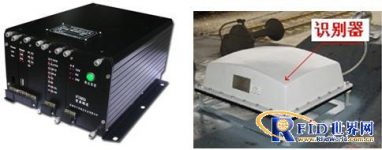
RFID-based automatic phase passing system scheme for electric locomotives
[ad_1]
1. System background
The GFX-3A automatic phase separation system for electric locomotives was jointly developed by Shenzhen Fengteruida Industrial Company and Beijing Railway Bureau. It passed the technical review and appraisal of the Science and Technology Department of the Ministry of Railways and the Transportation Bureau on July 18, 2007. The system is an automatic over-phase control product developed for electric locomotives. Its main function is to automatically and smoothly reduce the traction current according to the locomotive speed and position of the locomotive when the electric locomotive passes through the phase-separation zone. “After passing through the phase separation zone, the main circuit breaker is automatically closed, the auxiliary units are closed, and the traction current is controlled to rise smoothly, realizing the automation of the operation when the electric locomotive passes through the phase separation zone, and greatly reducing the work intensity of the flight attendants.
2. System composition:
The dual CPU hot backup structure of the system improves the reliability of the system. The main control system has the function of self-checking and early warning and the function of event record storage and analysis.
At the same time, it recognizes the positioning signal of the radio frequency card on the Internet and is compatible with the ground magnetic positioning signal. The dual technology multiple positioning signal realizes the accurate and reliable automatic phase separation of the electric locomotive.
The automatic phase separation device for trams and locomotives includes two parts: the vehicle-mounted device part and the positioning device along the line. The vehicle-mounted part includes: vehicle-mounted control host, roof RFID reader, alarm (buzzer, two-color LED), magnetic induction receiver and connecting cables; positioning devices along the line include: contact network radio frequency positioning card and magnetic induction device (magnetic Sleepers).
1. Positioning device along the line (one-way one phase separation)
RF positioning card: 6 sets
Magnetic sensor (magnetic pillow): 4 sets
2. Roof RFID reader
The roof reader is installed on the I end of the car roof, and its function is to receive the information of the radio frequency positioning card on the Internet, and the reader will transmit the received radio frequency card positioning information to the host.
3. Alarm and on/off switch
The alarm and the on/off switch are designed as an integral part (also can be installed separately), installed on the front panel of the driver’s console, used for automatic over-phase alarm, sound and light display, and input/cut device.
4. Vehicle Magnetic Induction Receiver
The on-board magnetic induction receiver is installed on the bogie of the locomotive. The receiver adopts a sealed, waterproof and shockproof design to ensure the reliable operation of the system. The vehicle-mounted magnetic induction receiver is based on the principle of electromagnetic induction, and the induction receiving coil is combined with the magnetic field of the ground sensor to complete the positioning and recognition of the system.
3. Installation diagram of split-phase positioning point
The device is based on the dual positioning technology of the online radio frequency card positioning and the ground magnet signal to locate the locomotive position automatically. Locomotive position identification is mainly based on online radio frequency card positioning, and ground magnet signals play a backup and supervisory role. Three radio frequency card positioning points and two magnet positioning points are set in front of each phase separation zone, and the anti-phase positioning points are set equally. As shown below:
Note: 1, T1, T2, T3, T4 are the positions of the ground magnetic sensor, T1 and T4 are the notice points; T2 and T3 are the forced points
2. K1~K6 are the online radio frequency positioning cards installed on the load-bearing cables, and the positions are defined as follows:
Upward direction: K6-6# (announcement card), K1-1# (unloading card), K2-2# (sub-main card breaking)
Downward direction: K5-5# (announcement card), K3-3# (unloading card), K4-4# (dividing main break card)
Four, working principle
When the locomotive runs to K6, it reads the notice card signal, and the buzzer buzzes to remind the driver that there is still 2Km away from the phase separation, and the meter starts before the phase separation; when the locomotive runs to K1, it reads the 1# unloading card, Start to calculate the distance according to the position of 1# card at 575m. When the locomotive runs to K2, it will read the 2# sub-main broken card, and start to calculate the distance according to the position of 2# card at 275m, and according to the current locomotive speed, send an unloading signal to start the flow reduction, when the locomotive When the current drops to “0”, the main break signal is issued.
When the T1 or T2 magnet signal is recognized, if the 1# or 2# card has been recognized before, the magnet splitting main trip meter will not be activated, and the radio frequency card will still be used to split the main trip meter.
If the radio frequency card signal is not recognized, it will encounter the T1 magnet signal and start the 205m division main trip meter of the T1 magnet. If T1 is not encountered, when T2 is encountered, the forced main break is performed.
When the locomotive passes the no-power zone, one of the following conditions will send the main switch-on signal to control the main switch-off of the locomotive:
Detecting the signal change of the grid voltage signal from scratch;
Recognize the magnet recovery signal or reverse radio frequency card signal;
After passing the no-power zone, the meter is closed and the main trip is made.
The principle of automatic phase passing in reverse driving is the same as that in forward driving, because the positioning points of each phase are installed completely symmetrically.
The device is a vehicle-mounted automatic phase separation control device based on the combination of radio frequency positioning technology (RFID), magnetic induction technology and locomotive “kilometer mark” data (TAX2 box public information) positioning method.
When the locomotive is running in the section, the distance between the locomotive and the next phase point in front is calculated and calibrated based on the kilometer scale data and combined with the current locomotive speed. The kilometer standard data is used for location backup and fault diagnosis to ensure the safety and reliability of the locomotive’s automatic phase separation.
5. Working Principles
System design principles
Under the automatic control of the device, the first three radio frequency card positioning points and the two magnetic sensor positioning points for manual phase separation are mutually correlated and verified to ensure the reliability of the excessive phase separation. Even if the individual positioning points fail, the normal automatic phase separation will not be affected. If the device fails, the alarm will display a red light, and the buzzer will sound to remind the driver to cut off the automatic excessive phase. As long as the operation end switch is turned to the cut position, the device and the locomotive control system are completely cut off, and the switch/cut switch is only connected to the operation end. Regarding, the non-operating end throw/cut switch will not affect any position.
The main control system has a complete self-check function. When the device is normal, the alarm will display a green light, and the driver can automatically pass the phase through the switch/cut switch.
The main control system has a complete event storage function, and all the operation records and related fault information of the automatic phase separation are all recorded in the memory, which is convenient for downloading and analyzing.
Anti-misoperation, the device judges the running position of the locomotive in combination with the kilometer mark data. When the locomotive is running in the section, even if the magnetic signal is induced due to interference, the main control system will not issue an output control.
The unloading/loading locomotive traction current signal adopts a 2-level linear slope mode, which is suitable for various operating conditions of the locomotive (zero position, traction, electric system).
Six, technical characteristics
1) Locomotive positioning technology
Locomotive position positioning introduces radio frequency positioning card (RFID) technology, its characteristics:
Simple structure, small size, easy installation, maintenance-free, and adapt to harsh working environment.
Unique ID serial number, there will be no misidentification.
Installed on the load-bearing cable of the catenary along the line to prevent man-made damage.
2) Radio frequency identification technology is compatible with geomagnetic signals and combined with kilometer mark positioning technology to improve the accuracy of locomotive position positioning.
3) The core dual CPU hot backup structure improves the average trouble-free operation cycle of the equipment.
4) Calculate and output the best switch-off position to reduce locomotive speed loss.
5) Slope current control technology solves the problem of excessive phase splitting impulse of locomotive.
6) It has a complete fault self-check and alarm prompt function.
7) Modular design, simple structure, convenient installation and maintenance.
8) Redundant design, convenient for function expansion.
Solution Provider: Shenzhen Fengtai Ruida Industrial Co., Ltd.
http://www.sz-rfid.com
[ad_2]