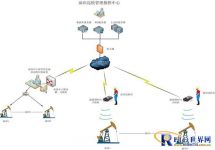
RFID oilfield inspection solution
[ad_1]
I. Overview
In order to ensure the normal and safe production of oil and gas wells, companies need to conduct round-trip inspections on the safe production of oil and gas wells at fixed points to discover and deal with the problems in the safe production of gas wells in time. To this end, a corresponding inspection and listing system has been formulated, and supervision and inspection are carried out from time to time to promote the implementation of the system. Due to the fact that the inspection and listing system is subject to too many human factors in the implementation, the supervision and inspection measures are not effective, the inspection and listing system is often difficult to implement in a better and longer-lasting manner, and there are frequent thefts, damages and other accidents that cannot be timely feedback and handled. The problem caused large economic losses and affected safe production and operation. At the same time, because the operating conditions of the field equipment are collected and processed by manual inspection and recording, the quality of data collection mainly depends on the professional quality of the workers. Due to differences in personnel, the inspection attitude and work ability of inspectors are not the same; especially in terms of inspection time, inspection route and inspection content, it is difficult to achieve quantitative management. After the inspection, the equipment inspection records are only filled in based on experience, and the records are missing Phenomenon also often occurs, which greatly reduces the reliability and authenticity of the data. At the same time, because this kind of data is highly dispersed and not real-time, human factors have a great influence on the accuracy and effectiveness of the data.
2. Introduction
Oilfield inspection Kenmax UHFRFIDThe handheld machine solves the following three important problems in the oilfield inspection work:
Inadequate inspections, missed inspections, or not on time. Manually reporting inspection results is inefficient, easy to miss items or make mistakes. It is difficult for managers to understand production and equipment conditions in a timely, accurate, and comprehensive manner, and it is difficult to formulate the best production, facility maintenance and repair plans.
Oilfield inspection Kenmax UHF RFID handsets can complete multiple functions such as daily inspection standardization, data recording standardization, work performance quantitative management, and accident responsibility query. This can greatly improve the inspection speed and comprehensive management level, which is mainly reflected in the following aspects:
Completely realize paperless: Realize completely paperless inspection work. Customization of inspection routes: inspection tasks can be flexibly configured in the background management system, devices can be added or deleted at any time, inspection points can be added and deleted, and the order of inspection points can be changed, so as to avoid turning people into slaves to equipment. When an emergency occurs, the inspection sequence can be adjusted in time or the inspection points can be added. Powerful anti-missing inspection function: In the system, once the inspection task is defined, if a missed inspection occurs during the inspection, the inspection equipment will promptly alarm to remind the inspectors and management personnel, thereby completely solving the inspection task. During the inspection process, there are problems of missed inspections that occur from time to time. Accurate patrol location: The GPS positioning function of Kenmax RFID handset can be used to monitor the patrol route of patrol personnel to prevent the occurrence of insufficient patrol inspection. Convenient data collection: Taking into account the fact that the inspectors have a lot of inspection content and heavy workload each time, the information collection operation on the inspection terminal is very simple. For status information, a selective entry method is adopted, and for digital information, a method of clicking on up and down arrows is adopted to select. It can shorten the recording time of inspection personnel to the greatest extent, reduce workload and improve work efficiency.
3. Scheme design
The plan was successfully designed by Nanjing Kenmax based on years of experience in the development of Internet of Things products. It combines modern intelligent oilfield inspection plans such as ultra-high frequency RFID (radio frequency electronic tag) technology, wireless communication technology, and information release technology.
UHF RFID solution for oilfield inspection
3.1 Intelligent inspection terminal
The patrol inspectors use the intelligent patrol terminal to collect and input the information of the on-site equipment. The terminal integrates functions such as device identification, data collection, and communication. The information collection method is flexible, and the collected information can be directly read by the intelligent inspection terminal or input by the operator. The information entered can be of any data type. Inspectors use Kenmax intelligent inspection terminal to scan and read the UHF RFID tags of the equipment on the spot, and they are allowed to receive field data after the UHF RFID information of the equipment is correctly obtained. When entering the data, the on-site intelligent inspection terminal has a data judgment function, which can be directly input or automatically read in according to the conditions of the site. The data collected on site can be returned to the patrol database server through GPRS or WI-FI wireless network or wired method.
3.2 Inspection management platform
The inspection management software adopts the B/S structure, the client computer does not need to install the software, and directly accesses the designated server, and the relevant operations can be carried out after the user name and password are verified. Through this system, you can complete the initialization of the oilfield intelligent inspection system, the establishment of the collected well or station index items, the formulation of the well or station inspection task, the real-time display of inspection information and status, the summary statistics daily report and the chart analysis, etc., and realize the oilfield Seamless connection of management integrated platform.
Fourth, the program function
Combining the current advanced communication technology with the inspection system, mainly integrating GPS, GPRS/CDMA, WIFI and other communication functions in the inspection terminal, providing a set of visual, networked, and real-time inspection management for the production scheduling department The system realizes real-time alarm and processing of inspection faults. Make the inspectors work closely with the production dispatching department to improve the monitoring and commanding ability, fault handling ability and work efficiency of the production dispatching department. Its main functions are mainly reflected in the following aspects:
Convenient and intuitive display of fault type and location. GPRS can be used to send on-site faults to the central station in time, and the system displays the location and type of faults in real time on the map. Dispatchers can easily and intuitively understand the faults in order to deal with them in a timely and accurate manner.
Real-time tracking of patrol personnel and limitation of patrol data entry. Through the use of GPS technology, wireless communication technology and GIS technology to complete the real-time tracking of inspectors. The location of inspectors can be displayed on an electronic map to complete real-time tracking, positioning, scheduling and monitoring of dynamic targets. (Need to be used in conjunction with the geographic information system) Through the configuration of the management software, it is stipulated that the field data can be entered only when the inspector enters the area of the inspected point (positioned by GPS), so as to prevent the inspector from falsifying the data.
The GPRS/CDMA network sends the surveyed data to the central database of the system in real time. Users can perform statistical analysis on the occurrence of faults in the database, and can take effective preventive measures for the safe production of oil production plants. Map query (need to be used in conjunction with geographic information system). It can provide a convenient method for freely querying and locating information about wells, pipelines, users, roads, stations, etc. For missed site wellheads, the electronic map can be used to remind management and related staff by flashing alarms. Remote task download and daily work arrangement/notification. Management dispatchers can send daily or a certain period of inspection work content (requirements) to the handheld terminals of each inspector through GPRS/CDMA, and can request a reply confirmation after receiving the task. When an inspection point or When the inspection requirements change, the change notification can also be sent through the GPRS/CDMA network in time, which greatly improves the efficiency and management of the inspection. At the same time, with the help of the network, it can also complete the management of daily work, such as sending relevant work arrangements in time, meeting notices, and so on. On-site picture collection and sending. For the more serious faults and problems that occur in the on-site inspection point, in addition to entering the text description of the problem, the high-resolution camera built in the inspection terminal can be used to store the photo or video data through GPRS/CDMA and it has begun to develop gradually. The 3G network and other related communication means send data to the database for management personnel to read, view and analyze.
[ad_2]