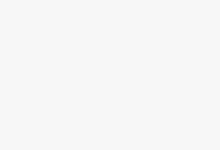
Design Scheme of Energy-saving Control and Management System for Non-contact IC Card
[ad_1]
content
Section 1. Overview
Section 2. Description of the non-contact IC card water control management system
1.System composition description
2.System equipment description
3.System function description
Section Three, System Configuration and Quotation
Section 4. Construction period
Section 5, Project Organization and Service
Section 1. Overview
Under the current situation, the global pollution is gradually serious, and the management and conservation of water resources has become a worldwide problem. China has a large population and limited available water resources. When the available water resources are seriously polluted, saving existing water resources has become a top priority.
The energy-saving control system developed by our company adopts the MIFARE I type originally produced by PHILIPSNon-contact IC card, The card has a 32-bit unique serial number in the world, has strict logical operations and logical encryption functions, and a storage capacity of up to 8Kbit. It is divided into 16 sectors to support multiple applications, and each sector has its own set Password, can customize the access conditions of each sector, far superior to magnetic cards and ID cards in terms of read and write speed, read and write security, system scalability, etc., use high-performance energy-saving controller to automatically control the water outlet solenoid valve to discharge water When shutting down the water, the energy-saving controller automatically charges according to the actual water or electricity consumption, and automatically charges from the IC card e-wallet; it is suitable for bath shower charge control, boiling water/hot water charge control, drinking water charge control, and electricity use Charge control, laundry charge control, agricultural irrigation, green watering, industrial water, warm air supply control and other small consumption applications.
The energy-saving controller can run offline and collect data with a hand-held acquisition card. It can also be connected to the management computer through the network to use energy-saving management software for equipment parameter setting, consumption data collection and query, statistics, reports, settlement and other processing. So as to achieve the purpose of saving water and electricity, scientific charging and efficient management.
This system is simple to use, easy to operate, and powerful. It completely replaces outdated consumption methods such as cash, tickets, and magnetic cards. Using the multi-sector feature of MIFARE I, it can easily expand a variety of functions, such as: canteens, commissaries and Supermarket shopping, medical fees, faculty and staff attendance, dormitory access control management, computer online charging management, student status management, parking lot fees, etc. can all be realized by virtue of the card’s one-card multi-purpose performance.
Section 2 Non-contact IC card energy-saving water control management system
The inductive IC card energy-saving control system developed by our company can not only save water and electricity, but also achieve the purpose of scientific charging and efficient management.
1. System composition description
The entire management system is composed of a central processing part, a data collection part, and a front-end equipment part.
Central processing part:
1. Authorization card issuance, deposit, loss report, cancellation, card recycling
2. Data sorting, statistics, query and printing
Hardware parts:
computer
printer
Non-contact IC card issuer (RD-M920)
Software part:
Operating system: Chinese operating system above Windows98
Non-contact IC card water control charging system
Data collection part (off-line model): Use a collection card to collect data, which greatly reduces the workload of project construction.
Capture card
Front-end equipment: processing and storage of consumer data
The components are as follows:
Power supply (12V)
Solenoid valve / electric control valve ()
Water/electricity meter (selected when measuring)
Non-contact IC card water controller (RD-M710)
2. Description of terminal equipment
M710/M720 water controller
The main technical parameters
• Card reader type: MIFARE standard card
• Working frequency: 13.56MHZ
• Maximum record volume: 40 million yuan
• Number of cards issued: unlimited
• Data saving: FLASH saves data, no loss after power failure
• Display; 6-digit digital tube display
• Working voltage: DC12V, power consumption is less than 3W
• Ambient temperature: 0 degrees -50 degrees
• Volume: 140MM*102MM*30MM
• Weight: 300G
Product features
• Light-colored translucent shell, smooth appearance design, full of fashion
• Fully waterproof design, double-layer design of the keyboard and upper and lower shell seams, with silicone seals for waterproofing
• Unique water-saving design, using card reading and switch dual methods to control water, after inserting the card, press the water button to release the water, remove the card or press the water button to stop the water, more humane and water-saving
• Power-saving design, the device will automatically power off after 30 minutes without reading the card or without key operation, and automatically start after reading the card or pressing the key
• E-wallet application, only records the consumption amount, eliminating the trouble of account inconsistency
• The accumulated data can be extracted by using the data acquisition card, without complicated networking, reducing the amount of construction
• Use timing method to deduct fees, and you can set the rate flexibly to meet various requirements
• With the flow meter, the metering method can be used to deduct fees, which is more scientific, fair and reasonable
• The system is easy to access, the upper software can be connected with the original consumption management system, and the card can be issued directly without re-entering personnel information, which is convenient to expand into a card based on the original consumption system
• It’s easier for users to recharge. You can recharge through self-service card transfer and management center recharge.
RD-M920 reader (recharger)
The M920 reader we chose is one of the ROAD series products. It can read, write, issue, and recycle cards in cooperation with this system, and recharge the card will have the best effect.
The main technical parameters
1. 5-digit LED digital tube display can display date, time, valid card number, operation prompt information, etc.
2. The read and write time is less than 0.3 seconds.
3. Power supply voltage: DC12V
4.Communication mode: one of 232 or 485 communication modes can be selected
5. Ambient temperature: -10℃ – +50℃
6. Working frequency: 13.56MHZ
7. Operating distance: 50mm
3. Control system business process
The system adopts the prepayment method for hydropower control and management, and the normal use process is as follows:
Put the card and press the start button to discharge the water and press the stop button to take the card
1) The consumer inserts the recharged user card into the energy-saving controller, and the energy-saving controller automatically determines whether the card is a valid card. If the card is legal and valid, the energy-saving controller is allowed to be used. If it is an illegal card or invalid card, an alarm will be issued and the energy-saving controller is not allowed to be used. (The number of times of use and the time of use are set by the setting card).
2) When consumers need water, they only need to press the start button of the energy-saving controller, and the water/electricity control device immediately releases water and the timing starts. The energy-saving controller displays the usage time.
3) After use, the consumer pulls out the user card from the energy-saving controller, and the water control device immediately cuts off the water. And disable the start button until the next card is used.
4) If the number of uses in the user card has been deducted, the water control device will immediately cut off the water and the button will become invalid. You must wait until the next day before you can continue to use it.
The manager can collect the charging data in the energy-saving controller through the acquisition card. Card management such as user card issuance, card replacement, and recycling is handled by the smart card center in a unified manner.
4. Functional characteristics of energy-saving control system
1) Adopt a special waterproof design to adapt to the environment such as bathhouses.
2) Realize automatic water supply control and charging, can realize unattended, adopt electronic wallet transaction, avoid management loopholes and be more scientific and efficient.
3) Charge deductions based on actual water consumption or electricity consumption, and start timing of water discharge, which achieves personalized consumption and energy saving, fair and reasonable for consumers and contractors, and takes into account the interests of both.
4) As the timing can be seen, users will consciously shorten the water and electricity time and increase the turnover rate of water supply/power supply equipment, thereby saving resources.
5) Cultivate people’s awareness of saving, benefit the country and enterprises, and promote the construction of spiritual civilization. IC card management is convenient and accurate, which improves management efficiency and grade.
Section Three, System Configuration and Quotation
The system configuration diagram is as follows:
The following is the system quotation
Section 4 Construction Period
1. Construction schedule
2. Engineering quality management
1) Establish a quality assurance organization and strengthen project quality management.
2) Strengthen employee education and improve quality awareness.
3) Strictly control the purchase of materials to ensure the normal use of construction equipment.
4) Optimize the construction method to achieve the purpose of prevention first.
5) Strengthen the process quality inspection and do a good job in the protection of finished products.
First of all, carefully review and sign the construction drawings, and clarify the technical requirements and quality standards. Do a good job of quality and technical clarification on this basis.
6) Construction in accordance with specifications and strict quality control
Strictly follow the construction drawings and construction specifications to check the construction quality. The company’s quality assurance department inspects project quality records from time to time, issues quality inspection notices, and issues “Quality Rectification Notices” for projects with quality problems. In the actual construction, the quality is controlled from the following quality links:
Standardized check, review, approval and submission procedures of construction drawings;
Factory testing of products and systems;
On-site inspection of materials when receiving goods;
Construction quality supervision and inspection of piping, wiring, wire duct and bridge frame;
Construction quality supervision and inspection after equipment installation;
On-site commissioning and trial operation of the system;
Completion documents and completion acceptance;
Customer training and follow-up after-sales service.
Section 5 Project Organization and Service
1. Personnel organization:
Project Manager: XXX Project Assistant: XXX
Network technology: XXX Technical supervision: XXX
Equipment installation: XXX and other engineering supervision: XXX
Quality control: XXX Technical service: XXX
Cost control: XXX Technical guidance: XXX
Material supply: XXX
2. Project implementation
The project implementation steps include: design disclosure and construction drawing design, construction preparation, construction and installation process, system debugging, completion acceptance, after-sales service and other stages.
2.1 Design confession and construction drawing design
After the bidder signs the contract in the project, it will first receive the relevant project construction drawings provided by the construction party, including the general floor plan, building floor plan, equipment floor plan, weak current floor plan, all construction drawings of the all-in-one card system, and communicate with the construction party and the design The institute conducts a joint design briefing and review, confirms the design intent, and resolves doubts about the design. During the implementation process, the bidder will ensure that the construction and acceptance are strictly in accordance with the construction drawings of the design institute.
2.2 Laying and installation of pipes, trunking and bridge
According to the construction drawings and on-site measurements, the person in charge of construction determines the direction of the line and the entry and exit points, branch points, laying and installation locations, and submits ground trenching, excavation, embedded parts, reserved holes, and fixes to professional construction parties such as civil engineering, electromechanical, and decoration. “Construction Conditions Book” for the connection method, installation foundation, etc. to cooperate with the construction.
Cooperate with the main structure and decoration, be familiar with the structure and decoration embedded drawings, check the dimensions of the embedded position, and the relevant construction operation, technology, regulations, standards, and construction acceptance specifications; follow the progress of the structure and decoration project, in the work surface Ink marking, blanking and processing, on-site opening and trenching, laying and installation. The person in charge of the construction supervised the construction process and did a good job without leakage. After the laying is completed, the quality engineer should make quality inspection and original construction records, and rework in time if problems are found.
The laying of pipelines should be closely coordinated with professional construction such as civil engineering, electrical and mechanical engineering, and decoration. They must be coordinated with each other and negotiated when necessary.
When there is a difference between the actual line and the construction drawing, a “Design Modification Notice” shall be issued. After the completion of the concealed section project, the construction party shall cooperate with the construction party to check and accept in time and go through the concealed inspection and signature formalities.
2.3 Cable laying of power supply, communication, signal, control, etc.
When laying wires and cables, check the model, specification, quantity, laying position and method according to the requirements of the construction drawings. A certain margin should be left when cutting the material, and the wires and cables must be guaranteed not to be damaged when laying through the pipe.
The wires and cables that have been laid must be marked with the cable code at both ends of each wire and cable, and the outlets should be sealed.
Cables that are not connected immediately should be protected.
2.4 The equipment is installed in place
The installation of equipment is generally carried out after the completion of professional construction such as civil engineering, electromechanical, and decoration.
The installation of the equipment shall be carried out in place after reviewing the dimensions of the equipment and the dimensions of the installation location according to the design drawings and equipment instructions. Equipment that is not connected immediately after installation should be protected.
After the equipment is installed, the quality engineer should make quality inspection and original construction records, and rework in time if problems are found.
2.5 System connection
Before connecting, you should check the wires according to the drawing, mark the wire number on each wire, make the wiring terminal, and make the insulation treatment if necessary.
When connecting wires and cables with equipment, they should be connected correctly and firmly, and arranged neatly and beautifully. After the connection is completed, the inside of the device should be cleaned without leaving any debris, especially metal conductors.
After the connection is completed, the quality engineer should perform quality inspection and original construction records, and rework in time if problems are found.
2.6 System debugging
System debugging generally includes three stages: stand-alone debugging, online debugging, training/trial run.
2.7 Completion acceptance
Before the completion of the subcontracted project, preparations should be made for the delivery and acceptance, and the construction machinery, construction materials, and construction waste should be removed. Do a good job in completion self-inspection. After passing the self-inspection, collate the completion materials, fill in the formal “Completion Report”, and apply to the construction party and the supervisor in writing to organize the completion acceptance.
According to the acceptance plan of the construction party and the supervisor, provide the basis and conditions for the completion acceptance, and jointly check the conformity, completeness and usability of the project. For the missing or problematic parts, they should be improved within the specified time according to the rectification notice. After the rectification is qualified The construction party and the supervision party are requested to sign the formal acceptance certificate in writing.
Completion acceptance includes the process of compiling completion data, organizing acceptance, and project transfer. details as follows:
2.8 Organization acceptance
The project manager should submit the project completion acceptance application to the construction party and the supervisor one week in advance, and the construction party will organize a specific completion acceptance team to conduct verification and review against the contents of the bid/tender, contract, technical agreement, design and construction specifications. If there are suggestions for rectification, the project team should immediately organize the rectification and re-verify it.
According to the actual situation of the project, the project is allowed to undergo the intermediate completion acceptance of the branch.
The project that has passed the acceptance inspection shall be signed by the construction party (including the intermediate completion acceptance of the branch).
The remaining problems of the project will be confirmed when the project is completed and accepted.
3. Service commitment
On the premise of ensuring the quality of the project, the bidder shall make the following technical service and after-sales service commitments to the tenderer:
1) For the construction project commissioned by the bidder to complete the project, the bidder will provide one-year warranty period maintenance service, and the warranty period starts from the date of completion and acceptance by the builder. After the expiration of the warranty period, they will continue to sign maintenance service contracts and provide lifetime maintenance services.
2) During the warranty period, due to engineering construction quality reasons, system debugging quality reasons, or product manufacturing quality reasons, operation failure or product damage (except fragile and consumable items), the bidder will improve the system performance free of charge, replace the defective product, and improve the work Until the user is satisfied.
3) During the warranty period, operation failure or product damage caused by reasons other than the responsibility of the bidder (such as force majeure, intentional or unintentional man-made damage by non-company personnel, improper operation or use by the user or improper transportation and storage, other equipment failures, etc.) The bidder will promptly respond to the requirements of the construction party, cooperate to improve the system performance, replace the problematic product, and improve the work until the user is satisfied.
4) For the products provided by the bidder to the construction party, spare parts will be provided in time at the most favorable price not exceeding the original contract price.
5) During the warranty period, the bidder will regularly send professionals to the site to conduct project quality return visits, listen to the opinions of the construction party, and ensure the good operation of the system.
6) The bidder has set up a professional after-sales service organization and a 24-hour direct service hotline to accept free technical consultation and service applications at any time. For the on-site warranty service of the project, the on-site service will be implemented within 4 hours.
[ad_2]