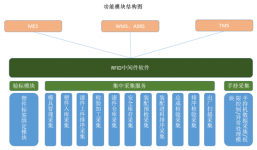
Industry 4.0 Smart Manufacturing Solutions
[ad_1]
I. Overview
1.1. Construction background
With the increasing automation of industrial production, machines have taken over most of the manual labor and also part of the mental labor. Industrial production capacity has surpassed human consumption capacity. Humans have entered an era of overproduction, and the life cycle of products has also been This has been greatly shortened. In the past, mass production would have caused overcapacity. Products made with the one-size-fits-all approach in the past cannot meet the needs of current users.
The Internet has changed this situation. People can be connected with people and manufacturers at low cost, so that everyone’s individual needs are amplified, and people are more and more like personalized things. However, the demand for personalized things is not so large, which requires industrial enterprises to achieve fast, small-batch, customized production.
The realization of intelligent production requires the requirements put forward by the business system. The manufacturing execution system is responsible for the execution, monitoring and management of production. Intelligent manufacturing is based on the interconnection of the original management system and machines, adding the management of production equipment and raw materials, and the management of machines and The management between machines, through the management of production raw materials, can realize product customization, multi-variety, and small-batch production.
The use of RFID electronic tags for raw material management can track and record all the attributes related to each component, including the production process, the next process, its own color, size, and even the number, flow destination or customized customer after assembly into a finished product. Information can be refined production according to customer needs, and when raw materials begin to flow into production, it will gradually enter the customized production link. The controller can communicate with RFID electronic tags wirelessly, and can replace the original bar code technology. RFID electronic tags can be read remotely and in batches, avoiding the shortcomings of bar codes that must be visible to be read. It can be automatically detected at the inspection station. Recognize and add quality data. The warehouse can automatically recognize the warehouse in batches, and the sequence can be automatically identified, which greatly improves the production level and avoids the adverse effects of human operation errors or omissions. At the same time, RFID electronic tags are printed with chip barcodes on the surface, which can be compatible with old equipment and avoid asset waste.
RFID technology has the following advantages in intelligent manufacturing:
1. There is no need to contact, the whole process does not need manual intervention, can complete the automatic data collection and is not easy to damage;
2. Information can also be collected for objects in operation, and multiple cards can be recognized at the same time, which is more convenient to operate;
3. It can be applied to a series of requirements such as harsh production environment, unreachable personnel, large data storage capacity, high real-time data transmission requirements, and reliable and effective data transmission.
Generally speaking, RFID has great application prospects for real-time data collection in the working environment of intelligent manufacturing, warehousing, and logistics. It realizes the integrated management of raw materials, factory manufacturing, sales, and customer needs, and can be flexibly and on time. Production, on-demand production, sequential production, etc., to achieve true intelligent manufacturing.
The following describes the industrial 4.0 intelligent production and manufacturing solutions by explaining the production process of the parts production plant in the automobile manufacturing industry.
1.2. Construction content
Automobile production is facing multiple platforms, multiple models, and extremely flexible requirements. If traditional parts pulling methods are used, sufficient inventory must be prepared for each type of parts in the warehouse. As the models increase, the area of the production line of the automobile production plant It will not be enough to support the placement of parts and the normal operation of production.
Sorting and pulling (JIS) classifies similar parts through the on-line sequence of the vehicle and the vehicle BOM, and placing them in a sequence consistent with the production of the entire vehicle to pull the parts. The sorting and pulling method of parts can help automobile manufacturers save in-plant parts Use area, increase the turnover rate of parts, and further enhance the flexibility of engineering production.
As a spare parts supplier that provides paint parts for automobile manufacturers, it is necessary to use RFID technology to bind RFID electronic tags from injection molding to realize buffer storage, painting sequencing, inspection processing, paint warehouse, pre-inspection, assembly sequencing, Full-process automatic data collection and quality control such as final inspection, outbound sorting, factory inspection, etc., to achieve large-scale product tracking, quality control, inventory control, optimize production lines, warehouse management planning, and meet the requirements of automobile manufacturers’ pull sequencing (JIS) Need to innovate the management model, improve the management level, further break through the bottleneck of production construction and warehouse management, and reach the level of industry 4.0 intelligent manufacturing.
2. System design
2.1. Construction scope
Through the construction of the RFID system, the main material flow in the user’s production process is tracked, monitored, noted, and counted.
Monitoring range:
The logistics entrances and exits, personnel entrances and exits of the workshops of the whole plant, the external entrances and exits of the plant, production lines, workstations and warehouses;
Monitoring object:
All large products (bumper + threshold + spoiler);
Scalable:
Automatic three-dimensional warehouse for personnel access control and product turnover equipment;
Monitor the logistics chain:
Injection molded parts → plastic parts buffer area → spraying upper part area → spraying off-line inspection area → painted parts storage → assembly pre-inspection → assembly assembly final inspection → assembly sequence → factory gate inspection.
Large storage and identification form:
Single or batch injection molding production, sorting (multiple forms), station inspection, batch warehousing and exit, and factory inspection;
Transport form:
Side door, rear door, container.
2.2. Key points and difficulties of construction
The system and equipment are simple to deploy, stable and reliable in the production environment of the factory, and maintainability is good. The ability to monitor and manage all equipment through the management platform is the basis for the success of the system;
The ability to accurately identify the position of the plastic part before spraying and the pre-installation and assembly sequence is the key to the success of the project;
The device supports dual-signal output, and the collected data can be transmitted to the collection server at the same time as the same data can be transmitted to the local workstation, which greatly improves the real-time performance of the system and ensures the integrity of the data to cope with different abnormal conditions. This is the success of the project. Protection.
2.3. System function and architecture
The system is mainly composed of split batch identification equipment, integrated identification equipment, access door, handheld mobile acquisition equipment and centralized acquisition server. The data of all readers are transmitted to the acquisition server through the network and stored in the database. At the same time, it supports local RS485 The interface is transmitted to the local IPC (workstation), and the readers of each functional area (work section) upload the read RFID data to a specific collection server, and connect with the upper-level system (WMS/MES/TMS) through the data interface.
2.3.1, system function module
The system function module consists of label binding module, fixed equipment centralized collection service, handheld terminal collection and exception handling. The data is connected with the existing MES, WMS, and TMS through the middleware server to share the database, as shown in the following figure:
2.3.1, system network architecture
The hardware architecture is shown in the figure below:
All equipment communicates with the collection server through the network, and the existing MES is connected with the collection server through the database. All the required data is obtained on the collection server through the database middleware, which reduces the difficulty of existing system transformation, and at the same time, it can distinguish work responsibilities and facilitate Post-maintenance and troubleshooting, and can increase the security of the server, can minimize openness, provide maximum transformation, and improve production efficiency. The hardware architecture is shown in the figure below:
All devices can support two simultaneous outputs, one RJ45 output, and one RS485 output. While outputting data to the acquisition server, it can output one data to the on-site workstation for quality data input, improving the response speed of HMI and improving the production of each beat efficient. At the same time, when the network is blocked or interrupted, the on-site work can not be affected, and when the network is restored, the data generated during the network interruption can be synchronously uploaded.
2.3.1. System middleware and mechanism
The data collected by the collection server is filtered, and useful information is inserted into the database. MES and other systems are processing business logic. When the information of plastic parts or paint parts needs to be identified, the system automatically queries the current station or process collected RFID tag information, and then translated to find relevant information and processed, instead of the original manual scanning bar code steps, through RFID long-distance wireless identification to achieve automated production management process.
[ad_2]