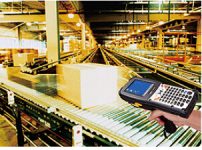
Based on RFID technology in manufacturing logistics application solutions
[ad_1]
1. System introduction
Informatization, automation, networking, intelligence, and flexibility have become the distinctive features of modern manufacturing enterprises. With the popularization and development of information technology and network technology, especially Internet technology, it has solved the standard problem and cost problem of information sharing and information transmission, making information more widely used as the basis and basis for control and decision-making. In order to reduce costs and speed up capital turnover, it is necessary to further solidify new processes or new management systems so that they can be implemented in a standardized manner. The role of information systems is to solidify management and optimize operations.
The tracking of materials and work-in-progress (WIP) and JIT and MES are new concepts put forward by American management circles in the 1990s. In the past 10 years, these aspects have developed rapidly abroad, and some professional development companies have gradually formed. At present, the domestic understanding of these aspects and the level of research and application are not high, and the gap with foreign countries is widening.
Based onRFIDThe material and work-in-progress tracking management system makes full use of the advanced management concepts and basic methods of JIT and MES to analyze and monitor processing data through real-time feedback of workshop production information, strengthen workshop production control, and improve manufacturing, especially An important measure for traditional manufacturing technology innovation capabilities, market response speed, and comprehensive competitiveness.
The application of RFID in the traditional manufacturing industry is a set of industrial production process automation management system developed for the materials and products in the workshop production line based on the information application of production enterprises. The precise collection, integration, integration, analysis and sharing of “work-in-process” information provides basic information solutions for the management of enterprise production materials and product life cycle management. It is the core content of the workshop manufacturing management system. The application of the system and ERP, CRM, SCM system form a good complement, effectively solve the ERP system in material and product data collection, data accuracy and real-time input and other issues, is to achieve the overall informationization of the factory or production enterprise Hub information system. Especially the independent research and development of electronic label terminal products suitable for traditional manufacturing applications and the manufacturing application system of electronic labels based on this can meet the needs of the country in different fields, especially the market for electronic label applications in key industries such as manufacturing and medicine. need. The system has the following design concepts:
The integrated application of RFID technology in the workshop field data terminal (such as kanban terminal or touch screen) fully adapts to the complex requirements of the industrial environment without direct vision or manual scanning. It effectively and concisely solves data collection, data accuracy and real-time input, etc. Aspects of the problem;
Provide data module design for “individual” or “batch” level, real-time, accurate, precise and efficient traceability and tracking of materials and work-in-progress, and use this as the core to establish a real-time file at the individual level of the product to realize the life of the product Cycle tracking and management;
Apply RFID, JIT, MES, network technology, etc. to production management and control, accurately, real-time, and comprehensively reflect the status information of the production process, effectively and agilely guide the industrial process, form a good complement to ERP, CRM, SCM, and promote the “transparent factory” Construction, promote the optimization of production, management and organizational structure, and promote the realization of the JIT production model;
The tracking management of “materials” and “work in progress” is closely integrated with quality, benefit, efficiency, warehouse management, logistics, etc., to encourage workshop workers, manufacturers and material suppliers to form a community of interests.
The Application of RFID in Traditional Manufacturing (MES) project makes full use of the characteristics of RFID, adopts specific RFID data collection terminals that can be installed in complex industrial sites, adapts to the environmental requirements of traditional domestic manufacturing workshops, and is moisture-proof, oil-proof, and lightning-proof , Electromagnetic interference, heat resistance, etc., meet the needs of non-contact automatic collection of materials and products in progress, and provide information input interfaces and query interfaces for the management system.
At the same time, on the basis of the RFID data collection terminal, a workshop-level production execution management system with a software basic platform and a series of application modules can be developed with the tracking of materials and work-in-progress as the core. In the design process of the system, through the design of data modules oriented to “individual” or “batch” levels, the traceability and tracking of materials and work-in-progress will be realized in real time, accurately, meticulously, and efficiently. This is the core to establish individual products. Level of real-time archives. In addition, in the system design concept, RFID, JIT, MES, network technology, etc. are applied to production management and control, accurately, real-time, and comprehensively reflect the status information of the production process, effectively and agilely guide the industrial process, and form a good relationship with ERP, CRM, and SCM. Complementary, promote the construction of “transparent factory”, promote the optimization of production, management and organizational structure, and promote the realization of the JIT production model.
The application of RFID in the traditional manufacturing industry is an industrial information application system for the manufacturing industry. The use of high-tech, especially automation technology, information technology to carry out beneficial transformation and information services to the traditional industry (manufacturing industry) is to promote my country’s export-oriented The main manufacturing industry develops high-tech products. The application of RFID in the traditional manufacturing industry is aimed at the actual situation of my country’s manufacturing industry, with the purpose of developing advanced, integrated, production line-oriented management software, which can effectively improve the operating economy and service quality of discrete manufacturing enterprises. This project The success of the development will undoubtedly have a significant driving effect in the industry.
The use of RFID technology can improve the traditional working mode and realize the full-process control and traceability of products in the manufacturing industry. The development of a complete RFID-based production process control system is to use RFID technology throughout the entire production process (order→plan→task→material preparation→cold processing→thermal processing→finishing→inspection→package→warehouse→transportation) to form Closed-loop production of the enterprise.
From a development perspective: the implementation of RFID technology in the manufacturing industry can also extend from raw material manufacturing, procurement to semi-finished products processing, finished product manufacturing, wholesale, distribution to retail, through every link of the supply chain of the whole society, until the final consumer. Therefore, the use of RFID tags in the manufacturing industry can break the isolation of a system’s internal use and extend RFID technology to the upper end of the supply chain. The research results can also be extended to other related product manufacturing applications, which has good application prospects and industry demonstration effects. These industries that can apply the research results even include food manufacturing companies.
2. System Features
RFID workshop manufacturing and execution system or work-in-process tracking and management system has the following characteristics:
Production plans and processes are directly transferred to procedures and equipment (while ERP and MRPII can generally only be transferred to varieties and workshops), directly guide equipment processing, prevent cross-process processing, and reduce process errors;
Real-time data collection, plan assessment can be carried out in time, and production progress can be monitored in real time;
The functional departments of each workshop can share production data, understand the production progress of related processes, and facilitate production coordination. Accurately confirm the delivery time and realize batch management;
Process feedback correction: correct process errors in time and shorten the process correction cycle;
Processing data is effective, reducing manual input and paper transfer;
Facilitate quality traceability;
Smart Kanban: complete quality information collection and quality analysis;
Extended logistics management: RFID batch number-barcode-product;
The RFID data collection terminal used at the workshop site is used to provide the system with information about materials, products, equipment status, personnel information, etc., to achieve two-way communication between the system and specific operators. Has the following functions and advantages:
Automatic collection: can automatically collect materials, work in progress, workstations, and personnel information without contact;
Information query: can query production plan, production process, product batch and other information;
Information input: equipment status information, processing quantity, processing status, quality information, etc.;
Resistant to harsh environments: it has the performance of moisture-proof, oil-proof, lightning-proof, electromagnetic interference and heat-proof.
The system includes the following tasks:
Construction of overall architecture and system model: Through in-depth analysis of network architecture, factory equipment, communication routing, software and hardware combination, and system scale and performance, establish the hierarchical relationship between monitoring system software and data acquisition hardware equipment, and determine each functional module The division of modules and the interfaces between modules complete the construction of the overall architecture. Fully consider the Integratability, Configurability, Adaptability, Extensibility and Reliability of the system;
Software platform architecture construction: Based on object-oriented design technology, distributed network, and various advanced database and configuration technologies, build a system software basic platform suitable for real-time, on-site, and remote monitoring, easy to expand and modify, and fully reflect the orientation The system application integration of discrete objects supports real-time activities and realizes the combination of management and control based on on-site management rules and comprehensive management knowledge. It mainly includes the construction of software system function positioning, platform selection and data collection (Data Collection), data storage (Data Storage), network application (NET/Web Application), client query browsing (Client/Web Viewer), etc.;
Specific software development of functional modules, including:
Production process modeling (CONFIG)
Production planning and production management
Field data collection
Material tracking query
Work in progress tracking query
Product Life Cycle Archive
Quality and performance analysis query
Internet applications
Workflow research: design workflow models and network data flow planning, support various control and communication strategies, support various workflows in the production process, and realize automatic driving, recording, tracking, analysis, and information sharing of manufacturing production and management processes, etc. , And easily integrate CORBA/STEP to achieve seamless integration with ERP, PDM, SFC, etc., forming a smooth channel for information flow;
Device communication and integration and data connection technology: standardize different industries, different types of monitored devices and system interfaces, including digital or analog sensors, programmable logic controllers (PLC), direct digital controllers (DDC), control execution Research on data formats and protocol conversion methods of various equipment and systems to meet large-capacity and high-speed data storage and access, with real-time and continuous historical data retrieval and playback functions, and provide complex and special Data query;
The realization of intelligent decision support function: the purpose of real-time monitoring is to provide data for the decision-making of dispatching and operation operators. If the system can reflect the production status while having data analysis functions, and then propose operation plans and suggestions, its practicality can be achieved Really manifest. The solution of this problem depends on the application of intelligent technology and the inductive expression of expert experience;
System testing: including unit testing, overall testing and comprehensive testing.
3. Application technology scheme
1. The overall architecture of the system
Including the software platform and application module system, as well as the hardware platform on which the system depends.
The software platform is the basic core component of the system, including a series of components that implement various core logics, and encapsulated into different component packages:
Scheduling Strategy Component Package
Interface development component package
Production process model component package
WIP component package
SPC analysis component package
Device communication interface component package
ERP interface component package
RFID terminal component package
The application module system is built on the framework of software platform and hardware platform to realize various specific management functions of the system, including:
Production process modeling
Production planning and production management
Field data collection
Material tracking query
Work in progress tracking query
Product Life Cycle Archive
Quality and performance analysis query
Internet applications
2. Hardware platform foundation: RFID data integration terminal
1) RFID data integration terminal (RFID DCS)
The RFID DCS terminal (reader) will be mainly installed at the production station of the production line to provide the MES system with information about materials, products, equipment status, personnel information, etc., and also provide operation information for specific operators Two-way communication.
The need for automatic collection: the information of materials, work-in-progress, workstations, and personnel can be collected automatically without contact;
The needs of the collection environment: the data collection site is diversified, and the collection equipment and the collection terminal are required to have moisture-proof, oil-proof, lightning-proof, electromagnetic interference, and heat-proof performance;
Query needs: can query production plan, production process, product batch and other information;
Information input needs: equipment status information, processing quantity, processing status, quality information, etc.
The specific approach is: in the RFID technology-basedelectronic labelThe reader (data integration terminal, RFID DCS) adds modules such as liquid crystal display circuit, PVC keyboard input circuit, digital display measuring instrument communication interface circuit, RS485 serial communication circuit, and TCP/IP network communication interface circuit. The liquid crystal display can display the issued production plan, production process, product batch and other information, and the keyboard can submit equipment status information, processing quantity and quality information, etc., so as to fully track the normal flow of workpieces in the normal process route and handle various abnormalities It records the completion status of each work piece in each process and the current position and online status of each work piece. It can automatically record the status of each work piece (pending inspection, qualified, Unqualified), all-round record of the circulation (process, work position, time, status) of each workpiece in the manufacturing platform.
2) Communication method:
The RS485 serial communication circuit and the TCP/IP network communication interface circuit can be selected as one of the communication methods to interface with the PC. After the information collected by the terminal enters the PC through the communication interface, the PC then stores the information, processes the information, and saves the results to the server. The PC can also transmit the production plan of the workshop on the day and the production situation of the workshop to the terminal through the communication interface and display it on the terminal’s LCD screen. After the workers see the feedback information, they know the production tasks of the day and the current working conditions to execute them. production task. In the RFID DCS terminal collection system, there is a certain communication protocol between the PC and the terminal to ensure the successful communication of terminal data.
[ad_2]