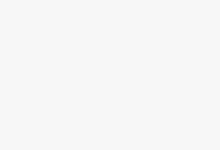
RFID mold lean production management system
[ad_1]
1. Background
Mould is the basic technological equipment of industrial production and is called “Mother of Industry”. 75% of rough-processed industrial product parts and 50% of precision-processed parts are formed by molds, and most plastic products are also formed by molds. As a basic industry of the national economy, molds involve machinery, automobiles, light industry, electronics, chemicals, metallurgy, building materials and other industries, with a wide range of applications. Since 2000, my country’s mold industry has entered a period of rapid development, but at the same time, mold is a traditional, complex, and competitive industry. The company is an order-oriented one-piece production enterprise. Almost every set of molds The production of orders is the development of a new product, which requires the analysis of customer intent to determine the mold structure, quotation, design, material preparation, manufacturing, assembly, trial mold, repeated mold repair and other processes, until the mold can be processed to a qualified product. At present, mold companies generally have such difficulties:
Each mold is a set of brand new products, and there are many uncontrollable factors in the production process. How to control these factors;
In the actual production workshop, for a large mold company, there may be nearly a hundred molds processed and manufactured at the same time. How to effectively manage hundreds of parts during the processing process;
With the increasingly fierce market competition, the delivery time required by customers is getting shorter and shorter, and the processing accuracy is also getting higher and higher;
How to realize timely material distribution in the production process of mold enterprises;
How to effectively develop a production plan.
How to dynamically monitor the production status of workpieces during the production process and be able to record their operating status information has become one of the keys to the lean production of mold companies.
2. Technical introduction
RFID radio frequency identification technology can accurately and automatically identify and track the information of each product produced by the factory by transmitting and storing data without human intervention. Compared with traditional data collection methods, RFID technology can delete and write tag information repeatedly, with long-distance operation and one-to-many reading, miniaturization, good signal penetration and strong anti-fouling, The high storage capacity and other characteristics enable lean production in the mold workshop to be realized.
3 System scheme design
Lean management of RFID mold production refers to deploying RFID readers and RFID tags in the mold production workshop, establishing a node network for material tracking, and defining the process or quality parameters of these production target nodes, and collecting parameters according to batches and modules. Analyze the relevance of process or quality parameters to support the material tracking process of the whole plant.
The entire system uses advanced RFID automatic collection technology to obtain real-time production data, inventory data, quality inspection data and mobile data of each node on the site. Through the collection, sorting and analysis of all production parameter measurement information in the production workshop, the material production process is improved The data collection and entry of the involved production units, equipment, and warehouse instruments provide reliable assurance for various production activities to provide material movement, processing, inventory and equipment, management assistance decision-making and workshop cost accounting.
Figure 1 System network diagram
The RFID mold production workshop can realize the automatic collection of all or part of the production data, real-time monitoring of production conditions, online adjustment and optimization of operating parameters and other production operation management and monitoring functions. It is the prerequisite for high-efficiency production and management and is the data of the enterprise production management system. origin of.
3.1 Data Entry System
Data is the basis of the entire system. Before the material block is machined, the system assigns a unique ID number to the material block according to a unified coding rule. After this ID number is written into the RFID electronic label through a dedicated data entry system, the RFID The electronic tag is bound to the material block, and through this ID number, the tracking and management of the entire production and processing cycle of the material block can be realized.
At the same time, the background system imports the processing data, drawings, processing procedures, tools, electrodes, spark positions and other information of the material block to each machining center, waiting for the processing of the material block.
Figure 2 Electronic tags and materials to be processed
3.2 Station acquisition system
The processing center installs an RFID data collection terminal on each processing equipment. After the processed material block is transferred to the station, the data collection terminal reads the ID number on the material block, and accesses the system background database through the ID number to obtain the material block For the processing data at this station, the processing equipment starts to process the material block until the processing is completed, and then flows to the next station.
Figure 3 Mould processing station
After the material block is processed, the system will allocate the material block into the measurement center. The measurement station is also equipped with a data acquisition terminal to read the electronic tag of the material block, and obtain the measurement point and accuracy of the material block through the ID number, and complete the processing of the material. For block measurement, qualified products enter the warehouse, and unqualified products are recorded in the system and processed manually by quality personnel.
The mold production management system using RFID technology enables real-time and accurate collection of mold data during the entire production and processing process, and promotes the production of mold workshops in accordance with the process route step by step, division of labor, and planned production, realizing real-time monitoring of the production workshop , Provide scientific decision-making for product statistics and production plan arrangement, greatly improve the production efficiency of enterprises, thereby bringing new competitiveness to enterprises.
4. RFID equipment selection
Lean mold production workshops have higher requirements for data collection terminals. The entire workshop is in an industrial environment, which requires that the RFID equipment collection terminal must be able to adapt to the industrial environment and maintain stable and accurate reading performance in such an environment. At the same time, as a data collection terminal, it should have good compatibility and easy integration when used in conjunction with other automation equipment at the workstation.
As the world’s leading RFID equipment supplier, ThingMagic, while providing excellent RFID equipment to customers around the world, is also committed to creating a product that can help customers better integrate and apply RFID technology simply and quickly. ThingMagic module is such a product: high performance, industrial design, exquisite and easy to use, instruction set operation can also be better integrated with other automation equipment.
[ad_2]