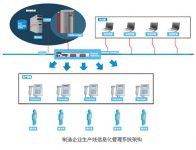
Information Management System for RFID Production Line of Manufacturing Enterprise
[ad_1]
1. Business requirements
There are thousands of types of spare parts, raw materials and products in production lines or warehouses of modern manufacturing enterprises. In reality, no matter how good the management model or system is, it is difficult to ensure the visual flow of the entire material, which brings management personnel It is a great trouble, and it is difficult to greatly improve the work efficiency. At present, all countries are using IoT barcode and RFID technology to implement fast and accurate positioning and status statistics of parts and raw materials in production to improve the production and management efficiency of manufacturing enterprises.
The production line information management system of manufacturing enterprises independently developed by Dingshi helps enterprises simplify business operation processes, reduce production costs, improve material inventory, product tracking, material management, and inventory management in real time, and greatly improve the quality of corporate customer service and Satisfaction.
2. RFID production line information management system architecture of manufacturing enterprises

Three, system function
1. RFID read and write function: 13.56 MHz RFID tags can be read and written.
2. Bar code reading function: It can read one-dimensional bar code or two-dimensional code label.
3. U disk data copy function: In the case that the network cannot be connected, the data temporarily saved in the collection terminal can be copied out with a U disk to ensure that the data can be submitted in time.
4. Process execution function: According to the designed process, input and output related data, and finally submit the collected data to the database.
5. Collection terminal online status monitoring function: It allows users to grasp the working conditions of all collection terminals, understand whether the collection terminal is online, and deal with problematic collection terminals in a timely manner.
6. Collection terminal process editing function: It can use input, output, and judge three kinds of operation design process.
Four, system characteristics
1. Rich application configuration
The system adopts Dingshi “PDT-A2 production data collection terminal”, which can read RFID and barcode labels; it can save data through the network and U disk to ensure data security; it can dynamically receive the background system control and adjust the working status in time; The system structure is flexible and changeable, supports custom design of data collection process, flexible configuration, and can be adapted to various applications.
2. Real-time tracking management
The Dingshi “PDT-A2 production data collection terminal” used in the system has TCP/IP network communication function, which can perform multi-level process step programming according to the actual situation to meet the needs of various production line control and management; it has strong tracking The management function can carry out remote real-time tracking and management for each link of the production management of the assembly line, the operators in each link, the operation steps, and the location of the production materials.
3. Efficient data synchronization
After the “PDT-A2 production data collection terminal” is granted to production employees, any operation of the authorized employees will be sent to the back-end server in real time. At the same time, the back-end server can issue prompt information to the collection terminal, prompting temporary changes in materials, etc. , The collection terminal can transmit collected data to the back-end server according to the instructions of the collection step, so that the collection system can be efficiently synchronized with the enterprise information system.
[ad_2]