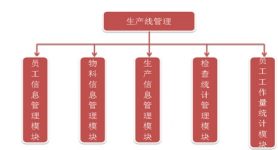
RFID-based smart clothing production line management plan
[ad_1]
1. System Overview
1.1. System background
China is one of the world’s largest textile and garment production countries. It has concentrated a large number of low-end and medium-end garment suppliers in the world, and the number of domestic workers in the garment production industry is a very large number. Compared with other industries, the clothing production industry has unique features: large-scale, small batches, multiple styles, short product cycles, strong seasonality, etc.; and at this stage, the clothing production industry is facing more and more competitive pressures, so , How to control costs, order production by sales, and make scientific forecasts are issues that the managers of garment manufacturers attach great importance to. In this field, most production companies still use more traditional production management methods (manual calculations, manual statistics, and barcode paper) to manage the data of the production line, which is low in efficiency and high in cost.
1.2. Status Quo and Analysis
In order to solve the above problems, new forces combineRFIDWith its own characteristics and advantages, it proposes an RFID-based intelligent clothing production line management plan. RFID real-time production line is the general trend of the garment industry, and its development prospects are very broad. The RFID real-time production line project of the clothing industry is also called the RFID electronic work ticket for the clothing industry, usually referred to as the electronic work ticket. It is the embodiment of a high-tech project that uses wireless workstations to cooperate with the apparel production management ERP system, and combines the management experience accumulated in the history of industrial production with the current tag reading and writing technology, data acquisition technology and other high-tech projects. Use RFID wireless identification and collection technology to replace the traditional counting, work ticket, and bar code recording mode of the workshop, breaking through the old framework. It has large information capacity, high real-time performance, diverse functions, fast and convenient operation, reusable, and long-term use Advantages such as low cost. With computer software, RFID readers, and networks, through the operation and recognition of the electronic tags carried on the pieces of clothing that flow to each production process, the entire production process can be monitored and managed in real time, including order execution and completion, clothing production progress tracking and Control, find the bottleneck of the assembly line, control the quality of clothing production, and calculate the wages of workers. Based on the accumulation of previous production information, it can also perform intelligent production scheduling and process improvements on orders to increase production efficiency.
3. System introduction
Garment production line management is a very large system that can integrate enterprise senior management, attendance management, purchase management, quality management, production line management, financial management, warehousing and logistics management, retail department management, etc. This program mainly introduces production line management.
3.1. The working principle of the system
Use RFID tag ID numbers instead of materials or products, record their corresponding materials and product parameters, and solve the fragility, inconvenience of searching, waste of resources and other phenomena of traditional printed labels. The labels can also be recycled, which can reduce costs and be environmentally friendly. The working principle of the system is as follows:
Grey cloth label
Equipped with an RFID tag for each grey cloth supplied, and record the material, color, purpose, cost and other information of the grey cloth on the RFID tag.
Staff Card
Each worker comes with aRFIDThe tag is used as an employee card. If the company has a meal sales system or plans to be equipped with a meal sales system, employees can be equipped with dual-frequency card RFID tags.
Station reader
A reader is installed in each station, which is used for employees to punch cards and write cards on labels on materials during production. Employees read their own employee tags once when they go to and from get off work. Each time they complete this process of a finished product (semi-finished product) during work, write the label on the finished product (semi-finished product) once.
The reader can be selected according to the needs of different workstations: if the distance is required, a long-distance reader can be selected, and portable equipment can be selected at the workstation where it is not convenient to install the equipment.
Inspection station
At the end of each production line, an inspection station is set up, equipped with a reader and a display tool. The reader reads the label information of the semi-finished product (finished product) that has been produced to determine whether there are process omissions and total statistics, and will meet the standard products Or the semi-finished product is replaced with a new label that has been initialized, and transferred to the next process production line. If it does not meet the standard, it is placed in the corresponding process non-compliant waiting area, and it is packaged and sent to the corresponding process for rework.
Automatically record statistics
The system automatically records which products each worker is doing during which time period, and how long it takes, and uploads the accumulated count results during this period to the server to count the employee’s piece-counting results, so as to achieve real-time recording of the employee’s workload;
Employee production query
Employees can check their production records throughout the day through the self-service card swiping terminal.
3.2. System structure diagram
Figure 1: System structure diagram
Staff Information Management Module
Use RFID tags to manage the personal information of employees.
Material Information Management Module
Through the RFID tag information on the material, it can automatically understand the situation of the production picking, such as: how much material is picked, what material, when to pick it out, which product is used for production, and calculate whether the picking amount and product output are reasonable. From this, we can get information about whether the material arrangement is reasonable, and whether the production scrap rate is reasonable. This result is helpful for relevant departments and colleagues to clearly adjust the material arrangement plan and product cost and price system.
Production Information Management Module
pass throughRFIDTechnology manages the production situation of the entire production line, what product is produced every hour, and can also analyze the production progress, difficulty, and estimated completion time of each product through the real-time tracking production information of this module.
Check the statistics management module
Use RFID to identify the clothing label information to check the product qualification rate on the production line. Specific to the people and processes, it can analyze which processes are prone to problems and whether the employees are skilled or not.
Employee workload statistics module
According to the employee’s card swiping record and the corresponding clothing card swiping record, the production output of employees is counted. The system automatically calculates the type, quantity, compliance status, bad product status, scrap status, and repair status of each employee every day and hour. Once the statistics are recorded in this module, relevant reports can be generated and uploaded to the financial and administrative departments and colleagues who need this report.
3.3. System Topology Diagram
3.3.1. Topology diagram of the overall system of smart clothing production
Figure 2: Topological structure diagram of smart clothing production system
[ad_2]