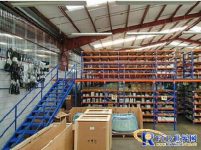
RFID factory warehouse logistics solutions
[ad_1]
Introduction
At present, market competition is becoming increasingly fierce. It is very important for enterprises to improve production efficiency and reduce operating costs. Warehousing logistics management is widely used in various industries, designing and establishing a complete set of warehousing management processes, improving warehousing turnover rate, reducing the occupation of operating funds, turning frozen assets into cash, reducing the cost caused by warehousing elimination, and improving the company An important part of production efficiency.
Warehouse management systems usually use barcode labels or manual warehouse management documents. These management methods have obvious disadvantages:
Barcode management: easy to copy, not stain-proof, not moisture-proof, and can only be read at close range.
Manual entry: The work is cumbersome, and the amount of data is large and easy to make mistakes and omissions, which increases labor costs in the warehousing process.
The workload of manual inventory is large, which leads to a long inventory cycle, and the missing or stolen goods cannot be found in time
RFIDThe introduction of radio frequency technology will make enterprise warehouse management more transparent and more efficient. Encapsulate the electronic label in the bar code label, stick it on the package or pallet of each goods, and write the specific information, storage location and other information of the goods in the label. At the same time, the detailed information of the delivery party can be written when the goods enter and leave the warehouse, and fixed or hand-held readers are installed in the warehouse and various distribution channels to identify and monitor the flow of goods.
The main components of the system
RFID electronic label
RFID printer (optional)
RFID fixed reader
RFID handheld reader
RFID forklift reading system (optional)
RFID channel reading system
Yapu RFID Middleware
Energetics? RFID warehouse logistics management system
system design
When warehousing
In the finished product packaging workshop, workers first affix RFID electronic tags to the products, and then affix the box label after batch packing. If the pallet is required, the pallet label can also be affixed after the pallet is finished. The general labeling methods are:
Single product labeling
Multiple products are packed together, and the outer packaging is labeled.
The pallet is labeled and associated with the single product label or outer packaging label data.
The packaged products are put into the warehouse by the loading and unloading tools through the channel composed of RFID readers and antennas. The RFID equipment automatically obtains the warehoused quantity and records it in the system. If there is a pallet label, the information of each pallet is written by the import port reader. Pallet labels, at the same time, form the order data association, calculate the storage location through the computer warehouse management information system (or manually specify the storage location for the batch at the beginning), and send the inventory instruction to the warehouse client through the network system (or forklift truck) System), the forklift personnel are stored in the corresponding storage location as required.
After the warehousing is completed, the system updates the inventory data and marks the location information of each batch of goods.
When leaving the warehouse
The consignor of the logistics department generates an outbound order based on the invoice required by the sales: that is, according to the outbound priority (for example, the first out of the warehouse before the production date) to inquire the warehouse for the storage location and inventory status of the outbound goods, if there are customers The designated batch number will be queried according to the designated batch number, and the outbound cargo pick-up bin and the corresponding pallet belonging to the cargo and the loading vehicle will be generated.
The consignee brings the outbound order to the warehouse manager, and the warehouse manager checks the information to arrange for the forklift driver to carry out the corresponding product out of the warehouse.
The forklift picks up the goods and passes through the exit gate. The exit gate RFID reader reads the pallet label on the pallet to obtain the outbound information, and verifies whether the product batch number and location listed in the shipped product and the outbound order are correct.
After the delivery is completed, the warehousing terminal prompts the delivery details for the administrator to confirm, and automatically updates the data to the database.
Inventory time
Staff can use handheldReaderRegular inventory, read the label information of the goods at close range, and compare it with the back-end management system, and manually check whether the variety, quantity, and production date of the goods in the storage location are consistent with the back-end system. If they are inconsistent, the system information can be corrected on site. This inventory method can shorten the enterprise inventory time by 85%, greatly improve work efficiency, and at the same time increase the inventory cycle.
System performance
Labor can be reduced by 20-30%;
99% of warehouse products are visualized, reducing the risk of missing goods;
Improved supply chain management will reduce work service time by 20-25%;
Improve the accuracy and reliability of storage information;
Efficient and accurate data collection provides operational efficiency;
Automatic collection of incoming and outgoing data to reduce human error;
Reduce enterprise warehousing logistics costs.
[ad_2]