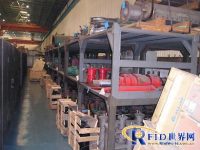
Barcode application solutions for the steel industry
[ad_1]
Each bundle of wire rods is registered and the barcode technology is used in steel ERP. After a well-known large-scale steel company in China implemented ERP, before the logistics had implemented the barcode management system, there were repeated product measurement, product removal, and shipping. A series of drawbacks such as slow manual input of data and error-prone, confusing identification and error-prone varieties. After the barcode system is implemented, the weight of the coil is automatically collected from the process scale by the barcode system. Coil uses barcode to identify batch number, inventory code, serial number (hook number) and other information. The management of the product is more detailed, the system manages each coil of wire and each storage location, and effectively uses the limited storage resources; the operation is more standardized, and the program-controlled loading is replaced by manual loading, which avoids loading the wrong vehicle. The process is more simplified, and the measurement is reduced from three to one, which reduces the waiting time and related procedures of customers, which greatly facilitates customers; at the same time, it realizes the effective tracking of out-of-the-box products and improves customer satisfaction.
solution
Receipt and delivery of many steel and heavy industries is a difficult problem to solve. With the help of barcode technology, effective barcode solutions can be established. The bar code card can be used to realize the functions of entering the factory, picking up on site, measuring, quality inspection, leaving the factory, and querying. Finally, it will be built into a scalable sales business barcode management system with complete functions, advanced technology, and simple management.
1. Product storage
① After the product is offline, it is measured by the craft scale.
② The bar code system automatically collects the coil weight.
③ The measurement staff selects the current batch information, and the system generates complete standard information from the coil weight and batch information. And send this information to the bar code printer, print out the bar code number, and transmit the data to the ERP system to increase inventory in time.
④ After printing, the barcode is peeled off by the barcode stripping machine, and the measurement personnel will post the barcode on the iron plate and list it.
2. Issuing cards
① Make or order a batch of barcode cards through the card-making mechanism.
② Each customer can subscribe for multiple cards.
③ Issue or lock the card by judging the customer balance.
④ Through the bar code card, all the shipping orders of the customer can be retrieved.
3.Car into the factory
① Scan the bar code with a credit card machine.
② Query and display the shipping note made for the vehicle. If there is one, check whether the vehicle number is consistent. And confirm, and tell the delivery customer to the delivery yard.
③ The barcode system will automatically mark the entry mark and entry time on the shipping note. (In order to easily check whether the car has entered the factory)
4.Yard Pickup
① At the entrance of the cargo yard, the customer scans the bar code card and prints out the information to be picked up (that is, the delivery note of the vehicle).
② The cargo yard personnel will carry out loading according to the delivery information.
③ When loading, use the scanning terminal to scan the items one by one, transfer the scanned data to the shipping note once and generate the sales outbound slip, save the signature, confirm the outbound, and reduce the inventory in time.
5. Quality Inspection
① At the place where the quality certificate is issued, the customer scans the multi-barcode card to find out the sales slip of the car, and print out the quality certificate of the car based on this number.
② The quality certificate shall be in duplicate, one copy shall be signed by the customer and kept for future reference, and the other shall be used by the customer.
6. Go out (door guard)
① The customer holds a barcode card and quality certificate.
② The customer swipes the card, and queries the vehicle’s sales outbound slip through the vehicle number, and verifies whether it is consistent with the actual product. Determine whether to release.
Main module
1. The electronic scale data reading module is produced offline to weigh a single coil of wire, and automatically import the data into the completion order provided by the ERP system.
2. The barcode generation and printing module establishes a barcode information table, and the barcode is associated with the completed work order number, including information such as specifications, batch number, weight, etc. (specific investigations to determine all necessary related information). Due to the establishment of the association, the definition of the barcode may be meaningless. The barcode is generated by the system according to the encoding rules (the encoding rules we recommend to use the CODE 128 encoding method);
Use printer programming language to complete automatic label printing.
1. Warehousing data collection module This module uses a bar code collector to perform bar code management on the goods, which has great advantages, avoids manual input, reduces the chance of error, and is convenient and flexible to use. The module is mainly divided into the following modules:
1. Goods warehousing; (data collection)
2. Goods out of the warehouse; (data collection)
3. Goods moving to warehouse; (data collection)
4. Warehouse inventory; (data collection)
[ad_2]