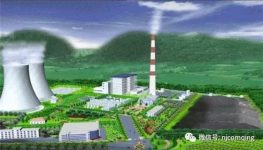
Smart power plant-point inspection system solution
[ad_1]
development trend
Smart power plants are the third important historical stage in the development history of power plant automation (informatization) in my country:
?1991-2000 (automation phase)
Enter the digital computer (microprocessor) automation stage marked by the comprehensive promotion and application of the Distributed Control System (DCS).
Production control automation
Handwritten records
Manual comparison

?2001-2015 (network phase)
The power plant information system (automatic system) has entered the stage of networking.
Online production data
Online management
Comprehensive decision-making online
? Early 2016 (intelligence stage)
Starting from the compilation of the “Smart Power Plant Technology Development Program” organized by the Power Generation Automation Professional Committee, a new period for the construction of smart power plants is about to begin.
One-key start and stop
Digital mobile interaction (smart point inspection)
Personnel positioning safety production management system
Digital Power Plant Intelligent Management System
Energy-saving optimization system
Based on big data analysis system
client needs
?? High security risks
Safety production has always been the lifeblood of power plants. The root cause of steam pipe leaks and dangerous goods leaks in power plants is that management is not in place and difficult. It is often difficult to control whether staff follow the company’s safety production requirements.
?? Difficulty in positioning personnel
For large enterprises with hundreds or even thousands of employees carrying out production activities at the same time in the factory area, if the enterprise cannot accurately grasp the actual location of the personnel, the time of arrival and other data, it is difficult to improve the efficiency of production and control.

??Difficult to return data from point inspection
The current patrol inspection management information system is relatively backward in function, which makes it impossible to meet the modern management requirements of production information, which is not conducive to early detection of defects in the equipment, and affects the safety, stability and economic operation of the equipment.
The inspection method is unscientific, easy to be modified and no electronic management;
During the inspection process, missed inspections and wrong inspections occurred from time to time;
The inspection data cannot be uploaded and shared, and the data cannot be effectively analyzed; etc.
The smart power plant is based on the digital factory, using the technology of the Internet of Things and equipment monitoring technology to strengthen information management and services. On the basis of traditional power plant safety production management, through the Internet of Things technology, three-dimensional digital technology and advanced safety monitoring and positioning technology, the integrated monitoring of industrial processes and plant security can be realized to avoid misoperations, reduce personal injury and death accidents, and improve the overall performance of the power plant. Safety management level.
solution
Based on the informatization construction of power plants, we have created a comprehensive solution from wired network, wireless network, personnel location inspection, network security, operation and maintenance management, etc., to help power plants complete the construction goals of smart power plants!

?Point inspection wireless coverage plan
Deploy different wireless devices for different scenarios
Production workshop, etc.: IoT gateway
Office: Installed AP
Outdoor environment: outdoor AP
?RFID inspection program
Through the establishment of the positioning system in the factory, for mobile materials, inspectors can check their location, inspection status, and whether they have missed inspections in real time in the background to realize intelligent inspections; managers can view the inspections of inspectors in the background Whether the time length, inspection track, completion degree and other indicators meet the requirements, management inspection personnel regulations
Standardized inspections to ensure safe and normal operating procedures.
?? RFID material management positioning program
It can position and monitor all kinds of materials in the power plant, and check the real-time location, storage and exit records, and transportation trajectory information in the background, so as to achieve accurate storage and intelligent management and control.For important goods (valuable goods or dangerous goods), a safe area can be set, once
Beyond the timely alarm, it can effectively prevent theft or avoid safety accidents and eliminate hidden dangers.

?? RFID personnel management positioning program
It can locate and manage all workers in industrial fields such as chemical plants. In the background, they can view their location, whether they are on duty, working hours, and activity trajectory in real time, which can help optimize their operating procedures, strengthen management, and improve work efficiency.
You can view information such as the time of entry and exit of foreign visitors, activity tracks and other information in real time. Electronic fences can be set up in specific areas (dangerous areas or important areas). Safety.

? Personnel/equipment positioning
Know the location of key objects in real time, and make accurate positioning in the first time when a danger occurs.
?Behavior trajectory
Accurately record the movement trajectory of key objects to facilitate the tracing of problems
?Equipment point inspection
Regular inspection of equipment, real-time monitoring, and timely feedback of abnormal data
? Dangerous warning
Hazardous areas, to be able to remind visitors and other non-related personnel not to approach
Case study
The daily inspection of a thermoelectric power plant uses a semi-automated method, that is, when the inspector arrives at the inspection point, he scans the code to sign in and manually records the equipment operation status. After all the inspection points are inspected, they return to the office and enter the data into the inspection. In the system. If you encounter a failure during the inspection process, you need to return to the office to manually open a work order and notify the maintenance team to perform repairs. This kind of inspection method is prone to problems such as missed inspection, inadequate inspection, and inadequate inspection.
In response to the above problems, a “wireless point inspection solution” was proposed. By deploying a wireless network on the inspection line, in conjunction with a handheld wireless PDA, the entire inspection and work ticketing process was completed. The inspectors use the handheld terminal to scan the code and sign in. At the same time, they record the equipment operation data on the handheld terminal and directly transmit it back to the inspection management system through the wireless network. If you encounter a failure during the inspection process, you can use the mobile terminal to issue a work ticket to notify the maintenance team to perform the equipment, which truly realizes the “paperless” inspection and greatly improves the work efficiency.
[ad_2]