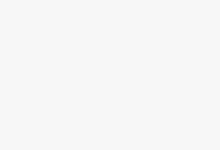
Application of RFID in automobile production line
[ad_1]
As a typical situation in discrete industrial production, automobile assembly production activities have the following characteristics: the production process is parallel and asynchronous, the equipment function is redundant, the control amount is independent of each other, the production resource management is complicated, and the parts in the production process are discrete. State, the production of vehicles is mainly realized through physical processing and assembly.
RFID technology is not just a simple replacement of bar code technology, its application in discrete manufacturing will change the production and operation of discrete manufacturing enterprises. Because RFID technology has many advantages such as large data storage capacity, readable and writable, non-contact, long recognition distance, fast recognition speed, good confidentiality, strong penetration, long life, good environmental adaptability, and the ability to recognize multiple tags at the same time, Use it to replace barcodes to identify and track vehicles on the automobile production line. There is no manual intervention in the whole process, which can greatly reduce the labor intensity and error rate of workers. Nowadays, RFID technology can be used to realize automatic, high-speed, and effective recording, reduce the labor intensity of operators, and increase the pass rate of products offline.
Establish a unified central database on the site of the enterprise workshop as an information platform for the circulation of goods to facilitate overall standardized management. In the industrial link, RFID technology is used to assign an identification number (ID) to each work-in-progress component, which is the name of the component in the information network. Through RFID technology, the production status and inventory status are mapped to the information network and registered in the information network. In the field center database, it is transmitted to the information system (such as ERP, MRP), etc.
Applying RFID technology to production line monitoring can realize automatic control and detection and save costs. RFID tags can uniquely identify each product, and record the raw material and source, production line location, production process and inventory status of each product through the application, and provide an effective basis for companies to better manage production and adjust inventory.
The automobile manufacturing industry was originally a typical multi-work, multi-process, and multi-material mass production process. Now with the development of personalized cars (buyers can customize the car), almost every car will have some personalized Therefore, it is necessary to apply RFID technology to achieve transparency in the entire production process. The automobile industry chain can be simply divided into three basic links: parts manufacturing, vehicle assembly and after-sales service. At present, RFID technology is mainly used in parts manufacturing and vehicle assembly links. Whether it is a parts production plant or a complete vehicle assembly plant, only manual management of a large number of parts and complex and numerous manufacturing processes is not only error-prone, but also unable to quickly improve the operating efficiency of each process from the source.
Application of RFID in automobile welding production line
In the early car body welding production lines, most of the manual methods were used. The operation was carried out step by step according to the written operation manual, which was prone to human error. Later, bar code labels were gradually used for management. Although the human error rate was reduced, identification errors often occurred due to the influence of dust, high temperature vibration, and oil pollution on the production site. When it comes to the case with a cover, no matter whether it is a barcode label or manually, it can not be used with confidence. The schematic diagram of the application of RFID in the automotive welding production line is shown in the figure.
In the picture, select high-temperature, dust-proof, metal-proof, magnetic-proof, reusable active packaging labels, and monitor the welding production line operations through automatic identification. The operation instruction information (vehicle type information, welding instruction information, program, etc.) can be stored in the target tray. The antenna can be set in a higher place of the welding production line in order to avoid the influence of people and machines. Due to the strong anti-pollution ability of RFID tags And strong durability, which greatly reduces identification errors and can effectively improve the visibility of the internal supply chain.
Application of RFID in automobile coating production line
The automobile painting production line has many complicated processes, large model changes, and great production flexibility. The purpose of automobile painting is to make every car sold to make consumers look more perfect. Therefore, each process link of the workshop production line must have a very high level of automation and quality monitoring system. Therefore, the use of RFID technology in the body identification system of the production line automatic control system can collect all kinds of on-site data statistics, status monitoring and quality inspection information in the production process in real time, and send it to the production control center in time.
In the automobile coating production line, the conveying equipment is a skid conveyor. As shown in Figure 3, each skid carrying the car body is equipped with an RFID passive tag with a temperature of 240℃. In the entire production process, this label runs with the workpiece, forming a piece of data that moves with the body, becoming a “smart car body” that carries data with you. According to the different needs of production technology and management, on-site reading and writing stations can be set up at the entrance and exit of the paint shop, the branch of workpiece logistics, and the entrance of important technological processes (such as painting room, drying room, storage area, etc.). Each on-site reading and writing station can complete the writing of skid, body information, spray color and frequency, and send the information to the control center at the same time.
RFID technology combined with optical fiber Ethernet and field bus can form a complex automatic control system, realize the flexible production of automobile coating production line, improve the automation level of automobile body production and the flexibility to adapt to different types of production, so that the system is very reliable Performance and fault tolerance.
Application of RFID in automobile assembly line
As the final link in the production of a complete vehicle, the assembly shop involves many parts and processes, which plays an important role in ensuring the quality of the vehicle and the production schedule. Any interruption of the assembly process means a delay in the operation. On the final assembly line, especially on the assembly line that adopts the JIT (Just In Time) production method, raw materials and parts must be delivered to the workstation on time, and the inventory and material supply must also match the vehicle assembly schedule. Before the adoption of RFID technology, automobile manufacturers used barcodes or paper identification cards to track and monitor the progress of vehicle assembly in real time. The disadvantage is that barcodes and identification cards are extremely easy to be destroyed, exchanged or lost. Causes wrong operations in production operations.
Take Ford Motor Company as an example. Its Mexican plant began to use RFID technology to solve the above problems a few years ago. The factory installs recyclable and reusable RFID tags on the hangers of assembled vehicles, and then compiles the corresponding serial number for each assembled vehicle, and writes this serial number into the RFID tag with a reader, with detailed requirements for the car The labels run with the assembly conveyor belt. Install the reader at the appropriate position at each work point to ensure that the car completes the assembly task without error at each assembly line position. When the rack carrying the assembled vehicle passes the reader, the reader can automatically obtain the information in the tag and send it to the central control system. The system can collect the production data and quality monitoring data on the production line in real time, and then send it to Material management, production scheduling, quality assurance and other related departments. In this way, functions such as raw material supply, production scheduling, quality monitoring, and vehicle quality tracking can be realized at the same time, and various malpractices of manual operation can be effectively avoided.
The application of RFID technology in the automobile production line has advantages that other technologies can’t match. It can automatically obtain data without contact and can withstand harsh working environments. This ensures that its advantages are flexible configuration, fast response speed, and low system communication requirements. , So that the production plant can accurately collect relevant data and conduct online analysis and processing, realize the automatic real-time tracking and effective monitoring of the automobile production line, and improve the production efficiency. It is believed that with the continuous development of RFID technology and the popularization of application systems, the performance of RFID technology will surely be greatly improved, the cost will be gradually reduced, and the potential safety hazards will also be alleviated. RFID technology is bound to become the mainstream of automobile informatization manufacturing and automobile informatization management, thereby promoting the development of the automobile industry.
[ad_2]