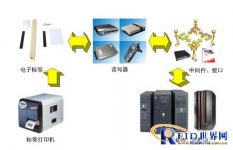
RFID data collection solution for Shanghai Shijia coating production line
[ad_1]
I. Introduction
Radio Frequency Identification (RFID), commonly known as electronic tags, is widely used in fields such as assets, personnel, production lines, and supply chains. Radio frequency identification is a non-contact automatic identification technology. It automatically identifies target objects and obtains relevant data through radio frequency signals. The identification work does not require manual intervention and can work in various harsh environments. UHF RFID technology can identify high-speed moving objects from a long distance, and can identify multiple tags at the same time, which is quick and convenient to operate. The most basic RFID system consists of three parts: Tag: consists of coupling elements and chips, each tag has a unique electronic code, attached to the object to identify the target; reader (Reader): read (sometimes also The device that can write tag information can be designed as a handheld or fixed type; Antenna: Transmit radio frequency signals between the tag and the reader. The basic RFID system composition is shown in Figure 1.
Figure 1. Composition diagram of RFID system
willRadio Frequency IdentificationCompared with barcode technology, radio frequency identification has many advantages, such as long distance of identification, no need for visual visibility of labels during identification, use in harsh environments, update of content, ability to read multiple labels in batches, and identifiable High-speed moving objects, large amount of information, not easy to imitate, etc.
Radio frequency identification technology is considered to be one of the most promising information technologies in the 21st century. In terms of current technological development, the RFID field is at the forefront of the development of the Internet of Things and is also one of the basic technologies for the realization of the Internet of Things.
2. Project background
In traditional manufacturing companies, management mainly focuses on product management, quality management, warehouse management, mobile asset management, on-site personnel management, fleet management, etc. Usually, the collection of production line information adopts manual collection and manual input. The accuracy of manual collection and manual input is insufficient, and there is a certain error rate. Manual input can only be done at regular intervals, resulting in the production plan being submitted on a weekly or monthly basis, which cannot be accurate to the day. The production data in the system cannot be updated in real time, and the lag is serious, which is not conducive to the smooth progress of the production flow and restricts the further increase of production capacity. At the same time, most functional departments of manufacturing companies use paper and pens, which makes most functional departments of manufacturing companies face a large number of data errors and reduces productivity.
Companies have long been aware of the existence of these problems and have tried their best to solve them. In my country, some manufacturing enterprises use barcode recognition or manual input to input data, but barcode recognition or manual input still brings a series of problems:
A. Different efficiency of workers can easily cause uneven division of labor in the team;
B. Production abnormalities and production line bottlenecks cannot be found in real time;
C. The labor efficiency is low, and the actual working time utilization rate is not high;
D. Manual input of information is prone to errors;
E. Real-time tracking is not possible, and it is difficult for the management to arrange work according to the work status. If there is a problem in a certain process of the work process, it must wait until the next day if it is to be eliminated;
F. Manual or bar code data collection requires a special team of personnel to operate. Calculated on a 1000-person factory, the salary of three statistical employees is about RMB 4,500, and RMB 54,000 a year, which requires a lot of labor costs;
G. The consumption of bills paper and printers every month is a huge and invisible account. Calculated on a 1000-person factory, printer maintenance and paper supplies are 8,000 yuan per month, and 96,000 yuan a year.
In the manufacturing industry, compared with the widely used manual or bar code technology, RFID tags have essential advantages. The advantages of RFID tags include: wireless long-distance reading and writing, penetrating reading and writing, and high speed Read and write in a mobile state, store more data, and can be used in harsh environments. Therefore, RFID technology is not just a simple replacement of bar code technology, its application in the manufacturing industry will change the production and operation of enterprises. At present, RFID technology has begun to be applied to supply chain management, warehouse management, and material management in the manufacturing industry. The on-site environment of the coating line is harsh, with high temperature and humidity, and paint pollution. Common identification methods cannot meet the requirements of use. Shanghai Shijia proposes a management plan for RFID electronic tags based on the customer’s on-site conditions.
3. Scheme design
3.1 Scheme design
According to the actual situation of the painting line of a certain factory, it uses a suspension chain system to move the workpieces in different processes of the production line, and uses beams and hooks to grab the workpieces to realize the entire process from inputting raw materials to processing finished products. It mainly involves electrostatic dust removal, preheating, primer spraying, drying, surface spraying, leveling and drying, etc. The UHF is used to identify data in each link, and wireless Wi-Fi and management systems are used for communication; hardware The network topology is as follows:
3.2 Process design
The workflow is described as follows:
Labeling: SR-3200B is used to initialize the electronic label data; after initialization, the label is attached to the beam or hook and reused;
Initialization of the online label; before the physical object to be processed is online, the physical information and electronic label information are read and associated through the smart mobile terminal to complete the correspondence between the label and the physical object;
Real-time identification of labels in each process: install a fixed type in each processReaderAnd the antenna, identify the physical objects that have passed the process, and record the time in the database background; monitor the production progress and quality of the production line in real time;
3.3 System implementation benefits
Production enterprises introduce RFID, combine RFID with existing manufacturing information systems such as MES, ERP, etc., establish a real-time management system for production lines, optimize and rationally use resources, increase production capacity, increase asset utilization, and higher-level Quality control and various online measurements create greater benefits for enterprises.
A. Impact on real-time data flow
RFID can provide a continuously updated real-time data stream. Complementing the manufacturing execution system, the information provided by RFID can be used to ensure the correct use of labor, machines, tools, and components, thereby achieving paperless production and reducing downtime. Furthermore, when materials, parts and assemblies pass through the production line, the production process can be controlled, modified and even reorganized in real time to ensure reliability and high quality. All data is collected by the client computer at high speed via wireless means.
B. Impact on real-time supervision of production lines
With real-time data flow as the basis, management systems such as ERP can mine these large amounts of data, conduct real-time and effective supervision of production schedules and processes, identify production bottlenecks, solve production problems, and deploy higher-level quality control and Various online measurements.
C. Impact on the actual production capacity of the production line
RFID can provide the most accurate calculation results of the man-hours required for the process. ERP software can accurately evaluate each worker’s process and working hours through RFID, and calculate the actual production capacity of each production line. Enterprise managers can use these data to make more accurate analysis of the company’s business capabilities.
D. Impact on the balance production line
Complete data mining and analysis. Enterprise managers can master workshop production capacity, solve production bottlenecks in real time, monitor production progress in real time, and improve production processes through quality monitoring. RFID provides the basis for enterprises to achieve a balanced production line, and is compatible with enterprise ERP, SCM, MCS, etc. The combination of mainstream management systems allows every employee in the company to play the best role. The effective working time of the production line is increased by 15%, and the output is increased by 10%; supply chain costs are reduced by 30%, inventory is reduced by 25%, and sales are increased by 10%.
Impact on production quality
Complete the data collection of the production line, reduce the labor intensity, realize the orderly progress of the workpieces, and ensure the high quality of the products. At the same time, the problematic workpieces can be traced and analyzed to achieve the goal of improving production quality.
Four, equipment configuration
The equipment configuration list is as follows:
Serial number name model quantity remarks
1 Card issuing machine SR-3200B 1 Card issuing
2 Fixed reader SR-2514 8 Wifi communication, reading in each process
3 RF cable assembly SCA-SMA/NJ-3 8
4 RFID antenna SA-915-VL9 8
5 Smart mobile terminal SP-2414-2A 1 with RFID function, at the production line
6 Smart mobile terminal SP-2414-2A 1 Without RFID function, production line buffer area
7 Electronic label model 1 400 Choose one of 7 and 8
8 Electronic label model 2 400 7 or 8
5. Introduction of main equipment
Label selection one
product description:
This product is a passive UHF high temperature resistant metal tag. The product is resistant to high temperature, small in size, low in price, cost-effective, sturdy and durable, and can be used in harsh environments such as high temperature. It is widely used in mold management, product asset management and other applications that require high temperature environments.
Product parameters:
Substrate: Ceramic
Antenna: Silver printing
Product size: 21*17*2mm
Test distance: fixed reader 2m (30dBm)
Handheld 1m (28dBm)
The test distance varies according to the environment and antenna gain
Label chip: Impinj M3 (If customers have special requirements, different chips can be used)
Protocol: EPC Class1Gen2 (ISO18000-6C)
Frequency: 902^928MHz
Operating temperature: -40~250℃
Installation method: Adhesive 3M9473PC (-40~250℃)
Shell: PPA
Protection level: IP68
Electrostatic protection: 2000V
Memory capacity (as shown below): EPC 96Bits; TID 32Bits
Erasable times: 100000 times
Product advantages:
High temperature resistance, the instantaneous temperature resistance of the product monomer can reach 250℃, and the normal temperature resistance can reach 200℃
Label selection two
product description:
This product is a passive UHF anti-metal tag. The product is small in size, low in price, cost-effective, sturdy and durable, and can be used in harsh environments.Widely used in mold management, product asset management, etc.
Product parameters:
Substrate: Ceramic
Antenna: Silver printing
Product size: 30*30*3.0mm
Test distance: fixed reader 5m-8M
Handheld machine 3m-4m
The test distance varies according to the environment and antenna gain
Label chip: Alien H3 (if customers have special requirements, different chips can be used)
Protocol: EPC Class1Gen2 (ISO18000-6C)
Frequency: 902^928MHz
Operating temperature: -40~250℃
Installation method: -40~250℃
Protection level: IP68
Electrostatic protection: 2000V
Memory capacity: EPC 96Bits; TID 32Bits; User 512Bits
Data storage time: 50 years
Erasable times: 100000 times
[ad_2]