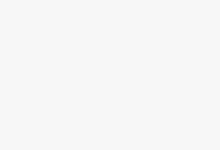
Application of M-7018 in temperature collection of blow molding hollow molding machine
[ad_1]
The blow molding machine adopts the working principle of “extrusion blow molding”. Granular or powdered plastics are plasticized by the extruder to a molten state and enter the die. When the material storage of the die reaches a predetermined value, the die of the die opens, and the electrical control system adjusts according to the set parison wall thickness curve. The gap between the die and the core mold is controlled by 64-point parison wall thickness. At the same time, the injection cylinder pushes out the molten material to form a product parison. After the mold is closed, compressed air is blown in until the plastic is blown into the mold shape and shaped into a hollow product. After cooling and shaping, the mold is opened, and the product is taken out by the robot, and then the product is demolded and trimmed to obtain the required hollow product.
This article mainly introduces the use of ICP DAS M-7000 acquisition module to realize the temperature acquisition in the blow molding machine.
One system introduction
Plastic blow molding is one of the most common molding methods for thermoplastic products. During molding, the semi-molten tube (parison) obtained by extrusion or injection molding is first placed in a blow mold of a certain shape, and then compressed air is blown into the tube to inflate it, and then it is cooled and shaped After demolding, a hollow plastic product is obtained. The equipment used for this molding method is called a plastic blow molding hollow molding machine.
The rapid development of hollow products is due to their relatively simple molding process, high production efficiency and high product quality. At present, the development of hollow molding methods and equipment at home and abroad is very fast, and the proportion of plastic raw materials in the total raw materials of molded products by this method is also increasing, about nearly 20%. There are many plastic raw materials that can be used for blow molding hollow products, such as polyethylene, polyvinyl chloride, polypropylene, polystyrene, linear polyester, polycarbonate, and some engineering plastics.
As there are many methods of plastic blow molding hollow molding, there are also many classification methods. The currently widely used plastic blow molding hollow molding methods can be divided into two categories: extrusion blow molding and injection blow molding. The corresponding molding equipment is extrusion blow molding hollow molding machine and injection blow molding hollow molding machine. kind. The main difference between the two is the molding of the parison. The former uses extrusion and the latter uses injection. Developed on the basis of these two molding methods are: extrusion-stretch-blow molding hollow molding (referred to as extrusion blow molding) and injection-stretch-blow molding (referred to as injection stretch blow molding) and multi-layer blow molding Molding, asymmetric hollow blow molding and other molding methods. And multi-layer blow molding has methods such as co-extrusion blow molding and co-injection blow molding.
In practical applications, the extrusion blow molding method is more common, has many types, and develops rapidly. The injection blow molding is becoming more and more popular nowadays because of its special advantages. Various specifications of injection blowing or injection stretch blowing equipment have also been continuously developed.
Two system requirements
■ Precise temperature control of storage bins, machine heads, molds, etc., so that plastic raw materials can be plasticized (that is, melted) and formed at an appropriate temperature.
■ Control the pressure and speed when the plastic is injected, so that the thickness of the plastic can be better controlled.
■ The timing of the actions of each mechanism is coordinated.
■ On-site HMI sets various process parameters, including temperature, pressure, speed, etc.
Three difficult factors
■ Temperature collection and control are particularly important in the entire equipment.
■ If the temperature control instrument is used for control, the target value of the control temperature needs to be set separately on each temperature control instrument, and the temperature feedback of each control point also needs to be observed on each temperature control instrument. The production of different products requires different settings. When the product is changed, the formula cannot be called to quickly change the parameters, which is very inconvenient to operate.
■ If the PLC temperature control module is used for control, although the above problems can be avoided, the number of control channels per module is small, only 2 or 4; the cost of the module is expensive, which is not conducive to system expansion and more detailed temperature control.
Four M-7018 module solution for temperature collection
On the basis of existing technology, PLC communicates with M-7018 module through RS-485 network
(1) Hardware part:
Adopt M-7018 thermocouple input module, each module has 8 channels, can collect 8 channels of temperature signals at the same time, the collection rate of 10Hz can meet the temperature control speed with PLC. 16-bit resolution, high temperature resolution accuracy, easy to achieve fine temperature acquisition and control, and produce more different types of products; 8 channels can increase the number of temperature control loops, which is convenient for more detailed temperature control; With cold junction compensation, no additional configuration is required.
M-7018: 8-channel analog quantity/thermocouple input module
Main features of M-7018:
■ Resolution: 16 bits
■ Analog input: thermocouple, mV, V or mA
■ Input range: +/-15mV, +/-50mV, +/-100mV, +/-500mV, +/-1V, +/-2.5V,+/-20mA
■ Thermocouple type: J, K, T, E, R, S, B, N, C
■ Sampling frequency: 10Hz
■ With burnout detection function
■ With Modbus communication protocol and DCON
■M7018Z: 10 channels and each channel can be individually configured, supporting 240V overvoltage protection.
(2) Software part:
PLC communicates with M-7018, through Modbus protocol, it is convenient to read the temperature signal detected by M-7018, unified into PLC for integrated control.
in conclusion:
Solution for temperature collection using M-7018 module:
■ It can avoid all the inconveniences caused by the use of temperature control instruments to control the temperature, and improve the grade and humanization of the product.
■ It can avoid the disadvantages of high price and fewer control channels caused by the use of temperature control modules for temperature control; more control loops can be expanded to achieve more detailed control.
■ Strong anti-interference ability, stable operation in harsh industrial environment, using this program to produce more than 700 equipment every year, which greatly saves money and improves the humanization of equipment.
[ad_2]