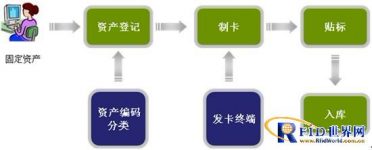
Fixed asset RIFD label management system
[ad_1]
1. System overview
“Fixed Assets” based on Internet of Things technologyRFID“Tag Management System” is aimed at the often-occurring inconsistencies between the physical objects and the accounts in the management of fixed assets. It adopts advanced and mature RFID technology to give each physical object a unique “asset holographic ID card” RFID tag, so as to achieve the realization of the fixed asset physical object. Tracking management is carried out in the whole process of the enterprise. It solves the common phenomenon of inconsistency of accounts, cards, and objects, improves the accuracy of asset inventory, and provides rich and powerful management functions to help customers achieve the full-scale, accurate and detailed, timely and dynamic fixed asset management requirements.
“Fixed Assets RFID Tag Management System” includes asset addition, change, scrap, damage, depreciation, distribution, use department change, management personnel setting, asset exchange between departments, batch transfer, RFID label generation, various report printing, Combination of queries, etc. For each fixed asset, you can check out all the information of the asset from purchase, storage, put into use, use department, depreciation, and even withdrawal from use. The dynamic query function can ensure that managers have comprehensive information at the first time, and the batch depreciation of assets can reduce a large amount of repetitive labor and ensure the accuracy of data. Automatic report preparation and printing are fast and accurate, saving a lot of time for manual preparation of reports.
“Fixed Assets RFID Tag Management System” centralizes the previously dispersed management information and combines them into an information platform with overall fixed asset management functions.
2. System composition
“Fixed Assets RFID Tag Management System” is characterized by physical management, using a computer as an operating platform, and a handheld RFID information analysis terminal and RIFD desktop card issuing terminal as auxiliary tools to form a complete physical asset management system. It is a management system with advantages of “fast”, “precision” and comprehensive functions.
The system contains:
Hardware part: handheld RFID information analysis terminal, RIFD desktop card issuing terminal, RFID electronic label, system management server.
Software part: Fixed asset RFID tag management software.
Three, system management process
After the relevant data of each newly purchased asset is entered into the computer, an RFID label will be automatically generated by the RFID desktop card issuing terminal. The content of the label can be set by the user, including the name of the fixed asset, the date of purchase, and the custody (using department) And other content. Putting labels on the physical objects of fixed assets not only clearly distinguishes the use sectors of fixed assets, but also brings great convenience to the inventory. Inventory personnel do not need to record the asset code and check the account book to carry out the inventory, only through a special handheld The RFID information analysis terminal reads the tags on the fixed assets, and the tag information is automatically stored in the RFID information analysis terminal. The handheld terminal is battery-powered and does not need to be connected by wires. The inventory staff can easily carry it to any place for mutual verification, and the read information is stored in the terminal. Nearly 50,000 fixed asset codes can be stored in the terminal, which increases the inventory speed by more than 90%, and at the same time avoids repeated inventory or wrong inventory. After reading the tag, connect the terminal to the computer through the computer to quickly obtain the actual situation of the asset. Through the combination query, the asset shortage, surplus and other changes can be found immediately.
Fourth, the system structure
4.1 System network structure
4.2 System function structure
Five, system characteristics
5.1 Use asset storage as a starting point to track and manage assets
In the past, physical management was based on financial management, from invoices to financials, and began to manage physical objects after the financial entered the account. However, with the development of society and the transformation of corporate procurement methods, it often happens that the physical objects are already in use but have not been recorded in the financial accounts for the time being. It causes lag in physical management and brings inconvenience to management.
“Fixed Assets RFID Tag Management System” divides “physical storage” and “financial accounting” into two management links. As long as the physical storage is in storage, the physical object can be managed throughout the process. Eliminate the lag in physical management.
5.2 Eliminate the blind spots of physical management in the past
First of all, in the past process of physical management of fixed assets, when the financial assets withdraw from the book, they are regarded as the physical objects of the assets. Even if the assets still have use value, they cannot be systematically managed. Secondly, since low-value consumables and consumables are all written off in the current month, the physical management in this area is almost blank. But as companies pay more attention to the optimal allocation of resources, and to improve the utilization of resources. The original physical management model has obviously not kept up with the management requirements of the enterprise.
The “Fixed Assets RFID Tag Management System” not only manages the entire process of low-value consumables that were almost ignored, but also divides the original asset withdrawal into two parts, “physical withdrawal” and “book withdrawal”, so that the book value can be checked. Withdrawal, but there are real objects of use value for management, eliminating the blind spots of physical management. In order to improve the utilization rate of resources, optimize the reasonable allocation of resources.
5.3 Strengthen the detailed management of the whole process of physical objects
Before using the software, the bank did not have a set of physical object management software to realize the full-process detailed management of the physical objects, resulting in the inability to track and manage the physical objects, which brought a lot of regrets to the physical management.
After using the “Fixed Assets RFID Tag Management System”, the detailed management of the changes, borrowing, maintenance, and overhaul of the physical objects, as well as the personalized management of specific assets, truly realize the full-process and detailed three-dimensional management of the physical objects.
5.4 Meet the real-time and dynamic management of the sub-branches
Due to the differences in the physical management process between branches and head offices, branches cannot fully use the centralized management mode of physical objects of head offices. In particular, the physical fixed assets purchased in a centralized manner are directly delivered to the place of use, and the branch offices cannot understand the actual situation of the fixed assets in a timely manner, which brings inconvenience to management. Secondly, if the computer equipment of many road sub-branches undergoes emergency repairs, the physical changes of fixed assets will be quite large, and they will only be discovered during the annual physical inventory. In this way, in the process of physical management, it is impossible to understand the true situation of the data in time, and it is impossible to provide a scientific basis for decision-making.
“Fixed Assets RFID Tag Management System” can be implemented by the following means:
? With the branch agency as the system center, the branch is the node for data collection and physical management, and provides a data query mode for the branch to meet the distributed management requirements of other branches for physical objects.
? RFID information collection technology is widely used in branch offices and sub-branches. Use the RFID information analysis terminal to perform on-site operation and confirmation of the transfer, maintenance, withdrawal, and emergency repair of equipment including branches (a combination of equipment transfer and maintenance), and send it back to the system for automatic batch processing. This can provide managers with real-time dynamic data and ensure the authenticity and validity of the data.
5.5 Reduce the work intensity of operators, improve work efficiency, and ensure the authenticity and reliability of data
Due to the widespread use of RFID field collection and operation technology, the intensity of work required to operate on the system in the past has been changed.
For example, when a branch is relocated, in the past, it was necessary to manually go to the relocation location for manual statistics, and then go to the relocation location to manually count and confirm the moved objects, and then return to the system to perform data operations after confirmation. In this way, the work efficiency of the administrator is low and error-prone.
“Fixed Assets RFID Tag Management System” adopts the technology of RFID information analysis terminal for confirmation and operation. The administrator only needs to take the wireless handheld RFID information analysis terminal to the move-out location, set the terminal to be transferred out, and scan the moved out one by one. , You can realize the transfer of physical objects. Go to the move-in location, set the analysis terminal as transfer-in, scan the imported objects one by one, and then realize the transfer-in work of the objects. After scanning, transfer the data from the handheld terminal to the computer, and the system will automatically perform the batch processing of the physical transfer and generate a list of physical transfers. This not only reduces the work intensity of the administrator, but also the data is accurate and reliable.
When equipment repairs occur, this method can also be used to realize automatic data processing. This not only reduces the work intensity of the administrator, improves work efficiency, but also ensures the authenticity and reliability of the data.
5.6 Greatly save inventory time and improve inventory efficiency
In the traditional model, the inventory work is done entirely by hand, which requires a lot of manpower, material resources and time. The error rate of inventory is relatively large, and the inventory benefit is not high. After using this software, the inventory is automated. You only need to scan the tags through the wireless handheld RFID information analysis terminal to store the asset information in it, and then the terminal will import the asset inventory information into the software, and the financial system Perform automatic verification and generate various asset inventory to the table. It greatly saves inventory manpower, material resources and time, has a low error rate, reduces inventory costs, and significantly improves asset inventory efficiency.
5.7 Automatic reminder when maintenance and inspection are due, equipment management is simplified and simplified
In the past, it was extremely easy to make mistakes only by manually remembering the maintenance cycle, which brought unnecessary trouble to the timely inspection and maintenance of equipment, and easily caused loopholes in equipment management. The equipment management module of “Fixed Assets RFID Tag Management System” records in detail the maintenance time of various equipment, specific maintenance conditions, maintenance inspection cycle, next maintenance inspection time, etc. The software will automatically perform maintenance inspection when it is due. Reminders provide a strong guarantee for timely delivery of equipment for inspection.
Six, system function
“Fixed Assets RFID Tag Management System” includes asset addition, change, scrapping, damage, depreciation, distribution and use department, use department change, management personnel setting, asset exchange between departments, batch transfer, RFID tag generation, allocation, and withdrawal , Assets operation, borrowing, requisition situation, various report printing, combination query, etc. For each fixed asset, you can check out all the information of the asset from purchase, storage, put into use, use department, depreciation, and even withdrawal from use. The dynamic query function can ensure that managers have comprehensive information at the first time, and the batch depreciation of assets can reduce a large amount of repetitive labor and ensure the accuracy of data. Automatic report preparation and printing are fast and accurate, which can save a lot of time for manual preparation of reports. The fixed asset RFID management system integrates fixed asset management, low-value consumables management, and equipment management. The original scattered management information is concentrated and combined into a management platform with overall functions. It is easy to realize “account = card = The management of “materials” provides a powerful guarantee for enterprises to efficiently manage their physical assets.
“Fixed Assets RFID Tag Management System” has the following main functions:
1. Daily asset management functions
It mainly includes daily work such as the addition, modification, withdrawal, transfer, deletion, splitting, and allocation of fixed assets, the operation, borrowing, and use of assets, and calculating depreciation rate and residual value rate.
2. Generate RFID tag function
According to the selected fixed assets, the RFID tags attached to the physical objects of the fixed assets are automatically generated.
? Provides the function of custom RFID encoding;
? Provides the function of customizing the generated content;
3. System features
? Provides the management function of main assets and attached assets;
? Provide the function of single and batch adding physical information, with the ability to copy and automatically split assets;
? Provides the function of single and batch transfer of physical information, and provides a wireless handheld RFID information analysis terminal to confirm single/batch transfer and manual transfer;
? Provides dynamic query functions, including rich queries such as in-use assets, expired assets, operating conditions, historical assets, and exit assets;
? Provides the function of customizing dynamic query templates;
? Provides the function of exporting dynamic query results into Excel or text;
? Provides a wealth of statistical report functions, including a specified time period and a summary table of asset details of any unit department, etc.;
? Provides the function of customizing the company name when displaying and printing reports in the asset card;
? Provides data backup and recovery functions.
4. Equipment maintenance, annual inspection, measurement management
? Provide asset maintenance management functions;
? Provide maintenance asset reminder function;
? Provide asset annual inspection, measurement and inspection management functions;
? Provide asset annual inspection, measurement and inspection plan functions.
5. Asset utilization efficiency analysis and management
? Used quantity, used percentage of total quantity;
? Unused quantity, unused percentage of total quantity;
? The number of idle assets, the percentage of idle assets to the total number;
? The number of intact assets, the percentage of intact assets to the total number;
? The number of damaged assets and the percentage of damaged assets to the total number;
? The number of maintenance assets and the percentage of maintenance assets to the total number;
? The number of repaired assets and the percentage of repaired assets to the number of repaired assets;
? The number of unrepaired assets and the percentage of repaired assets to the number of repaired assets;
? The number of assets under repair and the percentage of assets under repair to the number of assets under repair;
? The number of repairs for a single asset and the total amount of repairs.
6. Depreciation management
? Provides an average life depreciation method for assets;
7. Financial Management
? Realize the physical asset management function of multiple units and sets of accounts;
? Provide system and financial data automatic reconciliation function (optional).
8. Data interface
? Provide data import function, including data legality check and delete the import function once after import;
? Provide system data export function;
? Provides the function of data docking with other systems (optional).
9. Inventory
? Provides the function of custom physical verification methods (check by department, custodian, and storage location);
? Provide the function of on-site transfer of physical assets;
? Provides the function of confirming the status of physical assets;
? Query normal inventory information, query abnormal inventory information, query transferred inventory information, query transferred information, and query uncounted information;
? Provides data downloading and data uploading functions;
? Provides a single/all delete counting result function.
10. System maintenance function
? The system administrator will make the asset classification code table, exit method code table, purchase method code table, storage place code table, department code table, custodian table, and unit name table. Perform operations such as adding, modifying, and deleting.
? Provide the operator with the function of modifying his own password.
The system administrator can freely set the operation authority of each subordinate operator for the function
? Provide the function of automatic or manual backup of the data of the unit or department.
11. Security management function
? Provide various security management methods.
? Password management function: Maintain account numbers and passwords.
? Authority control function: divide users into different levels to determine the user’s authority to use the system, and determine different operations according to different authority.
? Data encryption function: encrypt important data.
12. Remote communication function
Provide error-free remote communication to achieve accurate data transmission through the intranet or dedicated line.
Seven, system configuration
The system software and hardware need to be configured according to the user’s actual situation (such as the number of fixed assets, organization, and actual environment).
[ad_2]