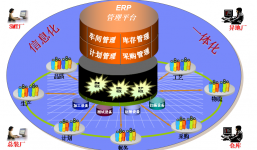
Digital factory solution–op lighting
[ad_1]
The overall plan of equipment management:
Through the introduction of equipment management modules, the channels for planning, execution and control are opened up to establish a comprehensive manufacturing management system that is both interrelated and self-contained.

Overall function of equipment management:

Through the standardization of equipment management, strengthen equipment overhaul and maintenance, reduce the impact of ineffective shutdown or equipment failure on production and improve the overall efficiency of equipment OEE.
The relationship between equipment management and MES and field equipment:

Equipment management-perfect equipment master data management:

1) Establishing equipment ledger-formulate equipment bar code rules, establish equipment ledger in the system, and equipment management personnel need to record in the system the storage, withdrawal, and return of equipment.
2) Generate equipment inventory—generate equipment inventory based on equipment status and access information, and make purchase reminders based on inventory status
Sample screenshot of device master data

Establish equipment/spare parts account information, and establish the association between the main equipment and the MES station, so that the MES can obtain equipment output and quality information, and perform related process control, such as job qualifications, etc.
Example screenshots of equipment in and out of the warehouse

1) Register the equipment/spare parts in and out records, and explain the reasons, such as requisition, return, etc. If the equipment status changes, the equipment status can also be maintained at the same time, such as scrapping.
2) Use PC or PDA according to actual situation
Equipment Management-Equipment Information Management

1) Document server: establish the server path for document storage
2) Data classification: establish the classification of equipment documents, such as operation manuals, maintenance manuals, etc.
3) Format classification: define the classification of PDF, Word, Excel, AVI, etc. to determine the browsing software
4) Document set management: a document set may include multiple documents
5) Document upload: manually upload or download documents from other systems
6) Data browsing: According to different file formats, the system automatically calls related software to open.
Equipment management-regular maintenance and repair plan

Establish regular equipment maintenance–in the system, equipment maintenance personnel maintain equipment maintenance cycle, maintenance frequency, maintenance code and other maintenance plan information, and provide maintenance reminders according to the process of equipment use.

When the equipment in the production process reaches the maintenance cycle or maintenance frequency, the MES system will give maintenance reminders through emails and kanbans, so that maintenance personnel can maintain the equipment in time.
Schematic diagram of maintenance rules:

Equipment management-equipment maintenance operation process

Schematic diagram of maintenance operations

Equipment Management-Spare Parts Usage Record
?Ordinary loading and unloading spare parts
?Such as a trolley
?Used and not in use through scanning records
?Parameter collection requires spare parts
? Such as steel mesh
? Collect the corresponding parameters according to the demand when going online, and give reminders according to the production output
? Spare parts with control requirements
?Such as Feeder, according to the material station table to prevent specification errors
?Establish a separate management process for business processes
Schematic diagram of spare parts usage

Equipment management-integrated solution with field equipment
Equipment management-integrated solution with field equipment
1) The main purposes of integration are: status (idling, running, stop) acquisition, output acquisition, barcode acquisition, data acquisition, standard setting, equipment control
2) Basic settings: Set basic parameters in MES, such as inspection parameters (time, current, power, etc.), inspection standards, acquisition frequency, etc.;
3) Set equipment parameters: MES will import the set parameters and standards into the specified file, and then import them into the equipment by the equipment program;
4) Integration method: The integration method includes: PLC interface (such as production line track, automatic scanning equipment), file interface (such as ICT equipment), program interface (such as AOI equipment, SMT throwing data), direct reading from equipment (such as FCT equipment), sensor interface (idle listening), manual scanning (devices that cannot be integrated), etc.
5) Unqualified information: control the operation of equipment based on unqualified information;
6) Standard comparison: Compare whether the test standard is consistent with the existing standard in MES;
7) Information upload: equipment test information is converted into quality and output information in MES and uploaded to MES for equipment/process efficiency analysis, such as OEE analysis.
Example diagram of integration method

Technology Architecture

Technical solution: offline collection solution under centralized deployment

Technical solution research: diverse data collection methods

Technical solution, reference: Barcode technology development and comparison

[ad_2]