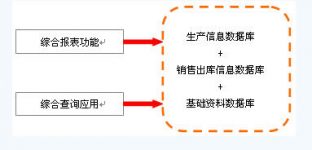
Barcode solutions for the apparel industry
[ad_1]
In the increasingly fierce competition in the apparel market, it is not enough to focus solely on the company itself. Only by meeting the needs and needs of customers better than competitors can companies have a unique competitive advantage. If an enterprise wants to establish a defensive marketing strategy by improving customer satisfaction, and thereby increase the company’s profitability, it must have a long-term advantage in price, fabric, workmanship, design, and advertising. As a clothing company specializing in the production of cashmere products, a company in Shanghai pays attention to the color consistency of the same batch of products in the production process to achieve quality perfection.
Relying on the senior experience in bar code application fields such as production site information collection, product serial number management, and the advantage of providing one-stop service of bar code printing and collection equipment, the development of clothing enterprise production management information system helps the company realize batch management modernization , And realize the function of rapid automatic data collection and management, which lays a good foundation for subsequent sales and management of anti-crossing goods.
Production management industry solutions
1. Raw material batch management
Because the raw material used in a company’s production is cashmere, this type of product is characterized by different batches of products even if they are of the same color, there are still color differences, so the company requires that the raw material batches of similar clothes on the same order must be consistent. The number of fabric pieces of clothing that can be produced by a winding yarn can be roughly controlled. Therefore, the number of yarns used in similar clothes on an order can also be roughly controlled. When there is a surplus of yarn, the company hopes that the system can control it. Make a decision to match the remaining amount with the customer’s order.
2. Single product production process control
The company’s senior management can observe the work process of the workshop through the system, which can be detailed to the fluidity of a single product.
Solution overview: The system reserves expandable modules for system upgrades.
Raw material storage: including raw material winding and packing list.
Production planning department: When the production planning department receives a sales order, first enter the order into the material arrangement table in the system, use this form to adjust the inventory and its batch number information, when there is a matching batch of yarn inventory , Directly fill in the production process sheet to identify the raw material yarn used. When the inventory cannot match the current order, a supplier purchase order is directly generated, and the specific specifications of the yarn required are filled in the order.
Yarn warehouse management department: Workers go to the warehouse to pick up the materials after receiving the production process sheet. According to the bar code of the raw yarn and the bar code on the production process sheet, the warehouse tube scans the physical object and the label for comparison. If the picking is correct, it will be recorded in the system. If an alarm occurs for picking errors, the batch number label must be attached to the winding yarn received by the worker. –Production Management
Workers in the production workshop: After each piece of clothing is produced, paste the woven piece label contained in the batch number label on the woven piece.
Garment packaging department: After the semi-finished garment is completed, the worker uses the scanner to scan the barcode of each piece. If the scanned barcode meets the conditions of a batch, the system controls the printer to print a wash label/tag barcode serial number according to the scanned barcode. This serial number is sewn on the garment as the identity ID of the garment. After the finished product is sold, the company can use this ID to detect the raw material batch used in the garment and other related information. If the scanned bar code shows that the raw materials used on the garment are not in the same batch, the system will give an alarm and check which piece is faulty.
Introduction to Production Management Function Module
1.1 User Management
Define three management objects of system special group/user group/user.
1.2 Password management
Perform maintenance operations such as password setting/modification on a user basis.
1.3 Rights Management
Set access rights for system functions by group/user object.
2 Basic data maintenance module
2.1 Supplier Information Management
Management of supplier name, address, contact person, and checkout date.
2.2 Customer Information Management
Management of customer name, address, contact person, and checkout date.
2.3 Commodity data management
Management of product (yarn) name, model and price.
2.4 Management of auxiliary information such as production shifts/employees/workshops
3 Yarn warehouse management module
3.1 Generation of raw material warehousing list
When the raw material yarn is in the warehouse, the warehouse management personnel will check the raw material winding and packing list and enter this information into the raw material warehouse list in the system.
3.2 Barcode label generation
4 Production planning control module Production management
4.1 Entry of Material Arrangement Sheet
When the production planning department receives a sales order, the sales order information is entered into the system, and the system generates a material schedule.
4.2 Production process sheet
When the system matches the existing stock in the warehouse with the raw materials required by the sales order, it automatically generates a production process sheet.
4.3 Inventory comparison module
According to the material schedule, the production planning department compares the required raw materials with the existing raw materials in the warehouse. When there is a matching inventory of the same batch, the staff control system prints out the “production process sheet”. When the inventory does not match, The staff can control the system to print out the purchase order of raw materials according to the situation, and then send the production process list to the corresponding processing workers.
4.4 Inventory management
The manager can check the inventory situation through the system at any time, and print the inventory report.
5 On-site information comparison module
Workers use the production process sheet to pick up the yarn from the yarn warehouse. When the warehouse receives the production process sheet, take out the yarn through the relevant information of the production process sheet, and then scan the barcodes of the raw materials and the production process sheet through the system, and compare them. Whether the picking is correct, if it is correct, distribute the yarn (including the winding label and the sheet label) to the workers. If there is a batch error, the system will alarm.
6 Production control module
Weaving sheet production production management
In the garment production process, the worker sticks the label on the coil of the weaving panel to the weaving panel every time a woven panel is produced.
Semi-finished garment production
After the semi-finished garment is produced, the semi-finished garment is handed over to the inspection staff, who use the scanner to scan the barcode of each fabric piece. If the same color is used in the same batch of barcodes, the finished garment will be qualified; if the same color For barcodes that are not in the same batch, the system will give an alarm and be reworked.
Approval treatment of ready-made garments
If the garment produced by the worker is qualified, after the worker scans the barcode of each weaving piece, the worker controls the printer to print a garment label (washed label) and sew it on the garment. This barcode is used as the garment ID to uniquely identify the garment.
Back yarn management
When the worker returns the unused yarn to the warehouse, the warehouse manager enters the yarn into the system and records basic information such as the remaining quantity of the yarn.
7 Barcode reader interface module
1) Barcode products are adopted across the line to achieve seamless integration of software and hardware.
2) Use the hardware’s own instruction set for control, which is efficient and direct.
3) The bar code reader is connected to the PC to realize the collection of the serial number of the finished product at the time of shipment.
8 Barcode printer interface module
The barcode printer actually performs the label printing task.Production management
9 Query statistics module (The system can query basic data including: weaving piece information, clothing information, raw material yarn information, etc. according to the garment serial number.)
System flow structure
[ad_2]