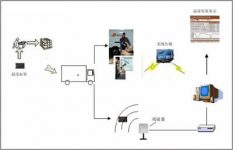
Application of RFID system and label in production line
[ad_1]
Easier said than done, radio frequency identification (RFID) systems and tags are still quite expensive. Considering that almost all products have to be labeled and the labels are difficult to reuse, the high cost can be imagined. Therefore, when Wal-Mart notified its 100 largest suppliers in June 2003 that all of its 100 largest suppliers must adopt RFID tags, and that the relevant equipment must be in place at the shipping center by January 2005, many suppliers were busy trying to improve their return on investment. (ROI) and reduce costs.
One of the hundred largest suppliers is Wells’ Dairy, which provides Wal-Mart with Blue Bunny ice cream and various small commodities. Wells’ report pointed out that it is the largest family-owned dairy company in the United States and operates the world’s largest ice cream production plant. The plant is located in LeMars, Iowa, and works up to 160 hours a week.
In order to comply with the new RFID regulations, many suppliers put labels on them before shipment, but Wells’ approach is different. It uses RFID systems early in the manufacturing process, saving costs and realizing other advantages. Brad Galles, Wells’ process control manager, started a pilot project with the dairy company’s automation supplier Rockwell AutomaTIon in mid-2004. Its internally developed solution uses Allen-Bradley 1756 EWEB module for ControlLogix to process data. The relevant data comes from Alien Technology’s RFID reader and 915-Mhz, 96-bit Squiggly tags.
The antenna reader writes on the RFID tag, which is affixed to the outer packaging of the two-barreled product, and 30 outer packaging boxes can be affixed per minute. During quick freezing, read the label on the outer packaging box again, at this time the speed can reach four times the previous, and finally the product is shipped. The RFID system transfers information back to Wells’ control system, realizing information sharing in the company’s corporate network. Galles explained that if the usual system of labeling and then shipping was adopted, Wells’ would have to introduce manual repackaging, which would increase labor costs.
Galles pointed out: “We believe that the use of RFID technology can promote process transformation and improve performance from the beginning. Once the data is collected, we can use it to improve catalog tracking, automate most quality control and catalog work, and simplify data collection. Work.” Wells’ report also shows that its RFID system frees employees from heavy work, reduces shipping errors, and reduces manual repair work as much as possible.
The dairy company and Rockwell achieved efficiency improvements through the RFID system, making full use of the data processing capabilities of the tags. For example, each RFID tag of a dairy product company is connected to a database, which carries the production parameters of the ice cream in the box, including production time, batch identification information, and product line. This enables Wells’ company operators to know exactly when each label was attached, and which batch the batch is shipped to.
All in all, the advanced features of RFID tag identification data help to strengthen the physical status and environmental data of the user database, ensure that process changes or tests are carried out effectively, and support related decision-making and implementation in order to further improve product quality.
Galles pointed out: “The role of RFID is that it can enhance the visibility of factory production, because we can use RFID to collect information, and the information collection method is compatible with existing equipment, which creates more value for us. To achieve the highest return on investment, we should continue to use the ControlLogix platform used in the existing process to design the RFID system.”
RFID basic knowledge
RFID tags do not need to monitor the production line and can process more data. Although barcodes are ubiquitous and relatively inexpensive, RFID tags are more robust and should replace barcodes. In addition, RFID is cheaper than traditional radio transmitters and other wireless technologies.
However, in terms of current applications, RFID is mainly used for identification, material handling and other types of document work. This can meet the requirements of Wal-Mart and the US Department of Defense (DoD) on the installation of RFID systems. People have given great expectations to the development of this technology, but there are also reports that it is still facing obstacles in its realization, and there are also doubts about the return on investment, so the implementation of RFID should not be rushed.
In view of this, generally speaking, how the application development trend depends on the user in the final analysis. The user should be clear about their own needs, understand the function and cost of RFID, and then decide whether RFID can help improve work efficiency, promote decision-making, and enhance quality. Control and promote production. If it is not suitable, users will still choose technologies such as barcodes, radio transmitters or wired networks.
Bill Arnold of Omron Electronics LLC pointed out: “If the data acquisition system sees the bar code with its’eyes’, it can also hear the RFID tag information through the system’s’ears’, and it can also pass the system’s’language’ Talk to it. In this case, RFID technology is obviously a better way to achieve control and visibility in the supply chain. Barcodes are only 14 to 16 digits, and each RFID tag has 96 to 256 digits, as a This unique technology can be used to clarify various parameters of the product, including production shifts, machine tools used, and operators.”
RFID tags can be read-only, write once read many (WORM), read-write, passively read with an antenna/reader, or actively send signals (usually assisted by batteries).
[ad_2]