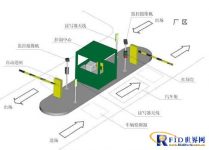
RFID-based intelligent weighing management scheme for coal mine vehicles
[ad_1]
http://www.iot-lzhy.com/qd/nt/20/index.html
1. System Overview
1.1. System background
The characteristics of vehicle management in the mining area are that there are many vehicles and models, and the management is more difficult; how to broaden the management perspective, improve vehicle operation efficiency, enhance driving safety, and strengthen vehicle performance management is a problem that needs to be solved urgently. Although the vehicle management data and database in the mining area are relatively complete, these data need to be manually entered into the computer database or parking check-related certificates to be checked. It is difficult to implement at gates with high traffic volume and high speed requirements, and it is time-consuming and labor-intensive. How to quickly and effectively collect data, remotely inspect and judge the system in the vehicle import and export, weighing area, and unloading area of the mining area has become the primary problem. Mining plants, power plants, mines, garbage dumps and other units have a large number of material transportation vehicles entering and exiting every day, requiring procedures such as parking, registration, and weighing. The data is manually entered into the computer by the operator, which is not only time-consuming, but also error rate In addition, it is easy to breed man-made fraud and cause a lot of economic losses to the enterprise.
1.2. Status Quo and Analysis
According to the current status of manual management of vehicles in mines, our company proposes to combineRFIDTechnology, electronic vehicle weighing technology, communication technology, automatic control technology, database technology and computer network technology solutions. The system can automatically record the license plate number, weight information, time information, etc. of vehicles equipped with electronic tags, and write them into the host The database can effectively eliminate human error, prevent over-balance blockage, cheating, etc., ensure the accuracy of original data collection, and reduce economic losses.
Two key points are set up on the ore transportation route, which are the loading point and the unloading point.Triggered when the vehicle enters the weighing pointReaderRead the card, and transfer the detailed information of the vehicle to the PC, match it with the tag information, and check whether the vehicle has lost ore during transportation.
2. System Introduction
2.1. System Principle
Intelligent management of all vehicles entering the mine requires each vehicle entering the mine to be assigned a special RFID tag, which contains the name of the owner of the mine truck, tare weight/license plate number/material type/ Information such as net weight/loading place/destination/printing time, year, month, and day. Set four key points in the transportation route. First, when the empty ore truck enters the mining area, the reader is triggered to read the card when the truck is weighed. The reader transmits the information in the on-board tag to the host, and at the same time instructs the electronic scale to transmit the vehicle weight information; after the ore truck is loaded with ore When leaving the mining area and weighing by the truck scale, the reader will trigger the reader to read the card. The reader will transmit the information in the on-board tag to the host, and at the same time instruct the electronic scale to transmit the vehicle weight information. This time the vehicle weight information is carried out with the empty vehicle weight information. For comparison, calculate the weight of the ore loaded on the vehicle; when the mining vehicle reaches the end of the transportation and is weighed by the truck scale, the reader is triggered to read the card, and the reader transmits the information in the on-board tag to the host, and at the same time instructs the electronic scale to transmit the weight of the vehicle Information: After unloading the ore, when the empty truck is weighed by the truck scale, the reader will trigger the reader to read the card. The reader will transmit the information in the on-board tag to the host, and at the same time instruct the electronic scale to transmit the vehicle weight information, which is compared with the terminal weight information. Calculate the weight of the ore. This weight is compared with the weight of the ore shipped in the mining area, and it is finally judged whether there is any loss during transportation.
2.2. System structure
This system consists of readers, electronic tags, truck scales, weighing instruments, infrared reflectors, LED light displays, signal lights, video surveillance, servers, etc.
The system network topology diagram includes monitoring management system, intelligent vehicle management, weighing host, sampling host, skinning host, real-time monitoring, database server and other online workstations, etc. The unit systems are connected together through the intra-plant LAN to realize data sharing.
2.3. System Flow
Before entering the loading area, all transport vehicles use RFID to identify and record vehicle information, and weigh them. After the weighing is completed, the server automatically records the weighing information, and the display screen displays the weighing information; the transport vehicles enter the loading area for ore loading and loading. After the mine is completed, drive out of the loading area and weigh again, the weight information is automatically entered into the system, and LEDs give weight reminders; the transport vehicle arrives at the destination and enters the unloading area to record the vehicle information through RFID identification, and weigh it. After the weighing is completed, The server automatically records the weighing information, and the display screen displays the weighing information; the transport truck is unloaded, and the scale is weighed after the unloading is completed, and the weight information is finally recorded. Through information comparison, it is judged whether there are omissions or residues in the mine.
3. System workflow
3.1. Admission registration
The mine registration office first registers the vehicles entering the mine and allots them a special mining label, and then saves the label’s card number, vehicle license plate number, vehicle owner’s name, entry time and entry location related information in The host database.
3.2. Invoicing
Only customers who have been issued a special tag for ore transportation can go to the ticketing office of the mine to issue an invoice to purchase ore.
3.3. Empty vehicle weighing
After the customer issues the ticket, the mine truck can be driven into the truck scale channel for weighing. The vehicle detector installed at the crossing senses the entry of the car, and transmits the signal to the front barrier and signal light. The barrier is immediately closed and the signal light turns red. Prompt the driver to drive slowly, and at the same time ask the weighing instrument and reader to start working. After the tag on the mining truck is read by the reader, the reader transmits the information of the vehicle to the host, and instructs the electronic scale to start transmitting the weight information of the vehicle. At the same time, the camera monitors whether the vehicle is parked at the designated position and captures the image. When the host receives the card number and weight information, it accurately records and backs up the information, and then issues an instruction to open the barrier, and the mine truck drives into the mine for loading.
3.4. Loading ore
After the empty ore truck has been weighed, it can be driven into the mine to load the ore.
3.5. Loading and weighing
After loading the ore, the truck needs to enter the truck scale again for weighing. The vehicle detector installed at the crossing senses the entry of the car, and transmits the signal to the barrier and signal light in front. The barrier is immediately closed and the signal light turns red to indicate The driver drove slowly, and at the same time asked the weighing instrument and reader to start working. After the tag on the mine truck is read by the reader, the reader antenna transmits the information of the car to the host, and instructs the electronic scale to start transmitting the weight information of the car. At the same time, the camera monitors whether the car is parked at the designated position and captures the image. After the host receives the card number and weight information, it accurately records and backs up the information, and then issues an instruction to open the barriers, and the mine truck drives into the ticketing office of the mine to issue a ticket.
3.6. Invoicing
After the ore truck is loaded, it needs to go to the ticketing office again to issue an invoice. The ticketing office checks whether the information on the two weighings of the ore truck is consistent. The information includes whether the card number of the mining truck is consistent, whether the owner of the vehicle is consistent, whether the brand number is consistent, etc. When all the information is consistent, the billing office will automatically calculate the net weight of the ore shipped according to the management system and issue the bill.
3.7. Appearance
Finally, the mine truck can drive out of the mine with a bill and pass the inspection by the guard.
3.8. Unloading and weighing at destination
The mine truck arrives at the destination. Before unloading the ore, drive into the truck at the destination for weighing. The vehicle detector installed at the crossing senses that there is a car entering, and transmits the signal to the front barrier and signal light. The barrier is immediately closed and the signal light turns red to prompt driving The operator is driving slowly, and at the same time, the weighing instrument and the reader are required to start working. After the tag on the mining truck is read by the reader, the reader transmits the information of the vehicle to the host, and instructs the electronic scale to start transmitting the weight information of the vehicle. At the same time, the camera monitors whether the vehicle is parked at the designated position and captures the image. When the host receives the card number and weight information, it accurately records and backs up the information, and then issues an instruction to open the barrier.
3.9. Unloading
After the ore truck is weighed, it can be driven into the mine to unload the ore.
3.10. Empty vehicle weighing
After the mine truck is unloaded, the empty truck is weighed, and the invoice is issued at the ticketing office. The ticketing office checks whether the information on the two weighings of the mine truck is consistent. This information includes whether the card number of the mining truck is consistent, whether the owner is consistent, and whether the brand number is consistent. And so on, if all the information is consistent, the billing office will automatically calculate the net weight of the ore shipped according to the management system to issue the bill, and collect the ore transport special label.
3.11. Calculate the weighing
The calculation of the whole loading process is divided into 3 calculations, the loading weight is calculated by the relative ratio of the loading weighing and the empty car weighing; the unloading yard weighing is compared with the loading weighing to check whether there is ore leakage during the transportation process; the empty car weighing Calculate the ore weight compared with the unloading yard weighing, and compare with the ore weight calculated for the first time to calculate whether the ore is lost or leftover.
4. System Features
Compared with the previous mine vehicle management and intelligent weighing systems, the use of RFID technology for mine vehicle management has the following advantages:
Information collection automation
The weighing data output by the truck scale and the electronic tag card number installed on the mining truck are processed by related equipment and transmitted to the computer. The computer displays the weight of the cargo carried by this car and stores it in the computer’s database. Users can perform operations such as querying, summarizing, and printing according to their needs, thereby realizing information collection automation.
Strengthen management to prevent favoritism and fraud
One car, one card, and the electronic label is affixed to the windshield of the car, and the weight weighed on each platform scale strictly corresponds to one card and one car. Cooperate with the camera’s image capture function to ensure that the entire system data is foolproof and accurate.
Protect the safety of this area and prevent illegal vehicles from entering
The system can be integrated with the parking lot management system. Only vehicles carrying legally authorized electronic tags can enter the mine loading and weighing area, thereby improving the safety of the area.
Simple structure
Convenient debugging and installation, wide weighing range and strong adaptability.
Can transmit information over long distances
It can carry out remote control and group control, so that the system can be truly automated and intelligent, and it can be networked with a computer to automatically analyze, calculate and print data records and reports.
Strong data confidentiality in the label
Electronic tags cannot be forged or copied, which fundamentally eliminates the phenomenon of copying, forgery, and cheating. .
Establish corporate image, improve work efficiency, and reduce operating costs
The system performs computer automated network management on all truck scales (weighbridges) in the mine. It can easily measure the weight of the truck when it is empty and fully loaded, and understand the actual weight of the cargo loaded on the truck in real time, thereby greatly improving The work efficiency of the enterprise.
Avoid human operation loopholes
Due to the method of automatically reading data, all over-balanced vehicles are automatically counted by the computer, eliminating manual intervention, automatically recording data, and automatically verifying and releasing.
Shorten the operation time of each operation link, improve the connection and unloading ability of the metering system, reduce labor intensity, and save labor costs.
5. Other application areas
Weighing management of various mines;
Construction incoming weighing management;
Crops weighing management;
Industrial weighing management;
Weighing management on the battlefield, etc.
[ad_2]