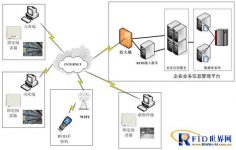
Digital RFID warehouse management solution for the clothing industry
[ad_1]
Chapter One Program Overview
1. Application background
Every day, fashion clothes are shipped out of the factory, and the cost of manual inventory, out-of-stock management, and anti-theft of these commodities continues to rise. Retailers are under pressure to maximize the return on investment in business processes. With the help of radio frequency identification (RFID), the entire enterprise value chain can obtain business intelligence, which provides important information for making business decisions quickly and accurately. After continuous development, RFID has become a mature solution, which can be used to understand the inventory situation more clearly and accurately, thereby reducing out-of-stocks, increasing sales and reducing cycle inventory workload.
As the volume of production and sales continues to increase, and the variety of commodities is increasing, some urgent problems have gradually emerged. First of all, it is an extremely large and cumbersome task to manually manage all types of goods in and out of the warehouse. In addition to manual scanning and input of barcodes, it also needs to confirm information in multiple links; second, traditional barcodes The system has obvious shortcomings, such as easy contamination, breakage, the need to stop waiting for scanning one by one, manual scanning is labor-intensive, etc., batch reading efficiency is not high, and it cannot meet the needs of fast and accurate; moreover, for multiple packaging boxes For large orders, the packing boxes must be disassembled one by one, which is time-consuming and laborious, and it is easier to introduce mistakes and omissions.
In recent years, XX brands have been imitated and counterfeited and other infringements have emerged one after another. However, due to the lack of effective anti-counterfeiting methods, the economic interests and brand value of enterprises have been greatly impacted.
In response to the above problems, we use RFID solutions and digital management systems to carry out informatization management of the entire process of inventory management, and integrate with existing enterprise information systems to build digital warehouses with modern commercial enterprises Management system. Not only can it meet the requirements of the distribution operation mode in modern logistics, it is suitable for large-scale busy logistics distribution, ensuring high-quality data exchange in the supply chain, and at the same time, through tracking solutions and supply Improving its transparency in the chain can effectively improve the level of warehousing and logistics management, save labor costs, and play a huge role in the management of the commodity supply chain.
Introducing RFID technology into the existing warehouse management, it can also automatically collect data from various operations such as warehouse arrival inspection, warehousing, outgoing, allocation, shifting, inventory counting, etc., to ensure all aspects of warehouse management The speed and accuracy of data input ensure that the company can grasp the real data of the inventory in a timely and accurate manner, and reasonably maintain and control the company’s inventory. Through the full integration with the existing enterprise ERP system, it is also convenient to manage the batch, source, etc. of the goods, realize the automatic comparison of the goods in and out of the warehouse, and automatically send an alarm when abnormal. Using the system’s location management function, you can also grasp the current location of all inventory materials in a timely manner, which is conducive to improving the efficiency of warehouse management.
RFID electronic tags have a globally unique ID code and cannot be copied, which can fundamentally solve the problem of anti-counterfeiting.
Successful case description:
In the past two years, Smith Barney’s large-scale expansion has been extremely rapid, with annual clothing output exceeding 100 million pieces, expansion of stores to 3,000, and storage capacity increased to 300,000 square meters… The burden on the supply chain has greatly increased, especially the inventory import and export volume has skyrocketed. The efficiency of picking and picking goods is rapidly declining, and goods are lagging in and out, making the front of the regional warehouses always full of cars, which has become the key to restricting the rapid linkage of the entire supply chain. For this reason, Smith Barney once lowered the warehousing sampling rate to 15% to improve efficiency. As a result, incidents of out-of-stock, wrong delivery, and over-delivery occurred frequently.
Once the RFID tag is added to the clothing, it is no longer necessary to open the box for inspection or random inspection when entering and leaving the warehouse, and the goods can speed up the batch circulation. According to the current technology, using RFID scanners, the reading rate of a box of 100 garments within 50-100cm is 100%. As a result, how many kinds of garments are in the whole box of goods, how many different colors and sizes are allocated, It is clear that the boxes of goods are scanned at one time and passed quickly. There is no need to review each item like a barcode. This greatly improves the efficiency of goods in and out of the warehouse and breaks the bottleneck of inefficiency in the supply chain.
For the same reason, the retail end also gets more convenience. In the receiving link, the type and quantity of the pre-received goods are set through the background, which does not require a lot of people to participate, and it can be completed quickly by simply scanning. When counting, place the goods on a dedicated counting table, and you can see the variety, color, size, and number of items at a glance. If the shelf of key commodities fails to be “all colors and yards”, the system will notify the clerk to replenish the goods, so that the shelf “changes with time”…
2. Construction goals
Establish an RFID automatic identification system for clothing products: Equipped with RFID electronic tags for clothing and other products, combined with fixed readers, handhelds and other data collection methods, to automatically identify and collect data in and out of the warehouse, so as to realize the automatic and rapid inventory of clothing products and timely grasp the inventory Quantity, monitor inventory assets, logistics and transportation of clothing products, and anti-counterfeiting traceability of clothing products;
Construction of a clothing product information business process management platform system: on the basis of the existing information system, through the application of the RFID system, docking and integration with the existing system, the establishment of a product information RFID management information platform system, and the electronic label logistics information with the enterprise scheduling plan information System interconnection, improve management efficiency, realize the transparency of the entire supply chain, and reduce enterprise operating costs.
Three, customer demand analysis
1. The system adopts a single product management mode, electronically labeling each apparel product that enters and exits, and the label uses RFID+barcode dual identification.
2. The system covers the central warehouse of the head office (1 location) and the second-level warehouses (more than 20 locations) of the store. There is a warehouse management system with a B/S architecture. Each branch connects to the central management platform through the Internet and the public network, and scans the information in real time. Upload into the system database. The main store and each store adopts single-door, single-out, single-entry, and the server is deployed in the headquarters building (not the main store).
3. The maximum quantity of goods to be identified is about 300 pieces at a time when the goods are in and out, and the maximum amount of a single order is about 4000 pieces. It is necessary to consider the situation of a single order entering and leaving the warehouse in batches.
4. The bill of lading must be checked simultaneously with the order, and corrective measures under abnormal circumstances shall be considered to realize manual intervention under authorization. Consider the manual adjustment of the order model and the actual delivery model (for example, the customer orders 16 yards, but the 15 yards of goods will be sent after the lack of stock consultation) and other situations.
5. On-site warning prompt measures must be taken for reading errors in recognition, and manual re-check and correction after the alarm.
6. Consider how anti-counterfeiting processing information is provided to customers for inquiries through the official website.
Chapter 2 Introduction to Application Scheme
1. Advantages of RFID technology
UHF RFID electronic label technology has the following technical advantages:
◆ Convenient and quick to read, can be efficiently and automatically identified
◆ Fast recognition speed and high data collection efficiency
◆ Strong environmental adaptability, anti-fouling
◆ The whole process is tracked, the products can be traced
◆ ID is the only one in the world, with high anti-counterfeiting security
◆ Dynamic real-time communication, real-time alarm
◆ The damage rate in the logistics process is greatly reduced
◆ Meet the needs of mechanization and automation in the operation process
Two, business application process
1. Storage
When the goods enter the warehouse through the warehouse entrance, the RFID information of each product is automatically collected by the import port reader. After pre-processing by the inbound access client, if it is a pre-ordered entry, it will be compared with the pre-accepted inbound order information For comparison, after all the order goods are in the warehouse, if there is an error or missing RFID tag information, manual intervention will be carried out. If the number or type of the goods is confirmed to be wrong, an alarm will be automatically sent to the business information platform; if other goods are in the warehouse, the The collected information is packaged and compressed and sent to the business platform system for filing, the back-end database is automatically updated, and product inventory records corresponding to warehouses and locations are added. According to the warehouse management information system, according to the pre-set positions of different types of goods, it can automatically prompt the corresponding goods positions where the goods currently in the warehouse are required to be stored.
2. Delivery
When the business platform system generates a bill of lading and sends it to the warehouse outbound client, if there are a small number of multiple types of goods, the picker can download the bill of lading with the handheld machine, and manually scan and sort the goods according to the bill of lading. The handheld machine will automatically prompt when the sorting error occurs Call the police and correct it in time; if it is a single type of bulk cargo, the picker will arrive at the designated location and push the goods to the outbound port with a cart according to the bill of lading. The outbound port reader will automatically identify the information about the outbound goods, and the goods will be picked up after preprocessing. The single comparison judges whether it is accurate. If the verification is correct, the shipment will be made, otherwise an alarm will be issued and manual intervention will be prompted. The results of normal outgoing or manual intervention will be reported to the business information platform for filing by the outgoing port client, and the back-end database will be automatically updated, and the product inventory records of the corresponding warehouse and location will be deducted.
3. Secondary warehouse management
For secondary warehouses such as direct-operated stores, corresponding fixed or hand-held readers can be equipped according to the size of the goods, the inbound and outbound clients (can be on the same computer) are deployed, and business processes such as warehouse transfer or terminal sales can be added. Implement a similar business process model.
4. Inventory work process
The RFID warehouse management platform system can automatically carry out warehouse inventory and location statistics, and automatically compare the back-end database when the inventory data is saved, and generate difference statistical information that is displayed on the terminal in real time, providing verification for inventory personnel. After the inventory is completed, the inventory difference report is automatically generated in the background for printing and verification.
3. System architecture diagram
The RFID electronic label management system includes: access to the server/in/out client/handheld terminal and communication network, as shown in the figure below:
The access server is responsible for real-time communication and data interaction with many clients. It is deployed in CS mode and includes RFID tag protocol processing middleware. It is responsible for parsing a large number of concurrent tag information and incorporating it into the database. Real-time information such as alarms should also be carried out with the corresponding business system. Real-time data interaction;
The warehousing client includes RFID reader access middleware, which is responsible for processing concurrent massive RFID tag information, filtering and screening valid data, anti-collision processing, and automatic comparison with order or delivery document information, and automatically issuing when it does not match Call the police. Pack and compress the tag information that needs to be uploaded, etc., and also provide manual intervention interactive interface;
The handheld terminal can be manually operated to collect information about a single piece of cargo, and can compare and alarm in real time. The collected information can be sent to the background system via WIFI or GPRS network, or it can be temporarily stored and forwarded.
[ad_2]