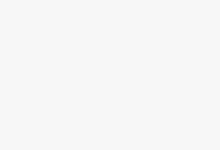
RFID application scheme of Volkswagen plant in Germany
[ad_1]
Volkswagen is the largest car manufacturer in Europe and the fourth largest car manufacturer in the world. On June 1, 2000, the Volkswagen Factory Amusement Park (Auto City) held a grand screening. This unique amusement park allows customers to choose their vehicles and see new trends in the automotive industry. There are more than 10,000 cars for display and for customers to choose. All these vehicles must be prepared to be transported. This means washing, vacuum packaging, cleaning treatment, and a comprehensive quality control. After all the work was completed, the car was used in the 48-meter-high glass tower for transportation. Volkswagen wants to have a device that can quickly locate production line cars, and use this device to monitor the entire production process of the car and track its delivery process. This device must process all the work in the shortest time possible, and it must not cause confusion when each car is confirmed.
620)this.style.width=620;” border=0>
solution
By using RFID technology, this solution has optimized the workflow of delivering the produced cars to customers. All tasks involved in the transportation process are stored in an RFID tag temporarily attached to the vehicle. Every time a vehicle passes through the RFID processing station, the worker immediately knows its location and its current state automatically.
620)this.style.width=620;” border=0>
System workflow
Open—–Parking—–Car Washing—–Temporary Storage——Car Factory Registration——Transportation
When a car leaves the production area, an electronic delivery list containing the vehicle identifier and pre-delivery tasks is written on the label. The tag was placed on the rearview mirror, and the car drove to a dedicated parking lot.
The car is then taken to an ILR-controlled cleaning station; the entry and exit status of this area is automatically detected, and its status is automatically updated on the label.
In the next step, the car carries an ILR control storage device; the facility is automatically detected after entering, and its status is automatically updated on the label.
When the car is ready to be sent out, it is taken to an ILR controlled gate where the wheelbase of the car can be read from the label. Using this information, the tracker on the transportation platform is automatically adjusted and the gate is opened. Then the ILR control platform is automatically activated and the car is transported to the car tower.
When a customer came to pick up his car, the tag was removed and used again.
advantage:
Reduce vehicle delivery time by quickly locating the target vehicle-when many vehicles are delivered at the same time, one worker can significantly save four times the time.
After the delivery task is completed, the efficiency of the delivery process is improved by automatically creating an electronic delivery list for each car and automatically updating its status.
620)this.style.width=620;” border=0>
Improve the efficiency of repetitive work-after the work is completed, the electronic instrument will automatically track the parts that need to be repaired or upgraded. During the transportation of the vehicle, the real-time tracking of the car is used to improve the quality of the car. The management ensures that the car is delivered accurately and accurately every time In the hands of the corresponding customers to improve the quality of customer service technology:
ILR hardware components include a data carrier: i-Q8 tag, read/write device: i-PORT, antenna and ILR control handle terminal (HHT). Data collection software can be seamlessly connected with existing enterprise application software.
Tagged cars Tagged cars, i-PORT, data collection, data integration.
For details, please contact our company. Phone: +86 (10) 62029007
This article is the author’s original submission. The copyright of the article belongs to the author. If you want to reprint it, you must obtain the author’s consent. thanks!
[ad_2]