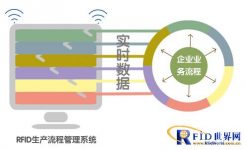
RFID production process management system
[ad_1]
RFID is a flexible application technology that is easy to control, simple and practical, and especially suitable for automatic control. Can work freely in a variety of harsh environments: short-distance radio frequency products are not afraid of oil stains, dust pollution and other harsh environments, and can replace bar codes.
By adopting RFID technology, the system can automatically collect production data and equipment status data, and provide production managers with real-time data on all links of the business process of the enterprise.
In the production process of traditional manufacturing enterprises, most of the production modes are based on the one-piece production mode. The biggest disadvantage of this production line mode is that there is usually a large backlog of semi-manufactured products in certain bottleneck processes. If the process is complicated and With more production links, this phenomenon will become more serious.
At present, the following problems generally exist in the management of traditional processing enterprises:
1) The overall production efficiency is low, and on-site management is impossible;
2) The amount of data in the production process is large, and the backlog of the production line is serious, and automatic circulation and automatic data collection cannot be formed;
3) A large amount of data needs to be manually entered, the accuracy and work efficiency are low, and the reliability cannot be guaranteed;
4) Poor controllability, inaccurate control of the processing schedule, and insufficient ability to monitor the status of the production site;
5) The quality loss is serious, the repair rate is too high, and the quality can not be traced;
6) The production schedule of the order, the work-in-process and completion data of the workshop are not clear, and the cost cannot be calculated accurately;
7) The analysis and statistics of business data cannot be accurate and timely, and it is difficult to dig out valuable information to guide future production plans.
Use EPR production process management assistance system toRFIDAs an information carrier, electronic tags can obtain data from all directions through wired information channels and process them in real time. Record the whole process of each link of the entire enterprise business process, realize the automatic identification and real-time management of the work-in-process, so as to realize the real-time tracking of the product life cycle, and improve the work efficiency and service level of the enterprise production management.
Functions realized by RFID production process management:
1. Technical management: display the hierarchical structure of the product according to the belonging relationship of the parts and components, and realize the compilation and management of product schedules, process cards, and blanking cards. The structure is clear, the operation is flexible, and the function is comprehensive.
2. Production management: compile or import the product details to be put into production from the sales order, and automatically generate the production parts, component details, raw materials, standard parts, supporting parts demand details, and outsourcing processing order details, etc.
3. Process control: By entering the completion information of each processing procedure, the processing progress of product parts and components can be tracked, and the production status and completion rate of each production batch of parts and components can be inquired.
4. Raw material management: including production raw materials, standard parts, purchased parts, etc. Provide a convenient and flexible material coding system to ensure the standard and uniform use of materials; a perfect inventory management system that organically combines material management and production systems to effectively control the use and distribution of materials. Inventory upper and lower limit settings can well control inventory backlog and capital occupation.
5. Work-in-process management: unified management of inventory work-in-process, workshop work-in-process, and outsourced processed parts. All parts are connected with each other to effectively control production logistics.
6. Finished product management: Comprehensive management of finished product inventory and sales. It can count the inventory of each finished product at any time, the quantity in and out of the warehouse, and the amount.
[ad_2]