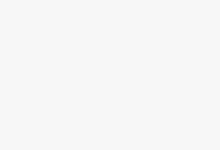
Cold chain logistics food safety supervision system
[ad_1]
System background
Cold chain logistics generally refers to a systematic project in which refrigerated and frozen foods are produced, stored, transported, sold, and are always in a prescribed low temperature environment before the end user, to ensure food quality and reduce food loss. It was established with the advancement of science and technology and the development of refrigeration technology. It is a low-temperature logistics process based on refrigeration technology and refrigeration technology as a means; it requires special equipment, and needs to pay attention to the transportation process, time control, and transportation. A special form of logistics in which the type and logistics cost account for a very high proportion of the cost.
Cold chain logistics is generally divided into four parts: refrigerated (frozen) processing, refrigerated (frozen) storage, refrigerated (frozen) transportation and distribution, and refrigerated (frozen) sales. Among them, refrigerated transportation and distribution are the weakest links in cold chain logistics. . Due to many factors such as environmental impact, technical limitations, cost, etc., the risk of product quality accidents caused by adverse factors in the process of transportation and distribution is much greater than that of other links. Moreover, under normal circumstances, enclosed goods are used for transportation and distribution, and this often brings difficulties to the subsequent identification of the cause of the accident, that is, when and where did the temperature of the item exceed the standard limit? Is it due to environmental factors or technical factors in the refrigeration (freezing) system? The solution of these problems requires a technology that can continuously record the temperature changes of items and store and send this temperature data to the background management system.
For temperature detection during transportation and distribution, the traditional method is to detect the end-to-end node temperature. With this technology, even if the temperature measured at the node is normal, it cannot guarantee that the temperature during transportation is always normal.
The transportation of cold chain logistics involves hundreds of items, and different items have different requirements for temperature and vehicle configuration. How to achieve the best operation, reduce loss and improve efficiency, my country currently lacks corresponding system standards.
To this end, Boao has launched a solution of “Cold Chain Logistics Food Safety Supervision System” based on 2.4G long-distance temperature radio frequency card, using RFID technology and combined with temperature sensing system to realize the cold chain logistics transportation and distribution process. Real-time monitoring of the temperature of items, or an alarm when the temperature exceeds the standard, can also record temperature changes during transportation and distribution, so as to help analyze the causes of temperature changes, and provide the most direct help to solve temperature changes. Contribute to the identification of responsibility for quality accidents. With the opening of the logistics industry, logistics investment will further increase, and the scale of the cold chain logistics market will also gradually increase, and these will create infinite vitality for the application of RFID technology in cold chain logistics.
System Brief
This project relies on the national science and technology support plan subject “Modern Logistics Service Demonstration Project”, with radio frequency identification (RFID) technology as the core, combined with the use of advanced technologies such as GPS, GIS, GPRS, and smart sensors to establish a cold chain goods container logistics monitoring network And the public safety supervision platform, including cold chain goods and status information collection terminal, vehicle-mounted real-time monitoring terminal, remote monitoring platform three parts, realize cold chain goods state monitoring and safety alarm, cold chain goods whole process information traceability and other functions.
1. System composition
Temperature electronic tag: the cold chain item and status information collection terminal, using 2.4G active electronic tag combined with temperature sensor technology, using the temperature sensor to collect temperature signals in real time, and transmit the temperature signals to the connected electronic tags, The electronic tag is responsible for processing these signals, and the processed signals are actively sent out in a wireless manner, so that a special card reader can collect this information. Installation method: directly fixed and installed in the carriage or container.
Fixed card reader with GPRS and LCD display: As a vehicle-mounted real-time monitoring terminal, it integrates RFID reader technology and GPRS technology. After normal operation, it can receive and demodulate the data transmitted from the tag in the carriage or container Then the temperature data will be displayed on the liquid crystal display, and at the same time the data will be sent to the remote monitoring center using GPRS.
Installation method: installed in the cab
Controller: Control the alarm function. During transportation, when the temperature exceeds the temperature range set for the item, an alarm will be issued. When an accident occurs, some items can be rescued in time.
Monitoring system: The remote monitoring platform is an important aspect of the system. Through this platform, the temperature changes in the carriage or container can be remotely monitored from time to time, and the information of the logistics process can be fully grasped.Facilitate decision makers to make judgments and decisions
2. Working principle
Working process: First, the temperature label will be loaded on the target item (box), when the goods are loaded on the car and set off, the system starts to work. The information collection terminal collects the temperature and status information in the container in real time, and writes it into the electronic label of the container regularly. The electronic label continuously sends information to the outside, and the card reader sends the received information to the monitoring center through GPRS, in the cab On the display screen, you can see the changes in the temperature of the goods. The remote monitoring platform realizes the reception and storage of all information, and displays the acquired information in a visual form or in the form of query, and interacts with cold chain transportation personnel in real time.
Background management: Due to various possible external factors and failures of refrigeration (frozen) equipment during transportation, the temperature of items usually changes. There is a large enough storage space in the active tag to place a sufficient number of temperature records. If the temperature change exceeds a preset range, the temperature change curve displayed on the screen will record this special situation. At this time, you can query the corresponding location and external environment based on this time to facilitate the exploration of the corresponding temperature change reason And make timely processing.
System Features
1. Basic Features
Real-time management and control of the entire logistics process, management and monitoring of the entire process of food leaving the warehouse from the origin, during transportation, and food arrival at the destination, helping companies to grasp the status of cargo transportation in a timely manner, reducing execution errors, reducing food quality loss, and enhancing The technical capabilities of cold chain logistics improve management efficiency, transparency and authenticity.
The accuracy and timeliness of reading information is high, reducing manual errors and delays, saving manpower and material resources, and minimizing the operating costs of cold chain logistics. Professional technical support, the latest technology in the field of RFID, has gathered the most extensive and most affordable 3 major identification technologies, which brings the development of cold chain logistics to a higher level.
2. Excellent performance
Using a new generation of temperature sensor RFID electronic tags, fully automatic identification, high identification reliability, 100% front-end identification rate; long identification distance (2-80 meters)
Very high anti-collision performance (can recognize 200 active cards at the same time), high recognition stability (error rate is less than one hundred thousandths), truly achieve no errors, no missing cards, fast recognition speed (the fastest possible 200km/h)
Traceability: The system tracks the entire transportation cycle of food, and centrally backs up the data to the information management center for analysis by management personnel, which is helpful for the traceability of quality accidents and the determination of responsibility.
Security, the system has a built-in security algorithm to ensure that only authorized users can read the data in the tag and ensure that all stored temperature and time records cannot be illegally modified. Real-time and comprehensive monitoring, so that any signs of damage can be effectively captured as soon as they appear, and play an early warning role for related emergency mechanisms.
Improve management level, centralized management, distributed control; standardize the supervision and management of cold chain logistics, and reduce unnecessary links.
3. System implementation benefits
Improve the information literacy and management level of employees
Improve the consumer confidence of food companies in the use of cold chain logistics
Timely handling of quality accidents, timely rescue of food
Promote the improvement and development of my country’s cold chain logistics links
Save food transportation costs
Discover the signs of quality accidents in time to reduce or even stop the occurrence of quality accidents
System technical indicators
System capacity A single card reader can recognize up to 200 active cards
Long-distance 2.4G active tag battery life battery life is not less than 5 years (the battery is a replaceable lithium battery)
Data transmission medium RS485/GSM, GPRS
Highest data timeliness real-time data
System functions
The cold chain logistics food safety monitoring system can monitor the temperature of food and its state in transit in real time, and has functions such as selection tracking and query.
Tracking: According to the information of the active temperature electronic tags installed in the container, the food in the logistics can be tracked and managed.
Query: Query the food according to the label ID, you can find out the name of the food, the number of the food, the current transportation location and transportation status of the food, etc.
Modification: The basic information of the food corresponding to the label number can be modified. The modification information includes: the name of the food, the number of the food, the temperature suitable for the food, etc.
Delete: Delete the food information of the completed transportation task.
Use this system to refer to and compare:
Before implementation: The use of traditional temperature monitoring methods can only monitor the end-to-end node temperature, which is relatively rough and cannot guarantee that the temperature during transportation is always normal;
After implementation: This system can be used to carefully understand whether the food has temperature changes during transportation and the quality changes that may be caused by it, and timely remedial measures can be taken.
Before implementation: Lack of real-time monitoring of food transportation and detailed temperature data records. When a quality accident occurs, it is very difficult to determine responsibility;
After implementation: Using this system, you can realize early warning of temperature changes during transportation/distribution, or record temperature changes during the process, so as to help identify quality changes that may be caused by temperature changes and the specific time of occurrence. The responsibility for quality accidents can be clearly identified.
Before implementation: The technology and capabilities of cold chain logistics are relatively weak, and it is difficult to ensure the quality of food well and comprehensively, which brings high economic costs to the enterprise;
After implementation: The use of this system has changed the traditional cold chain logistics methods, and the application of high-tech has greatly reduced the occurrence of food quality accidents, greatly reduced the operating costs of the enterprise, and has considerable economic benefits.
[ad_2]