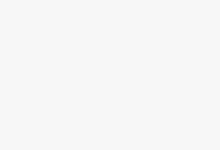
MES overall solution for weaving industry
[ad_1]
The MES manufacturing execution system is based on embedded technology as its core, and is supported by the self-developed wireless loom monitoring equipment WMC10X, production inspection equipment TIC30X, bar code label printing equipment BPS10X, Kaitai Intelligent Manufacturing Execution System, etc. Information solutions for the textile industry. This system collects and monitors the speed, efficiency, output, shutdown and other information of the loom in real time through the wireless loom data monitoring and collection equipment installed on the site of the weaving workshop; through the intelligent data collection terminal of the cloth production quality in the inspection workshop, it solves the production and defects of the cloth. Data collection and statistics issues; Barcode management of raw materials and grey fabric warehouses is realized through barcode label printing terminals and handheld barcode delivery equipment. The entire production process management system is mainly composed of loom monitoring, production inspection, blank bar code warehouse subsystem and finished fabric management subsystem.
The following is the topology diagram of the entire system:

instruction:
1. Preliminary preparation: In this link, register the shaft information in the system, and print the “machine flow card” at the same time, the machine flow card with the basic information of the shaft and a certain number of cloth bar code labels;
2. Weaving workshop: help the machine worker scan and scan the bar code of the “machine flow card” and the machine bar code pre-adhered on the machine through the handheld terminal when the cloth is dropped, to complete the binding of the shaft and the machine; at the same time through the handheld machine The keyboard input the number of meters dropped; the handheld data is imported into the database through the computer, and the data record of the dropped cloth is generated;
3. Inspection workshop: through the inspection intelligent terminal (see later for details), real-time collection of electronic data of cloth inspection, real-time upload to the server, and automatic generation of various output, quality, warehousing comparison reports; at the same time, each roll of cloth can print bar code labels ( Optional);
4. Precise barcode warehouse (optional): Scan code to enter and exit the warehouse according to the barcode label of the cloth roll.
1. Wireless data monitoring subsystem of loom

Loom monitoring belongs to front-line management. It is based on the wireless loom monitoring equipment WMC10X as the core to collect real-time production data related to weaving shafts, healds, upper shaft workers, machines, turnbucklers, security workers, and team leaders, mainly to achieve the following Features:
Wirelessly monitor the running status and alarm information of the loom.
Automatically calculate the amount of remaining yarn on the loom, and predict the time for the loom to operate.
Online display of loom current status, speed, output, efficiency, shutdown and other data, and provide monthly, weekly, daily, and hourly average data for comparison.
Associate the operation data of the digging, upper shaft and weaving shafts, associating the shifter, security worker, team leader and machine production data, and use these data to guide the production site management, while the back-end management provides reference and comparison data.
Automatically record the start-up time, number of start-ups, running time of each loom, and stop time and number of stoppages for various reasons. Count data such as the number of downtimes and downtime for various reasons in hours.
2. Production inspection subsystem
Production inspection belongs to back-end management. It is centered on production inspection equipment TIC30X, barcode label printing equipment BPS10X, and embedded data query terminal. It collects grey fabric inspection data in real time and associates it with the previous data. At the same time, it provides original electronics for barcode warehouse management. Detailed data. Mainly realize the following functions:
Through the custom defect keyboard and the code table sensor interface, the gray fabric output and defect data are directly collected, and at the same time, the gray fabric inspection data is automatically and accurately corresponded to the stopper through the front management machine stopper related data.
The weaving shrinkage is automatically calculated according to the inspection output and the length of the weaving shaft warp, which provides a reference for the proportion of raw materials.
It can generate output defect statistical report according to workshop, machine, product name, team, shifter, and inspector.
It is possible to automatically inspect the salary report of the team leader, shifter, and employee.
It is possible to inquire information such as the output defect of the car operator, the workload of the inspector, the output defect of the team, the upper shaft record, the heald record, and the maintenance and repair record in real time through the query terminal.
The barcode printer on the inspection terminal can print a barcode label for each roll of fabric, and give each roll of fabric an “ID card number” to realize the management of the gray fabric barcode.


Intelligent cloth data collection terminal


(Actual installation effect)
in summary:
The operation of this subsystem is based on a stable, reliable and reasonable network architecture and layout. A total of 3 coil inspection machines in the Wujiang Haicheng Textile Factory’s inspection workshop are equipped with a textile electronic inspection intelligent terminal (TIC). The TIC equipment is aggregated to the office area data through the network. The server is organized into a local area network together with the computers of statistics and management personnel.
All the inspection data are summarized to the server in real time, and the large amount of statistical work that was originally required every day can be omitted. The management personnel can view the output summary report generated in time. Through the physical inventory and electronic data comparison, the daily cloth is timely and accurate Library; Quality summary reports can provide managers with targeted data support for cloth quality. According to the system’s monthly output and deduction statistics for each shifter, piece rate wages can be easily calculated.
After the implementation of the system, each piece of cloth inspected in the inspection workshop can be printed out by TIC and the corresponding barcode label can be pasted on both sides of the cloth for future scanning out of the warehouse. So as to achieve accurate delivery management, the delivery code is automatically generated.
After the inspection sheet becomes paperless, the inquiries about the output deduction of the operator can be sent through the production quality SMS sending platform, and the output and quality deduction messages related to the individual of the operator are sent to everyone’s mobile phone in time after get off work every day.
3. White billet barcode warehouse subsystem
Barcode warehouse is mainly used for the storage and delivery of all kinds of rolled fabrics, and directly print barcode labels for the inspected grey fabrics (completed in the subsequent management). The barcode warehouse mainly realizes the following functions:
The refined management of grey fabric inventory can query the dynamic inventory and inventory distribution of the warehouse in real time.
Scan barcodes based on handheld computers to realize storage, storage, and inventory, automatically accumulate the total number of rolls and total meters, and provide shelf storage, storage, and inventory modes to save time and improve work efficiency.
Automatically generate the outbound code list according to the outbound barcode list of the handheld.

(Handheld shipping terminal)

4. Finished fabric management subsystem

1) Embedded intelligent cloth inspection terminal

1. Fully replace the traditional paper inspection form, and realize real-time electronic data collection;
2. Support code meter sensor interface, support metric system, code system length measurement, code table calibration;
3. Standardized defect keyboard, while supporting custom defect data entry;
4. Support the functions of cloth opening and cutting, stitching, complementing, etc.;
5. Support U.S. four-point fabric inspection standards and custom standards;
6. Automatically calculate the cloth quality level according to the defects and deductions;
7. Support label printer interface, real-time printing of bar code labels, marks, defect reports, label format can be self-defined;
8. Support network, U disk, card reader, printer, scanner and other interfaces;
2) Standardized supporting software modules
1. Support order and spot trading methods;
2. Support operations such as querying, adding, modifying, and deleting detailed data of the cloth inspection sheet;
3. Support shelf warehouse management mode;
4. Real-time query of inbound details, outbound details, and inventory details inquiries;
5. Support custom outbound code sheet printing;
6. Support multiple formats of query summary reports;
[ad_2]