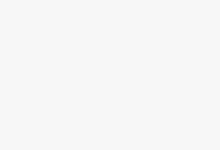
Intelligent application of RFID technology in industrial manufacturing
[ad_1]
“Development is the last word.” With the continuous progress and development of society, weak technological innovation has become a key factor restricting my country’s transformation from a world processing base to a world manufacturing base. The industrialized developed countries have gone through the three historical development stages of mechanization, electrification, and digitalization, and have the conditions to transform to the stage of intelligent manufacturing. The future will inevitably be a highly integrated and intelligent intelligent manufacturing system to replace human mental labor in the manufacturing process. . As an important part of the perception layer of the Internet of Things, RFID realizes intelligent identification and management through sensing objects. The Internet of Things technology allows different devices to be interconnected through RFID electronic tags, allowing people and objects to perceive and recognize, establish a complete supply chain management system, and effectively improve production efficiency.
1. Data collection and condition monitoring are important cores of industrial manufacturing
RFID technology collects equipment status or equipment failures through instruments, equipment, and technical means to identify the process based on the amount of equipment change. The real-time monitoring of CNC machine tools collects various status information of the machine tool through the DNC network and machine tool control by collecting data, and can obtain the operating status of the machine tool equipment through the network. It can also collect the current, power consumption, and vibration of the machine tool to determine the operating status of the equipment and issue a fault alarm.
2. The hardware of the machine tool equipment monitoring system consists of sensors, data acquisition equipment, and network communication equipment
Industrial manufacturing requires diversified technologies to achieve work tasks in complex environments. Through RFID tags, readers, wireless sensor network products, combined with barcode, PLC and other technologies, materials, work in progress, execution equipment, tooling, etc. Real-time collection of heterogeneous source data, and tracking and tracing management of product genealogy, providing basic data for enterprise production and operation control. Through efficient integration with ERP, MES and other systems, the full life cycle management of products is realized.
3. Positioning, tracking and scheduling of public manufacturing resources
In the industrial manufacturing system, some industrial transportation vehicles collect data, such as engineering forklifts, workshop flatbed trucks, etc., as well as some public resources such as on-site technicians. These resources require reasonable dispatch and rapid response, which greatly improves the operating efficiency of the entire manufacturing system. Utilize products and technologies such as ground-sensing RFID tags, UWB, state-judgment sensors, vehicle-mounted terminals, etc., by attaching electronic tags to some engineering vehicles of forklifts, to perform on-site maintenance/technical personnel and other resources spatial location positioning, operation trajectory tracking, and busy State judgment, task dispatch and call, optimize the allocation of public resources, and improve the rapid response capability of the manufacturing system. It’s like an automated forklift at a large terminal.
Fourth, RFID technology can implement process monitoring and visual management of the production plan execution process
Enhance the timeliness of production planning and scheduling, greatly reducing human errors in work. A visual production process monitoring platform can be realized through products such as station readers, electronic trays, RFID tag pendants, etc., to track the whole process from rough to finished product, and record the automatic report of the product, the completed quantity of each product/batch, and the status of the workpiece. The current process, the execution equipment and operators of each process, the actual working hours of each process, etc., provide original certification data for planning and scheduling, on-line materials, on-site logistics, and quality traceability, and also provide a basis for enterprises to carry out value engineering.Form a product traceability tracking system, greatly improve the credibility of the company’s products, and establish a complete quality system
RFID technology can realize warehouse automation management, electronic warehouse and on-site logistics management. By installing RFID tag design and packaging technology within the effective range, it can effectively read and write RFID electronic tags for individual materials, box materials, and transfer pallets. Data collection. Through electronic warehousing, it realizes the automation of warehouse management, automatic identification and processing of materials entering and exiting shelves, fast picking and inventory, and fast electronic inventory support for entire warehouse/classification/division; inventory warning and support for inventory management and replenishment. According to the production plan, the distribution plan of each warehouse is automatically generated, and the forklift, AGV trolley, etc. are uniformly dispatched. Monitor the material inventory of each station, track the material consumption at the production site, and generate material requirements and delivery requests. Inventory and line-side material inventory analysis to reduce line-side material accumulation and reduce the amount of sluggish materials.
[ad_2]