees and workshop production environment. Compared with traditional strapping production, the garment hanging system hangs the garment pieces in the air, so that employees are not surrounded by work-in-progress and improves the working environment of employees. In addition, the workshop environment has also been greatly improved, fully complying with the 6s environmental requirements, making the workshop environment simple and clear, and workshop managers can quickly find product line problems through visual management and improve the workshop’s management capabilities.
2. Automatically balance the efficiency difference of different employees in the same process. The hanging system can solve the problem of efficiency differences between different employees in the same process. When the work-in-process is transported to the next process, the hanging system will automatically send it to the one with the least inventory of the work-in-process. One station, so you can ensure the balance of different workstations in the same process. Even if there is a sudden situation that some employees leave for a short time, she can evenly distribute her workload to other employees, and it can also avoid the backlog of work-in-progress due to different efficiencies.
3. The product line management is transparent, and the visual hanging system uses the RFID scanning system and information system to record each piece of clothing and each conveyance of the product line, and then collect, sort, analyze and analyze these records. The data is presented to the user in a graphical screen, so that the user can see the overall status of the current product line very intuitively, and realize the transparency of production management.
4. Shorten the production cycle and improve production efficiency. The hanging system circulates through a fixed-rate product line, and once the work-in-process is processed, it is sent to the next process immediately, and the residence time of the work-in-process is basically negligible.
5. Improve the efficiency of employee management and quality management. Through the collection of data, the suspension system can display the output and repair data of each employee in real time. Product line managers can analyze the data of each employee to discover the abnormality of the employee’s efficiency in time, and then understand the situation and improve the efficiency of employee management. In addition, by tracking the number of repairs, quality problems can be found in time, the reasons can be analyzed, and they can be dealt with in time, so that the hanging system becomes the end point of the quality problems, and the cost caused by the quality problems can be reduced as much as possible.
6. Strong fault tolerance. If one of the stations fails without affecting the other stations, the entire system will still work normally.
7. The hanger automatically returns. Under normal circumstances, the hanger on the track cannot enter the station normally under abnormal circumstances such as a power outage of the garment hanging system. However, the Eastman hanging system can automatically relocate to the route specified by the process after the hanger is restarted.
8. The basic operating equipment on the chain assembly line when low air pressure is interrupted is pneumatic components, and sufficient and stable air pressure is the key condition. The unstable air pressure is usually caused by insufficient pressure of the air compressor or air leakage in the air pipe, which will cause the hanger to enter and exit the station abnormally. In this regard, the rfid garment hanging system can automatically identify whether the air pressure is normal. When the air pressure does not meet the system requirements, the system will automatically alarm and stop operation.
[ad_2]