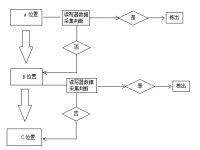
Application of RFID Technology in Sorting of Production Line
[ad_1]
With the rapid development of the global economy, the volume of trade around the world has continued to increase, placing higher demands on the entire logistics industry. As an important part of modern logistics, the automatic sorting system of goods is also facing severe challenges.
At this stage, logistics distribution centers widely use image recognition and barcode recognition technologies. Such technologies and equipment can effectively cope with the recognition and sorting of ordinary commodities, but the requirements for standardized packaging of commodities are high, and there is information in traditional detection methods. Shortcomings such as inaccuracy and slow transmission speed. In addition, many automatic sorting systems have extremely fast logistics speeds. It is difficult to achieve dynamic, fast and accurate identification by using conventional sorting control technology. Therefore, the RFID technology of the Internet of Things can solve this problem in time. The above scientific and technological basis RFID technology has the advantages of long reading and writing distance, fast scanning speed, simultaneous collection of multi-tag information, no orientation restriction, and strong resistance to environmental factors. This makes RFID long-distance radio frequency identification technology favored by major companies in the entire logistics industry. In the system picking, the RFID reader installed on the assembly line can collect the RFID electronic tag information on the item in the first time, and upload it to the upper computer, the upper computer gives a signal to the controller, and disposes of the item It can also be operated according to our actual needs, which is convenient and fast, and has high accuracy, which greatly reduces human error, reduces management costs, and improves efficiency.
Actual sorting system analysis and RFID benefit analysis
At present, the analysis of the sorting operation on the assembly line is as follows:
1. Using manual identification to identify the goods in circulation, it is easy to cause fatigue, so that missed inspections or error detections often occur, which affects the quality of the company’s finished products, and it is easy to cause certain bad effects on the company’s reputation in the market. Influence;
2. Data collection is relatively slow, and it needs to be entered into the system again after manual recording, which is cumbersome;
3. If barcode technology is used, the items need to be scanned one by one. When the barcode is contaminated and damaged by local friction, data cannot be collected, which affects efficiency;
4. Inventory efficiency is low and accuracy is low
The traditional method of inventory counting of goods is very inefficient, but timely inventory of goods is very necessary, and a lot of manpower and material resources are also spent for this.
5. Labor costs increase
Labor cost is now a very serious problem. Statistics show that the proportion of labor cost in the entire supply chain cost has risen to 30-40%.
Therefore, the use of RFID technology can solve these problems well. For the entire sorting system, we put an RFID electronic tag on each assembly line item, and arrange the RFID reader at a fixed position on the assembly line. Then you can collect the information of the circulating materials, and make the corresponding processing, for example, A, B, C, these three letters can represent the materials required by the three assembly lines, if the turnover box passes A line, scan the bar code, if it is A line The material will stop at the A assembly line and give an alarm light. If it is not, continue walking and scan to the B line. If it is the B line, stop at the B line and give an alarm light. If not, go down.
The scheme design is as shown in the figure above, simple and clear.
RFID system introduction
As shown in the figure above, when the product passes through the collection point, the reader/writer collects the tag information through the RFID antenna and sends it to the host computer to realize data collection and statistics. The entire system hardware includes RFID electronic tags, RFID readers and RFID receiving antennas. (For detailed information about the equipment, please refer to the parameter introduction of the attachment).
3.3 Introduction to actual operation
1. Label entry, when packaging products, the label and item information need to be bound and recorded in the system database;
2. Judge the assembly line, judge the label data at each position, and give the corresponding sound and light data to the staff, and the reader is connected to the mechanical equipment. When the material needs to be picked out, the conveyor belt stops, and after the pick out The pipeline continues to walk to the next step.
3. Manual picking and packing out of the warehouse.
……
System hardware configuration: RFID reader SFR-44
Antenna SFA-8R
And electronic label SFT-80
[ad_2]