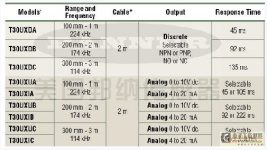
Application of an ultrasonic sensor in the escalator industry
[ad_1]
Foreword:
With the increasing degree of social automation, people are more inclined to choose more transportation tools. Therefore, escalators that replace stairs between the upper and lower corridors are more and more widely used, including subways, airports, stores, hotels, crossing tunnels and pedestrians. Occasions such as flyovers. The previous ordinary escalator had no detection device, and it was impossible to determine whether someone was riding. The escalator kept running continuously, which caused a lot of waste of energy. With the country’s vigorous efforts to promote energy-saving requirements, it has gradually been unable to meet the requirements of the owners. Therefore, frequency conversion elevators have emerged. The biggest feature of this type of elevator is that it will detect the approach of people at the entrance, and it will be normal when people are detected. Speed, and when no one is in a slow or stopped state, in order to achieve energy-saving effect. Therefore, a sensor device that can reliably determine whether the human body is approaching or not is very important.
Banner Corporation is a world-renowned sensor manufacturer in the United States. Its products can be widely used in various automation equipment around the world, covering ports, printing, logistics, packaging, electronics, rail transportation and other industries. Its excellent performance makes its products adapt to the environment of different places on the earth. It has become the No. 1 sensor manufacturer in North America and the No. 2 sensor manufacturer in the world.
For detection devices in the escalator industry, Banner’s solution recommends an ultrasonic sensor product designed for the escalator field-Banner T30UX ultrasonic sensor. This ultrasonic sensor series is an expansion product of Banner’s T30U ultrasonic sensor series. The new T30UX ultrasonic sensor has a T-shaped compact structure, is resistant to electromagnetic and radio frequency interference, has a smaller blind area and a longer detection distance, and its wide range of operation The temperature and built-in temperature compensation circuit make it applicable to various harsh industrial field environments. Its excellent performance parameters are enough to make users no longer have to worry about any mistakes in this link. The following is a detailed introduction to the installation and use instructions and debugging methods of this product on the escalator.
Features of this product:
1. Ultrasonic detection in a fixed area, only sensitive to distance, can reliably detect objects in various colors (including black) in the area, and shield objects outside the area to avoid misjudgment.
2. The detection distance can be set by pressing the button, and the circuit can be automatically identified and judged, and it can be completed by pressing the button 3 times.
3. Operating temperature: -40°C to 70°C, and built-in temperature compensation circuit to reduce the influence of temperature gradient changes on sensor measurement.
4. The maximum detection distance is 1, 2, 3 meters, and the switch and analog models are optional.
5. Large range operation, divergence angle up to 30 degrees, reliable coverage of effective parts of the human body, small blind spots, minimum distance of 100mm.
6. Not affected by dust and rain, the MTBF time can reach 100,000 hours.
7. Enhanced EMC and RFI, strong anti-interference; IP67 protection level, anti-shock and anti-vibration.
8. Transmitting and receiving integrated design, no need to install additional controller, cylindrical thread with a diameter of 30, installation and debugging is more convenient.
9. Key lock and indicator light function; remote control Teach-in teaching function, and there is a flow chart to guide the operation.
The working principle of T30UX ultrasonic sensor:
Install an ultrasonic sensor T30UX under the handrail on each side of the escalator entrance and exit, use the transmitted ultrasonic wave to shine on the human body, and receive the reflected sound wave, and then send an NPN/PNP or relay after detecting the passenger at the entrance of the escalator Signal. So as to provide accurate operating instructions for the escalator actuator (motor drive system) to run when there are passengers, and switch to an energy-saving state when there are no passengers:
Take the standard escalator with a nominal power of 11.7KW as an example. Running speed Power consumption
Full speed no-load state 0.5 m/s 3.2KW
Low-speed energy-saving state 0.2 m/s 1.1KW
Out of service energy-saving state 0 m/s 0 KW
In order to ensure that every passenger coming from different directions can be detected, the installation position of the sensor needs to be towards the inside of the escalator, so that the two ultrasonic waves can converge, and a detection zone without blind spots is formed in front of the entrance of the escalator. Through the button adjustment on the back of the T30UX, the sensing range can be set, and an isosceles triangle shaped detection beam area will be generated. Once a pedestrian walks towards the entrance of the escalator, as shown in Figure 1, it can be sensed by sound waves.
Generally, the country stipulates that the minimum distance for escalator entrance detection is 1.3 meters (that is, the straight-line distance from the elevator steps to the passengers). This solution selects the ultrasonic range of 2 meters model. Figure 2 is a simple installation diagram:
Among them, X is the distance from the sensor to the passenger, and Y is the effective part of the passenger detection.
Assuming that the detection distance of the ultrasonic sensor is currently set to 1.5 meters (that is, to shield objects beyond 1.5 meters), and at the same time, take into account that passengers enter the elevator entrance from the side. At this time, the distance between the passengers and the sensor is only 30mm.
So set the value range of X: 1.5m>X>0.3m, the transmitter angle of the sensor is 30 degrees, Y=X * tan30, the same amplitude range of Y can be calculated: 0.87m>Y>0.17m, that is to the human body Because the ultrasonic sensor can reliably detect dark objects, and the trousers and shoes of passengers are usually dark, the parts that could not be reliably detected by photoelectric sensors in the past can be completely detected by ultrasonic sensors. solved.
On-site installation operation process and precautions:
1. According to the structure size of the escalator, open a 25mm diameter round hole and fix it, no additional mounting brackets are required.
2. Make sure that there is no obstructing object in front of the sensor. It is recommended that the distance between the ultrasonic probe (ceramic pressure piece) and the opening of the mechanism is 3-5mm.
3. Adjust and install the signal power wiring (standard 2 meters long) to avoid damage to the ceramic sheet and the connecting wire.
4. The detection distance can be set by pressing the key three times according to the steps of the manual. It is recommended to set the maximum distance of 1.5m and the minimum distance of 30mm.
5. During installation, the elevation angle can be adjusted upwards by 15-20 degrees and tilted inwards by 10-15 degrees according to the specific environment. For details, see the angle description in Figure 1 and Figure 2.
6. After the on-site installation is completed, it can be remotely debugged offline, which is convenient for maintenance personnel to operate. For details, see the remote teaching function in the manual.
The above data is for reference only, and the specific design dimensions of the bracket are determined according to different ladder types.
Banner’s second-generation ultrasonic sensor T30UX technical parameters and dimensions:
T30UX product parameter table
Summarize:
The application of ultrasonic sensors in industry and civilian use is rapidly developing. This once very expensive and low-precision technology has now become simple and easy to use, with high accuracy and low cost. Nowadays, ultrasonic sensors have become a conventional device to improve product quality in process control, and are used in detecting defective products, confirming appearance or disappearance, and other fields. This sensor can also increase productivity, it can reduce waste and avoid downtime due to damaged parts. In the future, the development of such products in this technical field will continue this trend. This is a challenge. A consensus has been reached in the industrial field that ultrasonic sensors are not only used in all manufacturing fields (including quality control, Process control and testing), and has great development potential in a considerable part of civilian equipment.
Attachment: Key points of ultrasonic sensor selection:
1. Range and size
The size of the detected object will affect the maximum effective range of the ultrasonic sensor. The sensor must detect a certain level of sound waves to be excited and output signals. A larger object can reflect most of the sound waves to the sensor, so the sensor can be in its This object can be sensed to the maximum extent, and a small object can only reflect very few sound waves, which significantly reduces the range of sensing.
2. Measured object
The most ideal object that can be detected by an ultrasonic sensor should be a large, flat, high-density object, which is placed vertically facing the sensing surface of the sensor. The most difficult to detect are those that are very small in area, or are made of materials that can absorb sound waves, such as foamed plastic, or are obliquely facing the sensor. Some objects that are more difficult to be detected can be taught on the background surface of the object first, and then react to the object placed between the sensor and the background. When used for liquid measurement, the surface of the liquid needs to face the ultrasonic sensor vertically. If the surface of the liquid is very uneven, the response time of the sensor should be adjusted longer. It will average these changes, which can be read more fixedly. Pick.
Using the ultrasonic sensor in Retrosonic mode makes it possible to detect irregular objects. In retrosonic mode, the ultrasonic sensor can first detect a flat background, such as a wall. When any object passes between the sensor and the wall, it will obstruct With sound waves, the sensor senses the interruption, and then realizes that there is an object.
3. Vibration
Whether it is the vibration of the sensor itself or the surrounding machinery, it will affect the accuracy of the distance measurement. At this time, you can consider taking some shock absorption measures, such as using rubber anti-vibration equipment as a base for the sensor to reduce vibration, or use a fixed rod. Eliminate or minimize vibration.
4. Attenuation
When the ambient temperature changes slowly, the temperature-compensated ultrasonic sensor can make adjustments, but if the temperature changes too fast, the sensor will not be able to make adjustments.
5. Misjudgment
Sound waves may be reflected by some nearby objects, such as guide rails or fixed fixtures. In order to ensure the reliability of detection, the influence of surrounding objects on the reflection of sound waves must be reduced or eliminated. In order to avoid false detection of surrounding objects, many ultrasonic sensors have a The LED indicator is used to guide the operator to install to ensure that the sensor is installed correctly and reduce the risk of error.
[ad_2]