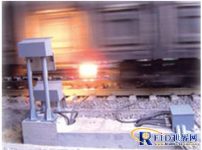
Application Scheme of Dynamic Image Detection (TFDS) System for Railway Freight Car Operation Faults
[ad_1]
In order to promote the modernization of the railway and realize the leap-forward development of the railway, the Ministry of Railways has carried out the reform of the transportation management organization system to continuously improve the level of technical equipment: it has formulated the principle of “overall planning, step-by-step implementation, main line first, and gradual implementation” train maintenance layout reform principles ; It is determined that “according to the changes in transportation organization, targeted and parallel inspection stations will be combined to reduce the number of train inspection operations, promote the transformation from human inspection to machine inspection, static inspection to dynamic inspection, and gradually realize the separation of inspections and repairs to achieve the goal of human “Optimization of machine integration” is the goal of reforming the layout of train maintenance; successfully applied the TFDS system, a dynamic fault detection system for freight trains, to perform real-time detection of trains in operation, improve the failure discovery rate of train inspection stations, and realize the purpose of machine control instead of human control. , Applying machine vision technology to the dynamic detection of key components that affect train safety.
The truck operation fault dynamic image detection system is a set of intelligent system integrating high-speed digital image acquisition, large-capacity image data real-time processing and precise positioning pattern recognition technology. The transition of the way of “inspection and repair” and the transformation of train quality from “human control” to “machine control” have reduced the labor intensity of inspectors, and created conditions for improving transportation efficiency and ensuring transportation safety.
The truck operation fault dynamic image detection system uses a high-speed camera to collect images of the running train, analyzes and processes it through a computer, calculates the train running speed, determines the train type and model, and takes out the images of the key parts of the vehicle required by the system for storage. It is displayed in the window computer in a way of one car and one gear, and can be printed and transmitted as required. Through the combination of man and machine, it is determined whether the bogie, braking device, coupler buffer device and other components and parts of the vehicle are defective, broken, missing, etc., so as to achieve the purpose of dynamically detecting the quality of the vehicle.
The system consists of two parts: railside image acquisition station and train inspection center. Among them, the rail-side image acquisition station is composed of wheel sensors (magnetic steel group), vehicle number acquisition system, front information processor, image server, high-speed image acquisition equipment, light source compensation equipment, rail-side equipment protection device and network transmission equipment. The train inspection center is composed of network transmission equipment, network server, and image browsing terminal. It needs to realize multiple functions:
1. Automatically shoot and filter out the images of key parts of the vehicle such as the vehicle bogie, basic braking device, and coupler buffer device;
2. Through the combination of man and machine, analyze the captured images and identify related faults;
3. Automatically distinguish vehicle number, vehicle type, model and axle counter;
4. Automatically test the train speed;
5. Can directly read the vehicle number information in the AEI system;
6. It can automatically generate frequently used reports for train inspection stations such as CTS-15 and CTS-81;
7. Some faults can be intelligently identified;
8. It can realize the sharing of distributed detection and centralized alarm network monitoring information.
Combined with the above-mentioned requirements and characteristics of the railway freight car application site, the following requirements are put forward for the system:
1. Multi-channel I/O interface is required;
2. The CPU frequency rate is relatively high, and a lot of image processing is required;
3. Gigabit network transmission, which is convenient for data transmission to the server quickly and smoothly;
4. The unattended system requires high stability and self-recovery;
5. The high vibration environment on the rail side requires the system to have high seismic performance.
EVOC’s 5T railway special machine is perfectly applied to the TFDS system. The product specifications are as follows:
Dimensions: 177mm(H)×482mm(W)×452mm(D)
CPU: Core? 2 Duo 2.4G/2.5G/2.6G/2.8G/3.0G (optional)
Memory: 2G/4G (optional)
Hard Disk: 500G
Electronic disk: 2G DOM electronic disk
Optical drive: 18xDVD (optional)
Network: Dual gigabit network RJ45 access, convenient to connect to high-speed network cameras
Standard I/O: 2 RS-232 serial ports
Backplane: Compatible with 13-slot and 14-slot backplanes, support ISA/PCI/PCI-E multiple bus expansion, convenient and quick expansion of user’s I/O card, video capture card
Front panel: with LCD screen, real-time temperature monitoring and operation status display of power supply hard disk
Power supply: support PS/2 power supply
Others: use 2 shock-proof bead to prevent vibration
Structure: safety door with lock protection control components, keyboard interface at the front and rear of the whole machine
System: Support Windows XP -embedded embedded operating system
The EVOC railway 5T dedicated complete machine satisfies the special requirements of the railway system for industrial control products through a variety of humanized and industrialized design for on-site application characteristics:
1. EVOC’s unique EPI bus and its interface, using European connectors instead of golden finger connection, 360-degree contact, sealed and dust-proof, strong structure, anti-vibration, can withstand a certain degree of gravity, to ensure a stable and firm connection. It is more suitable for the high vibration environment of the railway track;
2. Abundant extensions, fully meet the convenient access of various control cards, I/O cards and cameras;
3. Supports a truly high-performance dual gigabit network, and provides a good network environment for code application/release;
4. Support Windows XP -embedded embedded operating system, support the unique EWF system protection function of embedded system, and meet the unattended requirements for high reliability and high stability of the system;
5. Support DOM electronic disk, load the embedded system into the electronic disk to realize the complete separation of system and data storage, and ensure the stability of the system;
6. Built-in watchdog system and lead out the reset signal through the DB9 interface, the user can conveniently control the automatic restart of the whole machine through software or external signals to meet the requirements of the system self-recovery on site.
[ad_2]