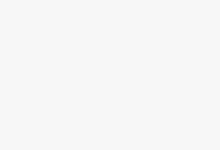
sh-rw urban muck truck transportation management project technical plan
[ad_1]
1. Project topology diagram
2. Summary of the technical route adopted by the project
As shown in the previous section, this project is mainly composed of 5 parts:
1. Vehicle-mounted RFID electronic tags;
2. Mobile handheld or fixed card reader;
3. Video recording devices at transfer points and disposal points;
4. The city data center computer room network and server, storage, database and other back-end equipment;
5. Monitoring center management command system.
Managers of the City Appearance and Environmental Sanitation Department, relevant personnel of the urban management departments of various districts (parks), information personnel of various construction waste management and service enterprises, etc., use the Internet and rent the operator’s 3G/GPRS, optical fiber network and third-party GPS platforms (including electronic maps), Through the “Construction Waste Transportation and Disposal Monitoring Platform System” software, real-time, all-round, and full-line monitoring, statistics, and consulting management of waste transportation vehicles are realized.
3. Software technology architecture and system
Taking into account the object-oriented regionality and decentralization of construction waste transportation and disposal management, in order to improve system performance and better realize data sharing, the system uses a mixed mode development (B/S+C/S mode), that is: only in the system The RFID electronic label management system (issuing RFID cards, data initialization, etc.) that needs to be completed internally and requires high data confidentiality uses the C/S client form; while other systems that achieve data access through the Internet use B/S development, such as Information query modules of the urban management departments of each district (park), etc.
The system is built on the Microsoft product system, using the SQSERVER2008 database, programming with the .NET series of development tools, the server uses the Windows server 2008 series of operating systems, and the client runs on the Windows XP, Windows Vista, and Windows 7 series of operating system platforms.
Considering that the equipment in the computer room is uniformly placed in the data center computer room of the city data center, security and backup are unified with the existing bakbone in the data center computer room for backup management.
The application software consists of the following three systems:
RFID real-time monitoring system for construction waste transportation vehicles;
Image and video remote monitoring system for construction waste transportation vehicles;
Inspection and supervision system for construction muck transportation vehicles;
The above three systems can operate independently and complement each other.
4. Introduction to the functions of each subsystem of the hardware equipment
1. Vehicle-mounted RFID electronic tags and card readers
Install an anti-disassembly active RFID electronic tag for each construction waste transportation vehicle, and enter the relevant information of the vehicle (such as: model, driver’s name, license plate number, load capacity, affiliated company, etc.) to the card, and then supervise RFID card readers are installed in places (fixed card readers can be used in fixed places, hand-held card readers can be used in temporary places), and information such as the arrival or departure time of each construction waste transportation vehicle will be automatically read , And synchronously transmit to the background server through the built-in GPRS module of the card reader. The supervision center extracts the information of the scene and the departure place for comparison, and can immediately find out whether the vehicle has been dropped halfway and whether it arrives within a reasonable time, etc. Taking into account the appearance of unmanned on-site, the system supports unattended, and the fixed RFID reader is automatically triggered to read the card when the vehicle passes by.
The fixed card reader should have: waterproof, lightning protection, high temperature resistance (above 60 degrees Celsius), low temperature resistance (below minus 5 degrees) and other functions.
After the RFID card is legally verified, it will be based on the installation of the card reader to install a signal light linked with the card reader. The card reading success signal light flashes to indicate that the card is successfully read, and the driver can drive away.
2. Camera and video device
It is composed of a video trigger device, a camera device, a background network storage server, etc.
When the vehicle passes the recording point, it is sensed by the fixed card reader to trigger the start of the photographing and camera system to complete the photographing of the vehicles passing by and the recording for a fixed period of time (about 5 seconds). The recorded video data is stored in the network storage server under the file name of the vehicle’s “RFID card number + the time of starting shooting (year, month, day, hour and minute, each with two digits)”. If the card reader is unsuccessful in triggering, you can use the spare embedded ground sensing coil to trigger the camera to take pictures.
The hard disk capacity of the network storage server shall be sufficient to store one month of photographic and video data as the standard.
According to a construction site, there are 20 muck trucks transporting at the same time. Each muck truck is transported 20 times a day. Each video recording time is 5 seconds. Shooting calculations are performed, and there is no need to record when the actual vehicle returns.) The capacity of a 1024*768 photo in JPEG format is generally less than 400K, and the capacity of each photo taken every day is about 313M. The total data volume of “photo + video” is about 1090M, which is about 1G, 30G in one month, and 30G*80=2400G in one month for 80 construction sites.
Note: Due to the limited investment budget for the current period, only fixed card readers were considered for installation in 80 construction sites, and no video recording devices were considered. It is planned to upgrade and install the camera and video system when the system is completed and runs smoothly for about three years, when the second phase of the project is implemented. Therefore, the actual data volume is less than 1T.
Since the construction waste transfer point or disposal point is the place where construction waste transportation vehicles gather, the construction waste transportation vehicles at each construction site will arrive in a concentrated manner, and the number of collections is far greater than the starting point. Nevertheless, we calculate based on 10 times the traffic volume of the construction site, and the storage of photo, video and video data of 10 fixed disposal sites for more than one month only needs to be equipped with a hard disk of more than 1T.
The longevity, high-brightness spotlights and flashes installed in advance are used to compensate for the illumination at night. The camera adopts high-definition, outdoor waterproof box camera or dome camera with infrared night vision shooting function.
3. Data transmission platform selection
According to the environmental requirements of the unloading points in each district (park) of Ningbo and the communication and negotiation with the operators, it is determined that the operators shall lay optical fiber links to the unloading terminal points at 10 muck unloading points. And to ensure that the various unloading point equipment is provided to work on the same network segment and can access each other, and the real-time link communication is maintained between the opposite end of the network and the Ningbo data center server.
1. Snapshot of the muck truck picture and video file transfer platform
The vehicle successfully triggers snapshots and video clips at each unloading point, and the optical fiber link laid by the mobile operator to each unloading point is integrated through the internal integration of the mobile operator. The entire optical fiber link from the unloading point to the server in the data center is independent The optical fiber channel enables data verification in the entire data transmission channel to ensure the independence and security of video file transmission. The convergence point is connected to the video server (the video server is equipped with dual network cards, one is used to receive photos and video files transmitted by each off-loading point, and the other is connected to the public private network of the e-government extranet). The public private network connected to the e-government extranet and the network that accepts video files are on different network segments, so that the video transmission network and the public private network of the e-government extranet are logically separated.
1. GPRS service data transmission platform
After the successful verification of the muck truck at the starting point, the GPRS module on the fixed card reader (or handheld patrol card reader) directly accesses the e-government extranet through the wireless network and transmits the data of the muck truck to Ningbo City. The back-end server of the data center is unified and cost-effectively counted by the back-end management software.
Managers of the City Appearance and Environmental Sanitation Department, relevant personnel of the urban management departments of various districts (parks), and information personnel of various construction waste management and service companies access the WEB server for all business browsing and processing.
4. Data center computer room equipment
According to the requirements of the project approval document, this project does not set up a separate computer room. All networks, storage, blade servers, databases and security equipment are hosted in the computer room of Ningbo Data Center. According to the negotiation, the main equipment that needs to be added in the computer room and dedicated to this project is as follows:
Server: 1 set of blade server rack, 1 set of database server; 1 set of WEB server; 1 set of high-performance video server.
Storage: 1 set of disk array system, mainly used for backup and storage of photos and videos transmitted from each camera and video point, as well as the original information of all muck vehicles.
The remaining hardware (such as network security equipment, monitors, KVM, etc.) can use the existing equipment in the computer room of the Ningbo data center.
5. Monitoring and command center equipment
The monitoring command center is located in the Environmental Sanitation Department of Ningbo City and mainly undertakes the following functions:
Real-time monitoring of the trajectory of muck vehicles;
Play back and compare the original recorded photo data of the offending vehicle;
Handling and making administrative inspection notices for illegal vehicles.
etc. The construction of the center includes the following main equipment and contents:
Basic decoration, including: electrostatic floor laying, precision air-conditioning installation, monitoring wall installation and UPS system procurement, etc.
The network switch realizes the access and connection between the internal departments of the City Appearance and Environmental Sanitation Department, and the management network system of the City Appearance and Environmental Sanitation Office and the network of the central data room.
Large LCD TV screen, real-time monitoring of the GPS running track of the vehicle on the electronic map; when the case is being demonstrated and processed, the relevant personnel collectively view the replayed image or video, etc.
5. Introduction to third-party platforms and software functions
1. GPS platform
The system uses the electronic map system of Ningbo Institute of Surveying and Mapping, and realizes real-time supervision of the operation route of construction waste transportation vehicles on the established GPS platform of Ningbo construction waste.
The system has been tested in the City Appearance and Environmental Sanitation Department and the effect is good.
2. System software
Database system: Microsoft SQL-Server 2008, 1 set.
Server operating system: Microsoft Windows server 2008, 3 sets.
Client operating system: Microsoft Windows 7, 2 sets.
Data backup system: Bakbone (including 1 file backup module, 1 SQL database backup module), 1 set.
Video recording processing system: video processing software (domestic), 1 set.
3. Application software function module
The application software in “Ningbo Construction Waste Transportation and Disposal Supervision System Project” consists of the following subsystems and functional modules (as shown in the figure below):
Function description of each system module:
RFID real-time monitoring system for construction waste transportation vehicles
1) Database management module for construction waste management and service enterprises
This module is responsible for the unified collection of construction waste management and service enterprise information in each district (county) to form a unified construction waste management and service enterprise database. The system adopts hierarchical authorization management. Each district (county) urban management department can query, maintain and manage the enterprise database information in its own jurisdiction, and the municipal urban management department can query, maintain and manage the city’s enterprise database.
2) Construction waste transportation vehicle management module
This module is responsible for the management and maintenance of vehicle information reported by construction waste management and service companies. By installing RFID equipment on the vehicle, and binding the vehicle information with the RFID equipment, the vehicle can obtain unique identity information in the system.
3) Load point, transfer (unload) point information management module
The function of the loading point and transfer (unloading) point information management module is mainly to collect the information of the city’s construction sites and unloading points into the system to form a unified loading point and unloading point database. The relevant staff can check the loading point and unloading point. Unified management of the information. The information of the loading point mainly includes: the name of the construction site, the geographical location of the construction site, the contact information of the construction site management personnel, the construction unit, the start time, the completion time, the amount of slag, the total excavation amount, the total land area, and the mud The information of the unloading point includes: the name of the unloading point, the geographic location of the unloading point, the contact information of the unloading point management personnel, the total amount of consumption, the annual consumption capacity, the use period, etc.
4) Vehicle RFID management module
RFID equipment is divided into RFID electronic tags and RFID readers. The main functions of the equipment management module mainly include the following aspects:
(1) Initialize a new RFID electronic tag;
(2) Initialize a new RFID reader;
(3) Binding the electronic tag to the construction waste transportation vehicle;
(4) Binding the reader to the construction site and unloading point;
(5) Change of electronic label information and reader information.
5) System initial database management module
This module is a platform for unified management of initial information such as user accounts, system roles, districts (counties), and permission assignments. For each type of information, the system provides functions such as addition, deletion, and modification. In addition, the system divides users into three categories: users from the city urban management bureau, users from district (county) urban management departments, and users from construction waste management and service companies. According to different business needs, the staff can set up different types of users in the system to query and Statistics authority.
6) Manually complete the processing module manually
This module is mainly responsible for processing incomplete card reading records. The muck transportation vehicle submits a manual completion application, and the district (county) environmental sanitation department verifies by video (or other means). If it is indeed normal operation, the district (county) ) The urban management department manually completes the incomplete records for normal statistics and billing.
7) Job query module
The system provides different query permissions for each role. For example, the city urban management department can query the transportation records of the city, each district (county) urban management department can query the transportation records of their respective jurisdictions, and each construction waste management service company can only query the company’s transportation records. Transportation record query; the system supports multiple conditions and complex queries. The staff can query the transportation records according to the jurisdiction, project name, operating company, reader, vehicle, operation status, and operating time period. It can perform single-condition simple query or conduct Complex queries with multiple conditions.
8) Statistical analysis and assessment module
The statistical analysis and assessment module is mainly used for construction waste business service companies to analyze their business vehicles, operating conditions, output daily reports, weekly reports, monthly reports, etc., real-time statistics of normal trains, statistics of abnormal trains, etc. The statistics used by industry management departments mainly include construction site statistics, statistics on operating vehicles, and statistics on abnormal vehicles. It also includes area-based vehicle operation statistics, abnormal statistics based on loading and unloading points, and vehicle number statistics. Provides the generation and output of various statistical reports for the management departments, operating service companies and the city bureau personnel, and provides the basis for the city bureau’s assessment of the district (county) urban management departments and the district (county) level urban management departments’ self-examination.
9) Expense settlement module
The system automatically counts the normal workload during the settlement cycle for each company based on the operating conditions of construction waste business service companies, and generates an expense statement. Each enterprise can print the expense statement online and stamp it by management departments at all levels. Settlement fees to a special account later. In addition, the system also provides an expense settlement query function. Enterprises can query their own expense settlement records online, and urban management departments at all levels can also query the settlement records of all enterprises within their jurisdiction.
Image and video remote monitoring system for construction waste transportation vehicles
1) Recording equipment management module
Equipment management is responsible for the unified management of network cameras at various construction sites and transfer (unloading) points. Its functions include: equipment access, equipment deletion, equipment information management and channel management, etc.; support PTZ control, staff online acquisition and modification The focal length, aperture, contrast, chroma and other indicators of the remote video equipment.
2) Real-time monitoring module
This module automatically connects the network camera at the unloading point according to the IP of the video recording device to realize the real-time transmission and monitoring of the operation video of the transport vehicle; it can also start the recording program of the remote network camera online to manually record the operation of the work vehicle at the unloading point.
3) Video and image file library management
The video files and image files of the unloading point network camera equipment are transmitted to the information center server in real time through the network, and are classified and stored according to the device name and file type (can be divided into: alarm trigger, manual recording, etc.). The management personnel can check the video and image File management; support users to manually delete useless video files.
4) Video and image playback processing module
The module supports online playback of video, video files and image files in the image library, and the system supports file query functions. Users can follow the channel name, time, and file type (can be divided into: timing capture; manual recording; alarm trigger), etc. Conditions to query the video, image file library, and use the player to open the video file to achieve online playback.
5) Device log module
The log management user records the alarm conditions of each video recording device and the operations performed by the user on each video recording device. The specific functions are as follows:
Log query: The user can query the log according to the construction site or unloading point (equipment name), log type (alarm log, operation log), time period, and operator. The query results show: construction site (or unloading point name), operation time, operator, and operation content and other information.
Log export: The system supports the function of exporting the log to an Excel file.
Log removal: For obsolete logs, in order to keep the logs at a certain scale, managers can periodically clean up manually.
6) Alarm management
This module provides alarm management of various failures of hardware equipment, which is convenient for managers to find equipment failures in time and provide a basis for troubleshooting. The system supports setting alarms for each video recording device. The types of alarms include hard disk full alarm, video file loss alarm, block alarm, read/write hard disk error alarm, and system mismatch alarm. Once an alarm occurs, the system automatically writes the alarm information into the log.
Inspection and supervision system for construction waste transportation vehicles
1) Deduction rules database management module
The system provides deduction rules that define a variety of violations. The manager enters the type of violation, the violation and the corresponding deduction value. The system automatically records the deduction rules and forms a deduction rule database. Users can query, modify and delete the points deduction rule base.
2) Inspection and supervision notice module
Inspectors discovering the violation information of the construction waste transport vehicle may promptly notify the relevant law enforcement agencies based on the violation facts. The system automatically generates an inspection notice sheet, which includes information such as the violation facts, the deduction of vehicle scores, and the deduction of construction waste management server enterprise scores. The inspectors can print the notice sheet.
3) Data acquisition, buffering and transmission module
When patrolling with a patrol card reader (PDA), the patrol personnel can query the vehicle information database by reading the vehicle RFID electronic tag information to obtain detailed information of the vehicle and the transportation company to which the vehicle belongs, and combine the information of the illegal vehicle and the illegal facts. And it is transmitted to the system through the 3G (or GPRS) network. At the same time, when the network is blocked (or other reasons), the data cannot be reported normally, the module is also responsible for the data caching function, and temporarily saves the data entered by the inspector in the PDA device. When the PDA device can connect to the network, the system will automatically upload again.
4) Data query module
The data query module mainly uses the patrol reader device to realize the data query function. The data query module includes: basic data query and violation record query.
(1) Basic data query: Inspectors can query vehicle information and transportation company information based on the on-board RFID electronic tags, or query information based on the license plate number, the name of the construction waste management service company and other information.
(2) Query of violation records: inspectors can query the violation information database based on electronic tags, license plate numbers, transportation companies and other information.
Other data interface
The system provides a data interface to realize data with the existing “Building Waste Transport Vehicle GPS Driving Record System”, “City Appearance Sanitation Quality Monitoring System” and other third-party software of Ningbo City Appearance and Environmental Sanitation Management Office
[ad_2]