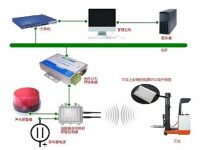
RFID large factory warehouse workshop forklift positioning management system
[ad_1]
1. System significance
With the continuous development and growth of enterprises, the types of materials in warehouses are constantly increasing, and the importance of forklifts in the warehouse is increasing, and forklifts enter and exit the warehouse more and more frequently. In this way, the rational use and overall planning of forklifts are very important. It’s important. At present, the complexity and diversity of warehouse management have made the traditional operation mode of relying on manual and paper inventory records completely incapable of such a huge task. In order to solve the current passive situation of relying on manual dispatch of forklifts, such as low efficiency, insufficient coordination and reasonable deployment, and insufficient dispatch speed, our company proposes a set of “Warehouse forklift positioning and dispatching management system based on RFID technology” program, relying on advanced technology, Free up the labor force, improve the work efficiency of workers, increase the profit of the enterprise, and enhance the image of the enterprise.
2. System architecture and program description
RFID large-scale factory warehouse forklift positioning and dispatching management system is based on Shanghai Hongyan Internet of Things Technology Co., Ltd. according to the current needs of many large-scale factory forklift positioning management and overall scheduling. It uses the most advanced radio frequency identification technology, sensor technology, and A security system developed based on monitoring technology, communication technology, and RTLS real-time positioning technology. The system has the characteristics of real-time positioning of the forklift’s position and working status, overall scheduling of forklift work, and checking the activity trajectory of a certain forklift in a specified time period at any time to judge the forklift’s work efficiency and reasonable dispatching conditions.
Our company designed the system according to the following principles:
1) Adaptability: To meet and meet the requirements of existing business management, network organization and service quality, we consider the status quo of the enterprise and the status quo of modern logistics management.
2) Flexibility: The system flexibly adjusts the business process and organizational structure according to the development of the enterprise.
3) High reliability and stability: As the RFID management system supported by enterprise warehouse operation and management, the stability, reliability and accuracy of this system are very important. The use of RFID technology and computer network technology is to improve dispatch management capabilities. The selection, configuration, installation, and computer network deployment of RFID equipment can quickly and stably collect and transmit on-site information to the system management center for analysis and dispatch management.
4) Advancement: adopt the most advanced international RFID technology, sensor technology, computer network technology, communication technology, RTLS real-time positioning technology.
5) Openness: Adopt a unified platform, a unified RFID data interface, a unified data dictionary and data structure mode.
6) Maintainability: The system’s standard interface design and modular design make maintenance simple and convenient.
7) Ease of operation: a unified and friendly interface and a complete operation manual make the operation easy to use.
2.1 System architecture

Figure 1 System network architecture
2.2 Program description
We will install a semi-active RFID low-frequency activation electronic tag (model: TY-T602A or TY-T603A) developed and produced by Tangyuan Company on each forklift that needs positioning monitoring. The tag has a unique code. , Each tag is initially bound to the forklift. The tag usually sleeps and does not send a signal to the outside world. Only when it is within the trigger signal range and is awakened by the low-frequency activation locator, will it send a signal to the outside world; secondly, we are in the warehouse entrance and main A low-frequency activation locator (model: TY-A201A) is installed in the aisle to wake up the tag and locate the location of the tag. The distance to wake up the tag is 0.5-8 meters; at the same time, install some active RFID long-distance reading in different places of the warehouse Writer (Model: TY-R301A), used to collect the information sent out after the low-frequency activation electronic tag is activated (including the ID number of the electronic tag itself, the address code of the low-frequency activation antenna, the signal strength RSSI value and the tag battery power status light information ). After the reader/writer collects the data, it uploads the information to the computer management center through various transmission methods. The management center has a set of software systems that we specialize in warehouse forklift positioning and scheduling management, which will analyze and process various data. Storage, judgment, etc., so as to complete the entire warehouse forklift positioning scheduling management system functions.

Figure 2 Schematic diagram of positioning
2.3 System function introduction
1) Monitoring of forklift entering and exiting warehouse:
Install a set of low-frequency activator and long-distance reader at each entrance of the warehouse. The activator has 2 antennas, No. 1 and No. 2, which are placed inside and outside the door, so that they can be monitored anytime and anywhere. The movement of forklifts in and out of the warehouse, including time, location, detailed information about forklifts, etc.
2) Staff attendance management:
At the same time, an electronic label can also be issued to the relevant staff, which can be used to monitor staff attendance and activity trajectory, and control the flow of personnel at any time.
3) Issue tasks:
When the administrator issues a task, he can open the issue task page, enter the corresponding task information, designate the relevant person in charge and the completion time and progress, click Submit the task, and the task is issued.
4) Forklift warehouse positioning:
Through this system, the approximate position of each forklift can be located at any time, which can be accurate to a position of 5 meters around, and the working and dispatching conditions of each forklift can be controlled at any time.
5) Forklift cross-border and sabotage judgment:
Some areas in the warehouse are restricted by forklifts. The system can identify the areas where the forklifts are reasonably running. Normally working forklifts usually move back and forth. If a forklift is found to be stationary in one place for a long time, The system will issue a reminder to determine whether to take a rest and slow down on the spot.
6) Historical data query:
Every task is completed, the system has a record. The location of each forklift can be controlled by the system at any time, and relevant data can be retrieved and inquired at any time.
[ad_2]