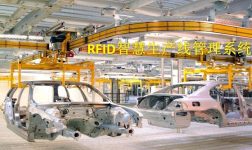
RFID smart production line management system
[ad_1]
Shanghai Anzhen Internet of Things Technology Co., Ltd. is responsible for the design, transformation and technical support of the smart production line system. Anzhen’s smart production system can help manufacturers perform more effective operations, reduce production line downtime, optimize remote material and component inventory, increase production efficiency, and maintain optimal output value, thereby increasing profitability.

1. Introduction to the system
The intelligent production line management system based on RFID technology combines the latest passive RFID technology and middleware software to form a complete set of Anzhen’s proprietary system solutions, which can help manufacturers solve many problems in daily production management and improve operational efficiency. Effectiveness, reducing production line downtime, optimizing raw material and parts inventory, thereby increasing and maintaining the optimal output value, thereby increasing the level of profitability.
2. System application
Workshop production line: For manufacturers, timely and accurate feedback information on the production line is very important. By placing RFID tags on products or pallets, and installing RFID reading devices at each node of the production line, they can understand the detailed working conditions of the production line. Thereby improving productivity and asset utilization.
Automobile production line: With the gradual improvement of people’s living standards and the increasing demand for automobiles, the automobile manufacturing industry is facing considerable production pressure. The use of RFID technology to monitor and manage the automobile production line process can strengthen quality control and tracking, and is effective Control costs locally and improve the competitiveness of enterprises.
Three, system characteristics
1. Automatically generate semi-finished product reports and finished product reports during and after processing.
2. Real-time tracking of inventory, assembling parts and spare components.
3. Keep the latest project information on the label in order to manage the production and assembly of complex or customized products, without the need to write separate assembly status and catalog tables.
4. The production date, code, batch and other information of the product can be automatically stored in the label.
5. At the same time, the information of the entire product processing process can be stored for searching during traceability, optimizing the management of parts, and improving product quality.
[ad_2]