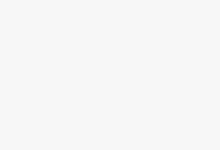
Kenmax RFID flat power pipeline mobile inspection application
[ad_1]
1. Program introduction
Overhead transmission and distribution lines are widely distributed and exposed to outdoor work for a long time. Not only do they have to bear their own electrical and mechanical loads, but they also have to be affected by various external factors and the erosion of the natural environment. In the long run, it will promote the aging, oxidation and corrosion of line facilities, resulting in line failures and failure to work normally.
Recently, Kenmax has developed and producedRFIDTablet terminal, specially used for mobile inspection of power pipelines. This tablet terminal has a built-in GPS/Beidou dual-mode positioning function, which solves the difficult problems of the original automatic identification technology and meets the business needs of power system customers for pipeline inspection.
2. System characteristics

. Accuracy: the administrator PC will transfer the description file of the line and its equipment to the RFID tablet terminal (you can do it when you update the data of the line)
. Security: identification of inspectors.Only when the inspector enters his user name and password to verify his identity, can he send the inspection results recorded on the tablet to the server
Standardization: Use the RFID tablet terminal to inspect each line one by one, and use the geographic location information displayed by GPS to automatically call out the geographic location information that meets the obtained information, and automatically call out the pole that meets the information. Ask the inspector to fill in the inspection objects one by one and record the abnormal situation.
. Fast transferability: After completing the inspection, the inspector puts the RFID tablet terminal on the base of the management machine, and the system automatically transmits the inspection result to the management machine database. The management opportunity centrally processes the inspection data passed by the inspectors to generate detailed inspection records and equipment defect data, and forward the data to other computer management systems (such as MIS, OA, etc.) as needed.
3. Core functions:

The mobile power pipeline inspection solution uses a variety of convenient technologies to arm the Kenmax RFID tablet terminal as an intelligent terminal for power inspection. It solves the problems of inability to accept supervision during traditional manual inspection operations, irregular inspections, and low degree of informatization of inspection data, which is of great significance for building smart grids and promoting safe production in the power industry. The core functions are as follows:
1. System login (tablet terminal): According to customer needs, the exclusive Android operating system is specially customized for the power inspection terminal, including the boot screen, the default wallpaper, etc.; the Android4.1 user interface is deeply customized to realize the customization of the standard power inspection terminal .
Multiple patrol personnel login → patrol cycle reminder → select substation → select patrol type
2. Pre-inspection preparation work (tablet terminal): Built-in pre-inspection preparation application APP, including job task description, preparation work confirmation, dangerous points and control measures, defect reminders, inspection route view, inspection tool collection, etc. Links to ensure the safety of inspection equipment.
Work task description→Preparation work confirmationPreparation work confirmation→Dangerous points and measures control
Defect reminder→inspection route view
3. Equipment inspection (tablet terminal): Use the professional RFID card reader function of industrial-grade RFID tablet computers to quickly scan RFID tag information, and cooperate with the professional development kit SDK to carry out in-depth integration of mobile inspection APP and record the defects of the equipment. Grade, mark the key defect as a key concern.
The equipment inspected by RFID scanning identification technology ensures that inspectors arrive at the designated inspection location; the defect level of the recording equipment (general, serious, crisis), and the mark that does not reach the defect level is the focus.
4. Equipment defect data management (back-end): The back-end directly generates inspection reports, and supports Excel spreadsheet export and printing.
5. Statistical analysis of equipment operation (back-end): According to the statistics of previous inspection records, equipment operation curves are generated, and multiple query methods such as time period and equipment are supported.
[ad_2]