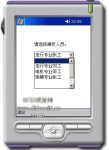
RFID locomotive important parts life management system
[ad_1]
1. System overview
The reliability of the use of important parts is an important indicator to ensure the normal functioning of locomotives. Strict maintenance and life management of important parts is an important means to ensure their quality.
In the process of using and repairing the existing important parts, the maintenance department has established a large number of ledger records, but it is very inconvenient to store and query the recorded ledger, which brings certain difficulties to maintenance and affects the efficiency of spare parts turnover. A complete set of accessories has been established Maintenance history and life management system will bring great convenience to parts maintenance.
The design purpose of this system is to install electronic tags on important accessories, and update the maintenance history content in the database associated with the electronic tags at any time according to the usage and maintenance of the accessories, so that the accessories have a lifelong history account.
1.1. System composition
“Important parts life management system” is composed of three parts: 1. Parts electronic label 2. Reading storage device 3. Computer software.
(1) The electronic label is fixed on the flat surface of the accessory, and high-strength glue is used to fix it on the accessory. The electronic tag uses the ultra-high frequency 915M tag, and the storage area stores a unique ID number.
(2) The reading and storage equipment uses an integrated RFID handheld terminal, which can work continuously for more than 36 hours with low energy consumption, and the operating distance can reach 20-50 cm. The support system includes WINCE5.0.
(3) The content of computer software includes server-side software and client-side software. The server-side database adopts SQL2000, and the software includes functions such as data backup and data recovery. The client software includes the following modules: 1. Label distribution 2. Inquiry 3. Early warning 4. Setting, server-side software and client-side software are written with full consideration of interface and expansion issues.
1.2. Function description
This system fully considers the on-site application situation and is designed for the maintenance department of important parts. The system is composed of three functional modules.
(1) Electronic label management
The system can view the fixed information of all accessories (manufacturer, model, serial number, delivery date, loading date, segment, maintenance history) and maintenance history (overhaul, intermediate repair, minor minor repair, return to factory) at any time for easy analysis and maintenance .
After the repair, through the operation of the electronic label, the maintenance information is associated with the electronic label to replace the paper account record, which is convenient for future maintenance and inquiries.
(2) Management of portable reading and storage devices
Portable reading and storage equipment is necessary for communication with electronic tags. It is connected to a computer. It can store information and can be used independently from the computer. This situation is convenient for the staff to use the electronic tags without a computer on site. Information is read.
When the portable reading and storage device is not connected to the computer, it can read the electronic tag and edit the maintenance status of the accessory at the same time, which is convenient for the actual operation on the spot.
When the portable reading and storage device is connected to the computer, it can synchronize data with the computer and update the latest maintenance records of the accessories into the database.
If the construction site is equipped with a wireless network or is allowed to connect to a wide area network, every step of the operation performed by the portable storage device for accessories can be updated to the system in real time.
(3) Ledger record management
The addition, modification, and deletion of account records are completed by reading and storing equipment. In the network computer, the account records of each accessory can be queried through software. These records are updated with the operation of the electronic label, and the data is stored in the server , When users need to query the resume of a certain accessory, they can use various conditions as keywords.
The system sets its own judgment and analysis standards for each accessory. According to the latest data after synchronization, the system can automatically analyze the current status of various and every important accessory, and give obvious hints on the interface.
1.3. Technical features
This system combines radio frequency technology, electromagnetic compatibility, semiconductor technology, data protection and cryptography and other multi-disciplinary expertise together with a complete software design, and finally realizes a complete monitoring device component maintenance history management.
The system architecture is on the TCP/IP network, which connects to the system database remotely and performs access operations to tag data. On the PDA side, the system uses VC++ and VS.NET 2003 technology to communicate with the PDA, and reads and writes the tags simultaneously.
2. Software description
2.1. Software operation (wheel set)
The engineer uses the handheld terminal to edit and modify the data, store it in the handheld terminal database, communicate with the upper computer, and send the data back to the server database. Both the handheld terminal and the PC-side software interface can prompt the status of various accessories according to the set conditions.
This section describes the maintenance management of wheel sets.
2.1.1. Operator selection
Before the operator uses the storage-reading equipment to overhaul accessories, first select a name (it can also be set to log in to the system through a user name and password).
2.1.2. Automatic recognition of accessories
When operating on accessories, the system will automatically retrieve and display the type and basic information of the current accessories based on the ID number in the electronic tag.
2.1.3. Fill in the inspection record when the accessories get off the car
When the wheelset gets off the car, the traveling engineer inspects it and edits various data into the handheld device.
2.1.4. Fill in the maintenance record after the parts are overhauled
When the wheel set is overhauled and needs to get on the car, the engineer uses the handheld device to edit the new data and update the relevant data of the electronic label.
2.1.5. Analysis of accessory status
1. Good spare parts
When all the following conditions are met, the wheelset is in good condition:
2. Spare parts to be repaired
When any one of the following conditions occurs, the wheelset status is a spare part for repair:
3. Spare parts for boarding
When the wheel set has been overhauled and checked again, and all the following conditions are met, and after a certain locomotive is designated for boarding operation, the wheel set status is on board:
2.1.6. View the situation of handheld terminal accessories
Because some parts stay in the locomotive depot and maintain a long time after getting off the vehicle, based on the unified database and the update of the data of each handheld terminal in the system, when different engineers use different handheld terminals to read the wheel sets, the program interface The current status of the round should be displayed. If there is a need to be repaired, it will be reflected in a conspicuous way (as far as possible, all faults will be listed at once). The interface is shown in the figure:
2.1.7. View the status of PC-side accessories
The program has a special button “Alarm Spare Parts to be Repaired”. After clicking it, all current wheelsets to be repaired will be listed. The interface is as follows:
On this interface, the summary of each round of failures is listed, click to view details, you can view various indicators.
2.1.8. Overall management of interchangeable accessories
On this interface, the number of all wheel sets in the current locomotive depot will be listed, as well as the number of vehicles that have been on board, the number of good spare parts, and the number of spare parts to be repaired. For the latter two, also list the locomotive type and axle number, as shown in the figure below:
In the above table, click on any wheel set to view the details of the previous on and off records and maintenance records of the changed wheel set.
[ad_2]