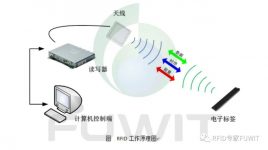
RFID technology solutions applied to automobile assembly lines
[ad_1]
Background of the project
With the continuous development of the automobile manufacturing industry, some traditional manufacturing methods and technologies can no longer meet the requirements of the modern automobile manufacturing industry. The traditional automobile assembly line usually only assembles cars of the same model in one assembly line, and each model of car has a single configuration. Therefore, the assembly line assemblers have simple work, high assembly efficiency, and assembly errors are not easy to occur. Nowadays, with the development of the automobile industry, cars are becoming more and more diversified and individualized. This requires a car assembly line to be able to assemble different models of cars, and the configuration of the same model of cars is also diversified. At this time, if the assembly line The informatization of the in-line assembly process is low, and the assembly data collection and assembly verification work cannot be done well. It is prone to problems such as low assembly efficiency, high error rate, and failure to grasp the assembly situation in time.
The collection of assembly data of the traditional automobile assembly line mainly relies on manual collection mode and bar code collection mode. The informatization of the assembly process mainly relies on the process kanban, and the assembly verification mainly relies on the human judgment of the workers. These several assembly methods have the problems of untimely assembly data collection, low collection efficiency, large collection data errors, and difficulty in the application of collection technology; the process Kanban information cannot be updated in time, the update information procedure is complicated, and a lot of manpower and material resources are wasted, and resources are wasted. Information update error rate is high; assembly verification takes a lot of time, and verification errors are prone to problems.
In order to solve these problems in the automobile assembly line, more advanced technology is applied to realize the informatization of the automobile assembly process, the timely and accurate collection of assembly information, and the realization of assembly verification functions to help automobile manufacturers achieve rapid, accurate, and personalized It is of great significance to make the assembly in a modern and transparent way.
02Analysis of automobile assembly process
As a typical situation in the discrete industrial production process, automobile assembly production activities have the following characteristics: the production process is parallel and asynchronous, the equipment function is redundant, the control quantity is independent of each other, the production resource management is complicated, and the parts in the production process are in Discrete state, the production of vehicles is mainly realized through physical processing and assembly.
Automobile manufacturing roughly goes through four major technological processes: stamping, welding, painting and final assembly. The car assembly process refers to the process of assembling auto parts other than the car body to the car body according to the specified requirements in accordance with a certain process and technology, and making it a qualified car after debugging and inspection. After the three sequential processes of stamping, welding, and painting, the car body with colored paint is formed and stored in the PBS (sprayed body storage area) between the assembly plant and the painting plant, waiting for the scheduling of the assembly production.
When the assembly plant starts production, the spreader lifts the car body to be assembled from the PBS into the assembly line to start work. Modular assembly methods are used in the final assembly production line. There are many stations along the production line, and each station is responsible for a specific process. When the car body moves forward with the assembly line, the corresponding parts are installed on the car body in sequence at each station. The main processes involved in the automobile final assembly include: front and rear axle installation, brake controller safety, powertrain installation, instrumentation and electrical wiring installation, and the filling of various solutions.
In the traditional process, the automobile assembly production line mainly uses barcode technology. The employees at the station manually scan the body VIN code and component barcode for vehicle tracking and assembly information collection. The entire collection process is relatively time-consuming. When the bar code is damaged or stained and cannot be identified, employees need to manually enter the vehicle’s VIN code or part code. This has a high error rate, time-consuming, and difficulty in speeding up the production cycle. The degree of visualization of the production site needs to be improved. It is necessary to provide workers with real-time and accurate assembly guidance to prevent the occurrence of missing and incorrect installations. The assembly of vehicles on the production line also needs to be monitored in real time.
03RFID technology application
3.1 Technical principle
RFID (Radio Frequency Identification) uses the principle of radar backscatter to transfer signals between the tag and the reader. As a non-contact automatic identification technology, it has a large amount of data storage, readable and writable, non-contact, and long recognition distance. , Fast recognition speed, good confidentiality, strong penetration, long life, good environmental adaptability, and the ability to recognize multiple tags at the same time, and can work in various harsh environments.
A complete RFID system consists of three parts: a reader (antenna), an electronic tag and an application software system. Its working principle is that the reader emits a specific frequency of radio wave energy to drive the electronic tag Send the internal data, at this time the reader will sequentially receive and interpret the data, and send it to the application for corresponding processing.
3.2 Applicability analysis
RFID technology is not just a simple replacement of bar code technology, its application in discrete manufacturing will change the production and operation of discrete manufacturing enterprises. RFID technology has the advantages of large data storage capacity, readable and writable, non-contact, long recognition distance, fast recognition speed, good confidentiality, strong penetration, long life, good environmental adaptability, and the ability to recognize multiple tags at the same time. Instead of barcodes to identify and track vehicles on the automobile production line, there is no manual intervention in the whole process, which can greatly reduce the labor intensity and error rate of workers. Nowadays, RFID technology can be used to realize automatic, high-speed, and effective recording, reduce the labor intensity of operators, and increase the pass rate of products offline.
Applying RFID technology to the automobile manufacturing industry and integrating it into the MES system is conducive to the effective transformation of management decisions and real-time transmission to the product layer, which can improve the management and control level of the production process, and effectively track, manage and control the production process and the upper level The combination of management systems can reasonably schedule and manage these resources, improve manufacturing competitiveness, improve production organization, shorten production cycles, reduce the number of products in progress, improve product quality and reduce human resource consumption. It has important significance and application value for the development of discrete manufacturing manufacturing system models and application solutions, and for improving the visual monitoring of the manufacturing process and product quality tracking.
04Solution
4.1 System Architecture
The system uses the RFID software middleware deployed in the workshop application server to uniformly manage the workshop reader network, and collects, processes and stores data in the data server in real time, which is beneficial to shield the differences of RFID equipment and improve the RFID reader network The stability and efficiency of the RFID device does not depend on the station terminal, and no special configuration of the station terminal is required, which is convenient for deployment. The architecture of the automobile assembly manufacturing execution system based on RFID technology is shown in the figure below.
The system makes full use of the technical advantages of RFID, combined with the MES system of the final assembly shop, to solve the problem of the fault between the planning layer of the enterprise’s current ERP system and the process control layer of the workshop on-site automation system, the internal logistics level of the workshop and the production control layer of the MES system. Visual and digital management of manufacturing and quality.
4.2 Application process
The final assembly line is an assembly line system. All vehicles that need to be assembled need to be transported to the designated station through the spreader or platform of the final assembly frame to assemble parts and components, and after the assembly is completed, pass the spreader or platform to the designated station. It is transported to the next link, until all the processes are completed.
Therefore, the UHF RFID electronic tag of this scheme is bound to the spreader and the platform. When the vehicle is placed on the spreader or the platform, the VIN number of the vehicle is connected to the spreader or the platform through the background management system. The electronic tag ID information is bound.
Install UHF RFID readers at each assembly station. At the assembly station, after the UHF reader reads the vehicle tag, it obtains the corresponding vehicle VIN code through the background and prompts the component installation information of the corresponding station. The staff install the corresponding parts. The system obtains the component installation information of the corresponding vehicle for later quality tracking, and the system returns the material consumption information to the LES system, and refreshes the station component installation information prompt until all the components that should be installed at the station are installed. In the supply link to the production line station, after the production logistics department delivers the parts to the station, the system updates the number of parts information.
4.3 Application deployment
In the final assembly production line, all the points that use the hanger to transport the body and need to identify the body information, such as counting points, electric tightening, SRS terminals, etc., use the following installation methods to deploy RFID equipment.
In the final assembly line, all the carriages that use the skid for car body transportation, such as the left cabin wiring harness, the right cabin wiring harness, and engraving equipment, etc., install RFID electronic tags on the skis, and install RFID readers on the rolling bed at key positions. Car body information is identified and tracked, and uploaded to different systems on the final assembly line.
4.4 System function
The final assembly line application based on RFID technology has the following functions:
When the system is spreading on the car body, it can automatically obtain the body number, and bind the body number to the RFID information to make it correspond to the production information, and when the car body is converted between the spreader and the table, it can automatically complete The transfer of information ensures that the information flow of the car body on the entire assembly line is correct and continuous;
When the car body reaches the assembly station, it can automatically obtain the body specification information, and display the corresponding operating procedures on the station terminal, and can provide real-time and accurate assembly instructions to the assembly workers;
After the system completes the assembly at the workstation, it can automatically record and save the assembly information, including the information of the assembly personnel, assembly parts, etc., for subsequent quality tracking;
Combine the on-site visualization system of RFID technology to monitor the vehicles in production and understand the production line situation and vehicle assembly progress in real time;
The system has the function of error prevention, and the body specification information has corresponding part coding rules. When the assembly is performed at the workstation, if the part code does not meet, the system will give an alarm in real time;
The system also has the error-proofing function of the process. When the flow is transferred to the current station, the system will automatically check the previous process. When the previous process is not completed or made an error, it will also remind at the station to realize the process. Quick error correction. 05 concluding remarks
The automobile assembly system application based on UHF RFID technology is based on the analysis of the automobile assembly production process, and integrates RFID technology into the automobile manufacturing execution system, so that enterprises can timely and accurately grasp the status of the production line and improve production Efficiency is conducive to the collaborative work between the MES system and the LES system, and provides accurate data guarantee for product quality tracking.
[ad_2]