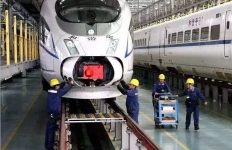
RFID technology is applied to tool management to improve work efficiency and safety assurance
[ad_1]
Routine maintenance is a delicate operation. The quality, accuracy, and integrity of maintenance tools affect the quality of maintenance and even affect safety. The scientific management of tools can ensure that the tools are effective and available, and that the tools are intact and will not be missing. Therefore, research on the scientific management of tools must be carried out. The various tools used in the maintenance process, like the materials and equipment, are the right arms of the maintenance personnel.

In daily maintenance work, hundreds of tools are often used. They have a wide variety, complex specifications, and a large number. Therefore, the scientific management of tools is of great significance to the safety of production, improvement of labor efficiency, improvement of maintenance quality, reduction of labor intensity, and acceleration of liquidity turnover.

At present, the main task of tool management of maintenance units is to supply suitable tools to maintenance teams; to do a good job of classification and numbering of tools; to establish and improve the inventory system of tools; to repair and replace tools that need to be repaired and replaced in a timely manner. However, due to the lack of adequate information technology, it is still in the initial stage of manual management, and there are many tools that have been lost by maintenance organizations.
RFID solution
The warehouse management of tools can be completed by installing RFID electronic tags on the tools. Using RFID technology can save you management time and improve work efficiency. The basic information of the tool can be displayed on the staff’s computer equipment to facilitate statistics and inquiries.

RFID system composition
The RFID system is mainly composed of: RFID electronic tags, RFID tag issuers, RFID fixed readers, RFDI antennas, RFID handsets, and tool management systems.

Label fixation: According to the classification of all the tools on site, the most suitable matching label is selected according to the tools of each category. It is recommended that each type of tool uniformly select the same fixed position.
Data entry: The chip in the RFID tag can store data, associate the attributes of each item of laundry to be managed with the RFID tag ID in the database for a one-to-one correspondence, and record and track the maintenance cycle of each item.
Employee ID card: each employee is equipped with a corresponding ID white card label to write card binding.
RFID system function
1. Personnel information management function: including personnel information, work card information, and personnel information export and import into this system. This function can be connected with other related management software.
2. Tool information management function: including new tools, old tools scrap function. This function can make the tool library information timely and accurate.
3. Automatic encoding function: encode new and old tools and bind data with RFID tags.
4. Tool borrowing and returning management function: This function is mainly used to perform the operation registration of tool borrowing and returning by swiping card or scanning operation, and has the function of returning overtime alarm.
5. Tool inventory counting function: input the actual counted quantity into the system for comparative analysis and processing with the original data. The results of the inventory are confirmed, and if there is an inventory gain, an inventory loss, or a reported loss, it will be processed separately according to different situations.
6. Report output and printing function: This function can summarize and query the detailed information of the tool borrowing and returning time in a certain period of time, as well as our query function for tool borrowing and returning information according to any conditions, even if the borrowing of certain tools is accurately known. Still the situation.
System operation process
1. Tool purchase and storage: First, before the tool is stored, paste or hang the electronic label on the tool, and enter the tool’s product name, model, specification, origin, brand name, packaging and other basic information, and divide the tool category and enter it And after the classification is completed, place the tools in the corresponding position of the warehouse, and make a record of the location.
2. Tool lending: Use the RFID reader to read the RFID information of the tools that need to be lent, and save the lending time, borrowing department and personnel, borrowing purpose and other related information in the data collector, click the touch screen to confirm, Upload to the system via batch processing or wirelessly.
3. Tool return: Use the RFID reader to read the information in the tool tag and check it with the information retained when lent. After confirming that it is correct, click the touch screen to confirm the storage, and place the tool in the corresponding position in the warehouse, and the return procedure is complete.
4. Appraisal of measurement tools: According to relevant national regulations, the measurement tools shall be regularly appraised to the designated professional testing department. After verification, the verification information is written into the system.
5. Tool scrap: When the tool reaches the designated service life or is damaged and cannot be used anymore, it must be scrapped. After reading the electronic label information of the device through an RFID reader or a handheld terminal, the device is scrapped after the reason for scrapping, the handler, the approver and other relevant information are entered in the system. The scrapped equipment information will be kept in the scrapped tool file information for inquiries.
6. Tool inventory: enter the inventory status, use the RFID handset to sequentially collect the tool tags on the tool rack, enter and upload to the background, through the RFID tags installed on the tools, the quantity of each tool can be collected, the background The system then completes the inventory of warehouse tools and generates reports based on the collected quantity data.
RFID system benefits
1. RFID automatic identification technology management replaces the previous manual bookkeeping management to improve the management level;
2. The accuracy performance is greatly improved, and the RFID technology reduces manual inventory errors;
3. Work efficiency has been further improved;
4. The software and hardware operations are simple and easy to understand, and the hardware functions and software processes are clear and clear;
5. Adopt advanced RFID technology to take a leading position in the industry and enhance the competitiveness of the industry.
[ad_2]