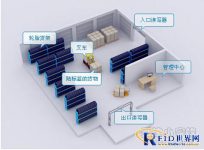
Tianjin Little Bee RFID Rubber Industry Warehouse Management Solution
[ad_1]
1. Program overview:
Use advanced RFID technology and WMS warehouse management system in the warehouse management of rubber enterprises to replace manual experience management mode, improve the operating efficiency of enterprises, use RFID technology to collect data, combine with the leading RFID application platform and services of Little Bee, and cooperate The resources of partners, the establishment of a powerful warehouse management information solution, and the real reason for the rubber enterprisesRFIDThe changes that have occurred. Integrate into the enterprise’s warehouse management business, so that RFID technology can maximize the benefits of warehousing, outgoing, inventory, moving, and allocation. RFID technology is used to maintain the accuracy and speed of data, and achieve the consistency of assets and information symmetry. . Enterprises can obtain insights into warehousing business from data, so as to make scientific decisions, maintain reasonable inventory, and further improve warehouse management.

2. Industry insights
This insight into the rubber industry is mainly focused on rubber production enterprises that produce general industrial rubber products such as tires and crawlers. The warehouse management business involved in production enterprises mainly includes raw material warehouse management, semi-finished products and finished product warehouse management. In the industry insight, it is found that related companies have many good equipment, but there are certain bottlenecks in the entire logistics link, and they are facing many problems. For example, backward management methods make inventory data inaccurate, information cannot be transmitted in real time, rubber product specifications are not accurate enough, and there is no accuracy and predictability of planned management. Inconsistent accounting results in distortion of data inventory data, resulting in providing customers Inaccurate delivery cycle of goods, material backlog or delayed delivery, etc. In the inventory of rubber products in the warehouse, there are usually large differences in quantity. After problem analysis, many of them are due to manual errors and management deficiencies.
3. Scheme design
The application of RFID in rubber warehouse management solutions is a combination of software, hardware, and services. It is designed according to the attributes of rubber companies to maximize customer needs. Attaching RFID electronic tags to the unit’s rubber products is equivalent to sending an electronic ID card to each item. The communication between the RFID electronic tag and the RFID reader can realize accurate and effective data collection, and then transmit it to the database. Reflected on the application of the system platform. When attaching labels, it is important to choose different label attachment schemes according to different types of goods and enterprises, which can be based on a pallet, a piece of goods, or a box. Use fixed and mobile RFID for key operations such as warehousing, outgoing, and inventoryReader, According to the warehouse management business plan, to realize the efficient data collection of the business process, the data will be sent to the database in real time, and the application software will display and statistically analyze the data. The manager can realize various data insights into the business through the application software. condition. The cargo and pallet information can be bound with the cargo location information, and warehouse operators can complete the process of finding goods and allocating more quickly and efficiently. In the construction of the overall solution, the accuracy of tag reading and the stability of the system are ensured, and the application can be highly expanded to ensure the applicability of RFID technology applications. At the same time, Little Bee attaches great importance to the user experience of system applications. All this is due to our industry insights into rubber companies and numerous customer relationships, combined with the experience accumulated by our diligent corporate character and the wisdom developed through cooperation with customers.
Four, system function
1. Warehouse management
In the warehousing management link, the warehouse manager reads the goods affixed with RFID electronic tags in the passage or at the gate according to the warehousing list generated in the system. The electronic tags have already entered the information before they are put into the warehouse, and they can also be in the warehouse. Initialize the label to store directly. Then put the goods on the storage location or shelf to be stored. The label of the goods or pallet also corresponds to the storage location of the storage location and shelf. The mobile RFID reader can realize the binding of the cargo location and the label. It is transmitted to the database via wireless network.
2. Outbound management
According to the pick-up plan, the goods out of the warehouse are sorted and processed and managed out of the warehouse. If the quantity out of the warehouse is large, push the goods to the door of the warehouse in batches, use a fixed reader to communicate with the tags, collect the RFID electronic tags of the goods out of the warehouse, and check whether they correspond to the plan. If there are errors, manually as soon as possible deal with. For a small amount of goods, RFID handheld terminals can be used to collect information from RFID electronic tags (handheld scanners or RFID tablet computers). When an error occurs, an alarm will be issued, and the staff should deal with it in time, and finally send the data to the management center Update the database to complete the delivery.
3. Inventory management
In accordance with the requirements of warehouse management, conduct regular and irregular inventory. The traditional inventory is time-consuming, labor-intensive, and error-prone. All these RFID solves these problems. When there is an inventory plan, the RFID handheld terminal is used to carry out inventory scanning, and the information of the inventory can be transmitted to the back-end database through the wireless network and carried out with the information in the database. Comparing, the generated difference information is displayed on the RFID handheld terminal in real time for verification by the inventory staff. After the inventory is completed, the inventory information is checked with the database information in the background, and the inventory is completed. In the inventory process, the system uses RFID non-contact reading (usually within 1 to 2 meters) to read clothing goods information very quickly and conveniently. Compared with the traditional model, it will improve a lot of efficiency and inventory accuracy. sex.
4. Basic information management
Set and manage the attributes of the goods, the main functions are, add, edit, delete, and query the basic attributes of the goods stored in the warehouse. In this way, it can be set according to the attributes of the operating products of different enterprises to ensure that it meets the individual needs of each enterprise. The warehouse can also be divided into locations, which can be divided into units such as warehouses, regions, and locations, so that large-scale warehouses can be managed more accurately. Warehouse managers at all levels can query and perform related business operations for inventory information of different dimensions.
5. System information management
Fully consider the scalability and security of the system, and provide reasonable tools to ensure system security. System management mainly completes the correction and maintenance of system operating parameters. Complete permissions assignment, add, modify, and delete data forms. At the same time, it has a complete login program (user name and password). Different personnel are given different permissions, which are set by the system administrator. The system also provides a one-key data backup and recovery function to further ensure the security and continuity of business data.
6. Data statistical analysis
The system can form statistical reports according to time, quantity and other elements, clarify the turnover period and efficiency, and facilitate the planning and control of the inventory management business process. The unified operation can speed up the speed of goods in and out of the warehouse, thereby increasing the throughput of the inventory center, and can provide Managers and decision makers provide timely and accurate inventory information, which can improve the accuracy of goods inquiries, reduce inventory levels, and improve the efficiency of the logistics system to strengthen the competitiveness of enterprises.
[ad_2]