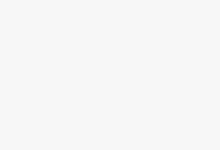
Shanghai Ditong launches RFID production line and barcode radio frequency automatic identification management system solution
[ad_1]
Overview:
With the rapid development of China’s economy and the continuous improvement of people’s living standards, automobiles have gradually become a consumption hotspot. Domestic automobile production has expanded rapidly, and foreign automobile production giants have also entered the Chinese market. For China’s auto industry, while ushering in unprecedented opportunities for development, it must also face fierce market competition, especially after China’s entry into the WTO, barriers will be gradually broken and competition will gradually become international.
Faced with such market competition, the auto industry will face tremendous pressure to survive, and must improve production efficiency, improve product quality, reduce costs, and meet the diverse and individual needs of customers. The Chinese automobile industry has a clear gap with the international automobile market in terms of management level, manufacturing capacity, quality and price. It is a new market characterized by the continuous shortening of product life cycles, increasingly personalized customer needs, and higher and higher quality requirements. The situation also poses new challenges to the Chinese auto industry.
At the same time, as a consumer product with relatively high safety requirements, the quality of automobiles has attracted the attention of consumers, government management departments and automobile manufacturers. For every automobile manufacturer, an effective information system must be established for Establish and keep long-term information about each car and owner, dynamic information in the process of technical services, and regularly file with relevant departments. In order to fulfill the obligations stipulated by the recall system, automobile manufacturers must set up relevant institutions, corresponding personnel, and configure corresponding systems.
Based on the above situation, facing the fierce and changeable market competition environment and the requirements of relevant regulations and standards, the automobile manufacturing industry must improve the level of production and quality management, and establish a complete and integrated production quality monitoring and management system.
The self-developed automobile production quality management system provides comprehensive production and quality management of products, covering incoming material management, engine processing and assembly, stamping, welding, painting, final assembly, inspection and testing, audit, after-sales service, product traceability, etc., and It can realize information interaction with ERP, CRM and other management systems.
Press shop management
The stamping workshop is a typical batch production organization method. According to the production demand of the welding workshop and the production capacity of the stamping equipment, the stamping parts are divided into multiple batches, and the production depends on the rapid cutting of the mold. The main features are: diversity of parts and components; production repeatability and production rotation. Therefore, production batch management is the focus of management in the stamping shop.
Machine shop management
The engine processing workshop mainly produces five core engine components: cylinder block, cylinder head, crankshaft, connecting rod, and camshaft, which is an assembly line production mode. The focus of the control is the key quality characteristics of each component, and the production batch is managed at the same time.
Use the cylinder block as the basic carrier to assemble the engine parts into an engine assembly, including the main assembly, preparation area, and inspection links. The focus of control is assembly accuracy, torque, test results and defects in the assembly process. Key components such as chains, generators, and starters are tracked in batches.
Welding shop management
The sub-assemblies of the welding workshop include side panels, front and rear panels, bottom panels, etc., which are assembled together, and then the roof and four doors and two covers are welded to form the body-in-white and sent to the painting workshop. The main quality control points of the welding workshop For welding defects and precision. The 2mm project is a symbol of high-quality bodywork. The defective car body will be repaired in the rework area.
Spray shop management
The main control points of the painting workshop are the process parameters of the equipment and the defects of the car body. The typical process flow includes pretreatment, electrophoresis, electrophoresis polishing, coarse sealing, bottom sealing, fine sealing, intermediate coating, intermediate coating polishing, surface coating, and finishing. And final quality inspection.
Assembly shop management
The final assembly shop is the final production link of the entire automobile, and is the most important part of ensuring the quality and production schedule of the car. The MES system final assembly shop includes sub-assembly assembly and main assembly and other technological processes. There are more than 100 processes in total, the focus of control It is the defects that occur in the assembly process, assembling torque, filling amount/filling parameters, etc. At the same time, the association of important parts, safety parts and automobile VIN codes is established, and the automobile genealogy is established.
Principles of the plan
Establish a unified central database on the site of the enterprise workshop as an information platform for the circulation of goods to facilitate overall standardized management. In the industrial link, RFID technology is used to assign an identification number (ID) to each work-in-progress component, which is the name of the component in the information network. Through the RFID technology of the MES system, the production status and inventory status are mapped to the information network. Registered in the field center database, and transmitted to the information system (such as ERP, MRP), etc.
basic structure
The system adopts the B/S three-tier architecture design, the presentation layer: the interactive interface between the user and the software, the middle layer: the application server and the proxy server, responsible for the system business logic processing, and the data layer: the database. Centralized storage of system data. It can be a variety of relational databases;
The MES system is based on typical RFID automatic identification technology and consists of the following parts: data carrier, read/write unit and interface module. The interface module is connected to PLC, PC and other control units by bus or serial communication.
Work Order Management
Work order management is used to decompose and refine the production plan/order, set the order number, product model, customer, quantity, batch number, BOM to which the work order belongs, specified production line, planned start time, planned end time, specified process route and various Process operation specifications and control items, stipulate calibration, traceability, and stop-line standards. Support split, merge, suspend, resume, cancel, etc.
Job scheduling
The basic production unit determines the production schedule according to the production schedule, and at the same time determines the tasks of each process, operator, and work shift. Its task is to arrange multiple tasks on the limited manpower and equipment resources, specify the execution sequence and time, provide reliable customer order delivery dates, and achieve and optimize the predetermined goals.
Error prevention management
The MES system uses radio frequency technology on the assembly line to produce as many customized cars as possible. It is produced based on the requirements of the user. The user can select the color of the car from tens of thousands of internal and external options. , Engine model and tire style, etc. As a result, the automobile assembly line has to assemble hundreds of styles of cars. Without a highly organized and complex control system, it is difficult to complete such a complex task. Equipped with an RFID system on the assembly line, using reusable radio frequency tags, the radio frequency tags can carry all the requirements required by the car in detail, and there are readers at each work point, which can ensure that the car is The assembly task can be completed without error at each assembly line position.
Warehouse management
The MES system establishes a complete supplier delivery quality record and batch information: each supplier can record the label of the parts that enter the enterprise according to the electronic version to understand its model, type, batch, production date, etc., and enter Warehouse and outbound management. Real-time monitoring of the production line: RFID tracking management is carried out for the entire production process from the product entering the assembly workshop to the final inspection of the vehicle.
Rework management
The MES system records the repair records of the repair workstation, which is convenient to understand the repair status of the product and analyze the reasons for the repair. The knowledge base prompts the repair personnel to quickly grasp the repair method and improve the business level.
Equipment management
The MES system tracks and guides equipment maintenance to ensure the smooth progress of the manufacturing process, promptly alarm when abnormalities are found, and generate periodic, periodic and preventive maintenance plans, and respond to problems that directly require maintenance.
SPC statistical process analysis
The MES system records the quality information in the production process in real time, such as the torque of the assembly shop, the data of the inspection line, the data of the filling machine, the equipment parameters of the painting shop, and the size data of the welding and frame workshops. And use SPC to monitor, notify the relevant responsible department to deal with the abnormality in time, and track the cause and handling of the abnormality.
Cost Control
Use modern logistics theory to improve the storage of auto parts and complete vehicles, save costs, and save the waste of production and temporary inventory in each workshop of the enterprise.
Product traceability
my country has formally implemented the automobile recall system, which puts forward higher requirements for product traceability. Product traceability requires detailed production site records, including all aspects of production, quality, and materials.
According to the RFID tag information, the production information of each key station of the vehicle in the assembly workshop can be inquired in real time, such as production time, operator, inspector, batch, serial number, quality data, process data, test data, etc., and understand Information about the manufacturing process, such as repair and processing results.
According to the RFID tag information, you can query the quality information of the car at important stations, including defect data and measurement data, as well as various data such as the process capability of the station;
Defect management
The whole vehicle production of the MES system is mainly assembled, involving a large number of components (including in-house self-made parts and outsourcing parts). Various defects are unavoidable during the assembly process. Produced by the process. In order to improve the quality and reduce the repair rate, it is necessary to monitor the defects of each car in real time, record them in real time, and take timely measures.
Report and decision analysis
The MES system supports custom multi-dimensional analysis, such as layered analysis of bad situations by department, model, time, bad type, shift, etc., and the vertical (historical) and horizontal (product, workshop, production line) comparative analysis of production and quality information, etc. ;
Application effect
The MES automobile whole-vehicle barcode traceability system is a management platform for effective quality management, logistics management and control of the product chain. The data is based on the ERP system. The system is a hierarchical system that can provide management, executive and business layers. Various quality information and logistics information required by each.
1. The electronic tag can be read multiple times (up to 100,000 times)
2. RFID electronic tags can be stably read by the reader (low error rate).
3. A lot of manpower and time can be omitted.
4. The command of the main system to the production process is comprehensively improved.
5. The whole production process and the main system are connected together, and the production efficiency is greatly improved.
Systematic management, control, evaluation and traceability of the quality of the entire vehicle life cycle to help increase productivity, reduce consumption, maintain product quality stability and improve product quality. Use product barcode information as a button to establish a A product information management platform that supports the entire life cycle, and realizes the front-to-back traceability of product information.
The automobile barcode traceability system uses barcode technology to achieve automated data collection. Not only does the barcode data collector realize the data collection of warehousing operations in logistics operations in the warehouse, but also obtains real-time barcode scanning in the production process and quality inspection links. Production and quality inspection information. Realize the transparency of factory logistics and production through barcode technology, industrial control technology and wireless network technology.
[ad_2]